Delta MMC120 User Manual
Page 10
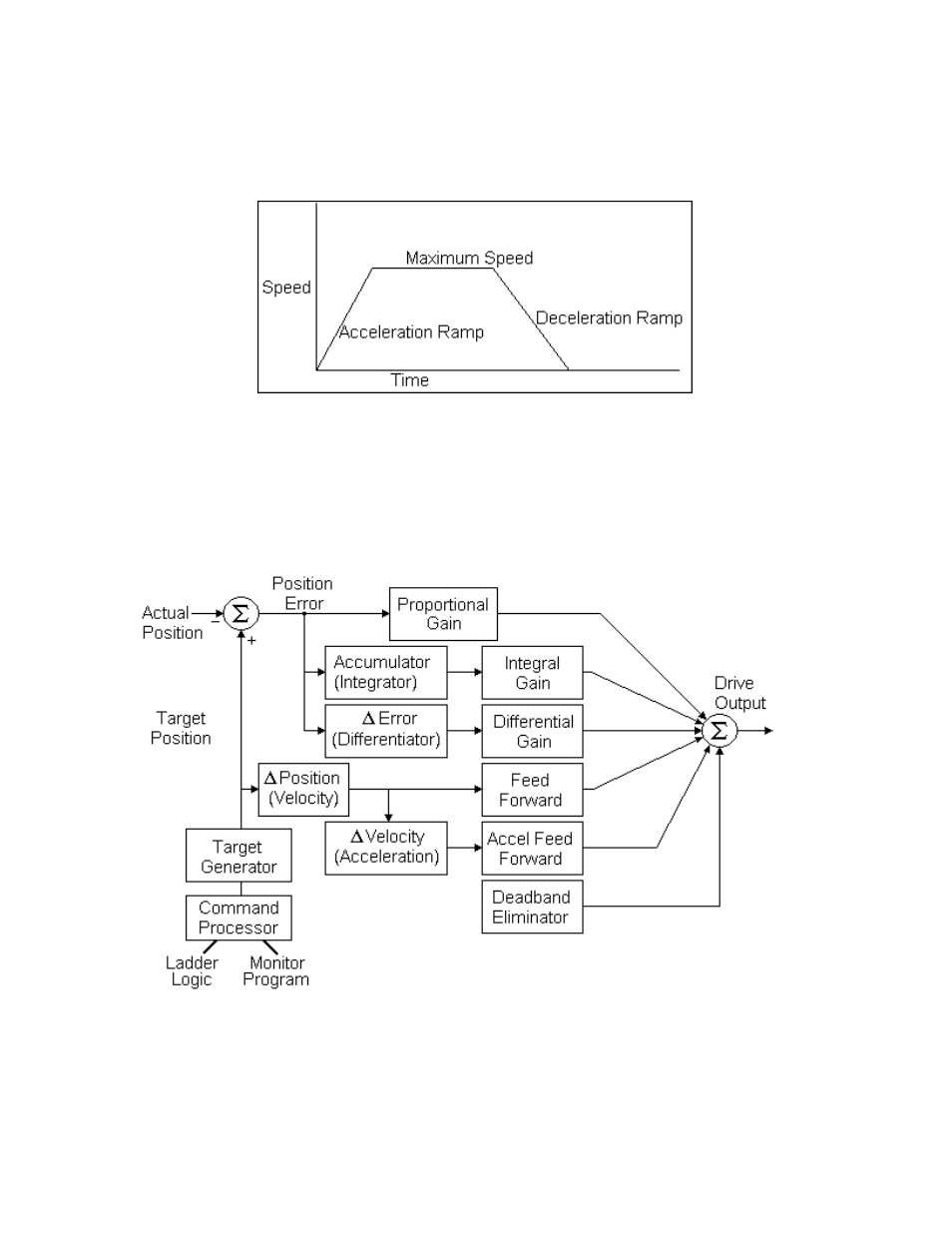
10
point-to-point moves,
TARGET POSITIONS
are generated so the target speed follows a
profile. The
MODE
,
ACCELERATION
,
DECELERATION
,
SPEED
, and
COMMAND
VALUE
(requested position) are used to generate the profile. They are specified by the
user, and can be changed while the axis is moving. A trapezoidal profile is shown here.
The
ACTUAL POSITION
measured by the magnetostrictive transducer is compared with
the
TARGET POSITION
to determine the position error. Every millisecond the position
error is used to calculate the closed loop components of the drive output. It is multiplied
by the
PROPORTIONAL GAIN
to calculate the proportional component of the drive
output. The accumulated position error is used, along with the
INTEGRAL GAIN
, to
calculate the integral portion of the drive output. The change in position error, along
with the
DIFFERENTIAL GAIN
, is used to calculate the differential portion of the drive
output.
In addition to the closed loop drive, this motion controller has two feed forward terms,
made up of
EXTEND
and
RETRACT FEED FORWARD
, and
EXTEND
and
RETRACT
ACCELERATION FEED FORWARD
. These feed forward terms give approximately
the drive needed to make the axis follow the target, freeing the PID loop to correct for
non-linearity in the system and changes in system load.