Integral gain – Delta MMC120 User Manual
Page 114
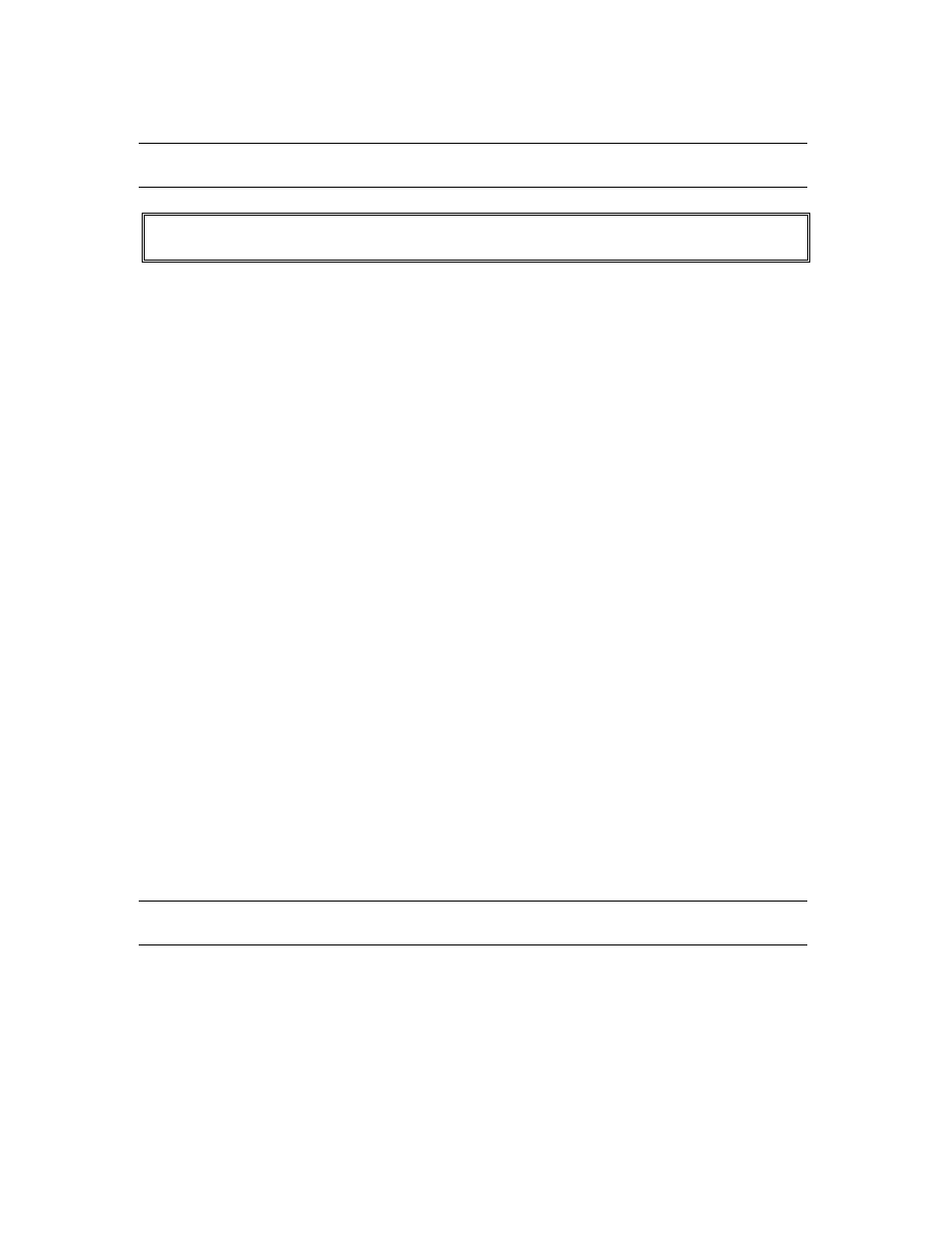
114
Proportional Drive = PROPORTIONAL GAIN x Position Error / 10
NOTE: The actual drive output may be reduced based on the values of the
Extend Feed
Forward
and
Retract Feed Forward
.
CAUTION: Increase the PROPORTIONAL GAIN gradually. Excessive gain can
cause oscillation that could cause damage or injury.
Think about this:
Internally, the motion controller must compare the error between the
TARGET
and
ACTUAL POSITIONS
with error limits to keep values from overflowing. The error
limit is the error at which full drive (10 volts) will occur. This internal error limit is
calculated as follows:
ERROR LIMIT = 100,000 / PROPORTIONAL GAIN
Therefore, if the PROPORTIONAL GAIN is set to 100, the ERROR LIMIT will be
1,000, which means any error greater than 1,000 will be treated as an error of 1,000 and
the OVERDRIVE error bit will be set in the
STATUS Word
.
INTEGRAL GAIN
Default: 1
Range: 0 to 65535
The INTEGRAL GAIN is used to control the amount of drive provided by the integrator.
The integrator adds the position error to an accumulator every millisecond. The
INTEGRAL GAIN should be adjusted after the feed forwards have been set to optimal
values. Using the integrator before the feed forwards have been set properly will cause
the system to overshoot the target. We recommend that you set the INTEGRAL GAIN to
a value of at least 50.
INTEGRAL GAIN is defined as:
INTEGRAL GAIN = 0.1 mV per 1024 counts of accumulated Position Error
Integral Drive is defined as:
Integral Drive = INTEGRAL GAIN x Accumulated Counts / 10240
NOTE: The actual drive output may be reduced based on the values of the
Extend Feed
Forward
and
Retract Feed Forward
.
Why Bother?
INTEGRAL GAIN should be used to compensate for the fact that loads may vary, valves
are non-linear and the axis may have trouble getting to the
COMMAND POSITION
without INTEGRAL GAIN.