Following error – Delta MMC120 User Manual
Page 118
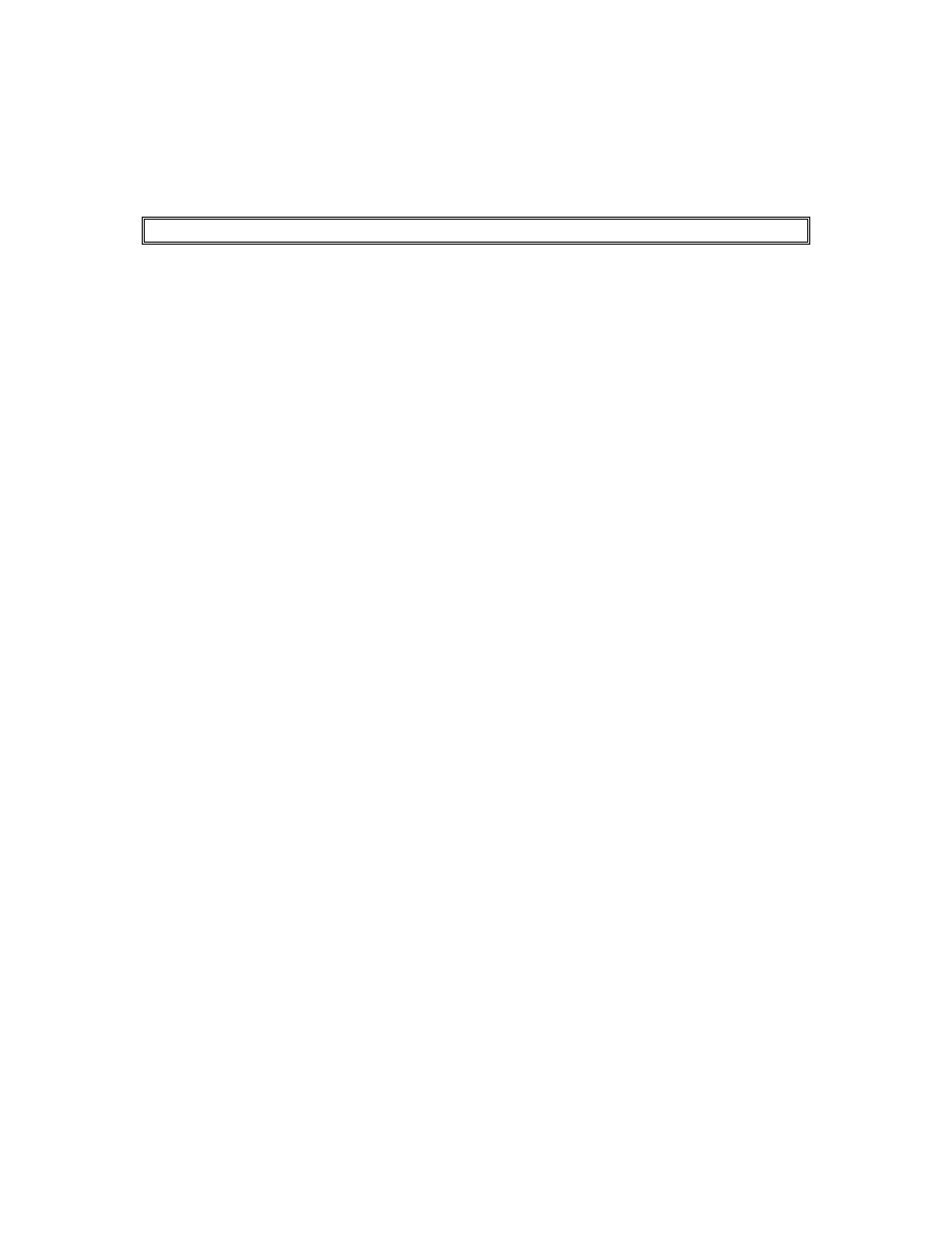
118
number of millivolts added to or subtracted from the drive output (depending on the
direction of travel) so the drive output is outside the dead band.
If a value outside the valid range is entered, the parameter error bit will be set, and the
value will be set to zero.
CAUTION: Do not make this value too large or the drive will oscillate.
Why Bother?
On an axis with overlapped spools or a large amount of static friction, the axis may
oscillate slowly around the
COMMAND POSITION
. This happens when the axis does
not respond to small changes in drive output. The integrator winds up until the axis
moves and then has too much drive, overshooting the
COMMAND POSITION
. The axis
then winds the integrator down until the axis overshoots the other way. If this happens,
look at the
NULL DRIVE
. The
NULL DRIVE
will oscillate slowly as the axis oscillates.
Notice the peak-to-peak values of the
NULL DRIVE
oscillation and subtract the
minimum value from the maximum value and then divide the result by two. Enter this
value in the DEAD BAND ELIMINATOR field as a starting point.
A spool that has 10% overlap will require a value of about 1,000 counts.
IN POSITION
Default: 50
Range: 0 to 65535
IN POSITION specifies the size of a window around the
COMMAND POSITION
.
When the
ACTUAL POSITION
gets within this window, the In Position bit is set (but
not latched) in the word.
Example:
If an axis
COMMAND POSITION
is 10,000 and the IN POSITION parameter is 30, the
In Position bit will be set when the
ACTUAL POSITION
is between 9,971 and 10,029.
The bit will be cleared whenever the
ACTUAL POSITION
is outside the range.
FOLLOWING ERROR
Default: 250
Range: 0 to 65535
The FOLLOWING ERROR determines how large the difference between the
TARGET
POSITION
and
ACTUAL POSITION
can get before the Following Error bit is set in the
word.