Target position, Actual position – Delta MMC120 User Manual
Page 123
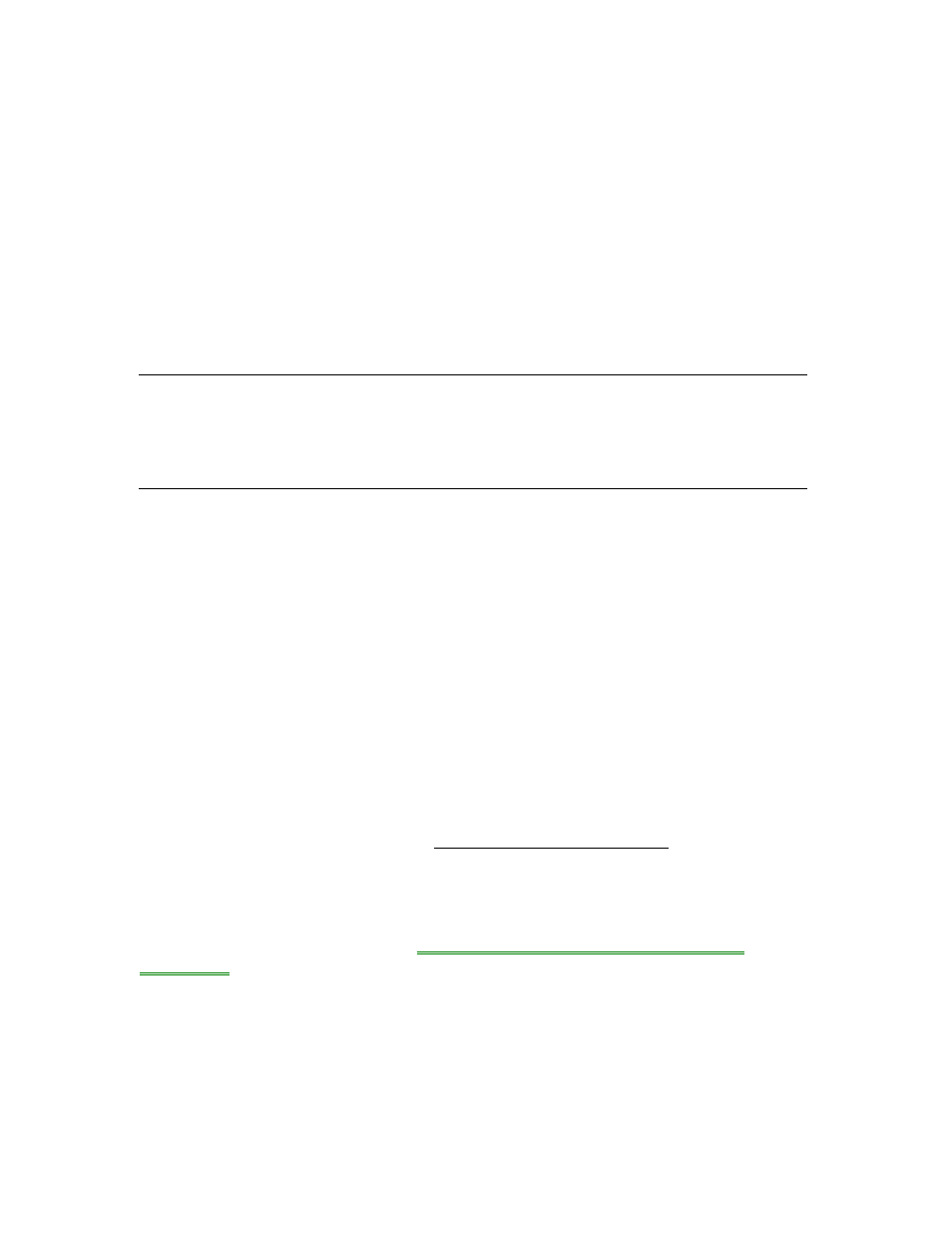
123
TARGET POSITION
When the axis is in
Closed Loop Mode
, the TARGET POSITION is the calculated
instantaneous ideal position for the axis. The TARGET POSITION is calculated every
loop by the
target generator
state machine of the on-board motion control program. The
PID
routine uses the difference between the TARGET POSITION and the
ACTUAL
POSITION
as its input to compute any required corrective drive.
During a move the transition of the TARGET POSITION toward the
COMMAND
POSITION
will be the perfect profile for the
ACTUAL POSITION
to follow.
NOTE: When an axis is stopped, the TARGET POSITION should be the same as the
COMMAND POSITION
unless an error or HALT has occurred (see
STATUS
).
NOTE: When an axis is not in position Closed Loop Mode, TARGET POSITION is
set to the ACTUAL POSITION.
Why Bother?
Knowing the relationship between the TARGET POSITION and
ACTUAL POSITION
is
key to tuning the axis. The main goal in tuning the axis is to minimize the error between
the TARGET and
ACTUAL POSITIONS
. The plot function is a very nice visual aid in
tuning the axis.
ACTUAL POSITION
The ACTUAL POSITION is the measured position of the axis at any moment. This
position is updated every loop. The ACTUAL POSITION is calculated from the
TRANSDUCER COUNTS
as follows:
ACTUAL POSITION =
TRANSDUCER COUNTS x SCALE
+ OFFSET
32768
Why Bother?
Before applying drive or hydraulic power, make sure the target position is set to the
actual position using a
‘ P’ command. Otherwise axis will jump to the TARGET
POSITION.
See
TARGET POSITION
.