7 troubleshooting/diagnostics, 1 general, 2 wiring errors – Rockwell Automation FlexPak 3000 Power Module SW-Version 4.3 User Manual
Page 73: 3 ac line and power input, 4 dc motor
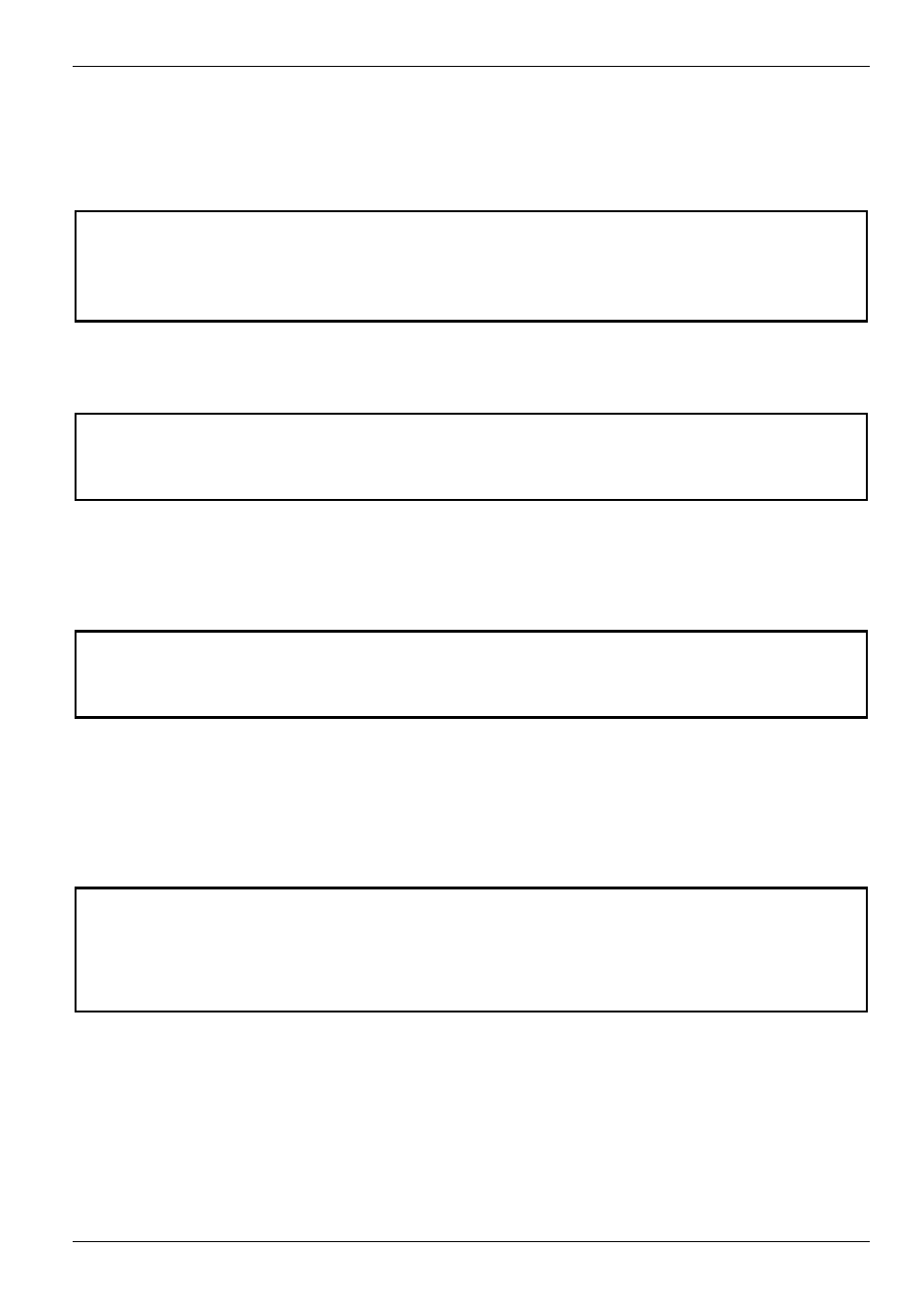
TROUBLESHOOTING/DIAGNOSTICS
49’1340 e
FlexPak 3000
7-1
7.0 Troubleshooting/Diagnostics
7.1 General
DANGER
Only qualified electrical personnel familiar with the construction and operation of this equipment and
the hazards involved should install, adjust, operate and/or service this equipment. Read and
understand this section in its entirety before proceeding. Failure to observe this precaution could result
in severe bodily injury or loss of life.
This section details troubleshooting and diagnostics information for the FlexPak 3000 Drive.
7.2 Wiring
Errors
DANGER
This equipment is at line voltage when AC power is connected. Disconnect and lockout all ungrounded
conductors of the AC power line before checking wiring. Failure to observe this precaution could result
in severe bodily injury or loss of life.
Wiring errors and loose or grounded wiring are common problems that can inhibit operation of a
drive. Verify the installation wiring has been correctly executed and that the drive is free of loose
terminations and grounded conductors.
7.3
AC Line and Power Input
DANGER
This equipment is at line voltage when AC power is connected. Exercise extreme care when checking
the AC line and power input. Failure to observe this precaution could result in bodily injury or loss of
life.
Verify that the applied AC power is correct for the specific drive (refer to 2.1.2 and 2.2.3). If an
isolation transformer has been installed on the incoming AC power, verify its output voltage and
that it has been properly connected. Verify that the AC line fuses are semiconductor protection
type and have been correctly sized per Table 8-7. The AC and DC power conductors should
have been sized per local standards.
7.4 DC
Motor
CAUTION
A megohmmeter (megger) can be used for this motor ground check, but all conductors between the
motor and the drive must be disconnected. The megger's high voltage can damage the drive's
electronic circuits. Disconnect all conductors between the motor and the drive before using a megger
for this motor ground check. Failure to observe this precaution could result in damage to, or
destruction of, the equipment.
Recheck all motor connections for tightness and correct identification. Verify that there is no
path to ground in either the DC motor armature circuit, the shunt field circuit or the thermostat
circuit. Connect one lead of a standard ohm meter to the motor frame and the other lead to the
two armature leads. then connect to the two thermostat leads and then to the two field leads.
If a reading of less than 100,000 ohms is observed, a ground condition exists and MUST be
corrected before power is applied. Check that the field winding is not open or shorted.
Verify the continuity of the motor thermostat and its proper connection to regulator board
terminals 13 and 14. If a motor thermostat has been installed, verify that it's circuit maintains
continuity in the terminal 13 and 14 circuit.