Rockwell Automation FlexPak 3000 Power Module SW-Version 4.3 User Manual
Page 156
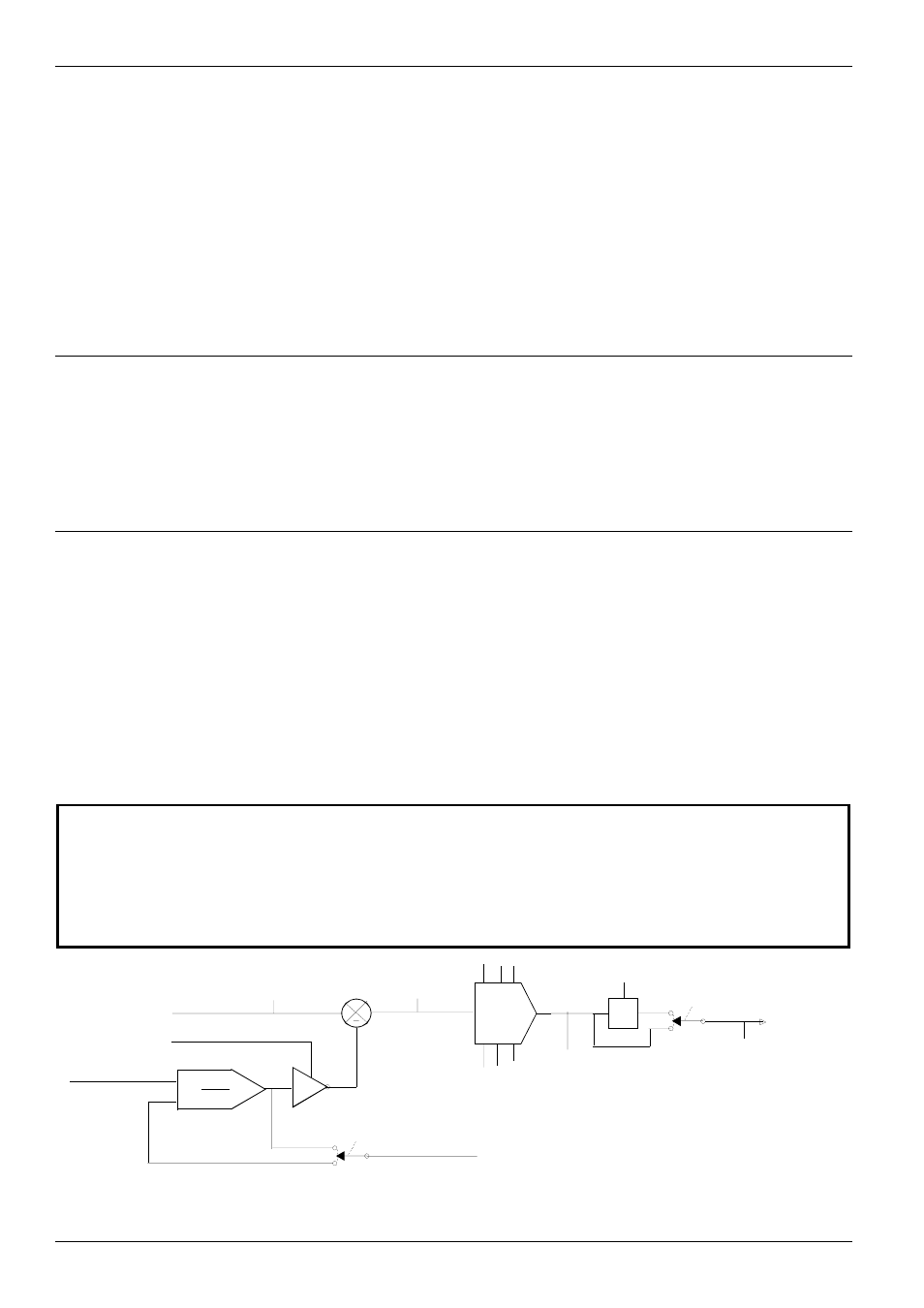
APPENDIX B
FlexPak 3000
49’1340
e
B-52
OIM Menu Path(s):
Drive Reference - Drive Reference Trim
The choices are:
•
REGISTER: The reference is TRIM REF REGISTER (P.107)
•
ANALOG MANUAL: The reference is the analog manual reference input from terminals 16, 17,
and 18 of the Regulator board. Do not select this option if this input is being used for the analog
manual speed reference.
•
ANALOG IN 1 or 2: The reference is from an I/O Expansion kit analog input. These are only
available if an I/O Expansion kit is installed.
•
NETW IN REG 1, 2, or 3: The reference is from a network input register. These options are
available only if a network kit is installed. Note that the network input registers are updated only
when CONTROL SOURCE SELECT (P.000) is set to network and the network is active.
TRIM REF REGISTER (P.107)
Drive register to manually set the trim reference value used by the drive.
Parameter Range:
+100.0%
Default Setting:
0%
Parameter Type:
Tuneable
OIM Menu Path(s):
Drive Reference - Drive Reference Trim
UNDERWIND ENABLE (Alternate network map, Drop_1, register 32, Bit 5)
Setting this bit to 1 enables two inverter blocks that permit underwind operation.
Setting this bit to 0 disables the two inverter blocks and permits overwind operation.
Parameter Range:
0 = DISABLED (overwind)
1 = ENABLED (underwind)
Default Setting:
0
Parameter Type:
Configurable
OIM Menu Path(s):
This parameter is available over the network, alternate network map,
drop_1, register 32, bit 5. It cannot be viewed through the
OIM
or
DCM
.
To use this register,
CONTROL SOURCE
SELECT must be set to
NETWORK
and
NETW REGISTER MAP
SEL
(P.914) must be set to
ALTERNATE.
The inverters are added to the speed loop block and the current minor loop reference block.
ATTENTION:
If
CONTROL SOURCE
is changed from
NETWORK
to any other control source, the
UNDERWIND ENABLE
bit is forced to the default if DISABLED. If the setting was
ENABLED
and
CONTROL
SOURCE
is changed from
NETWORK
, the motor rotates in the opposite direction when the drive is
restarted. The active speed reference should be set to zero before starting the drive from the new
control source. Slowly increase the speed reference until the proper rotation direction can be
determined. If it is incorrect, change the setting of the
FORWARD/REVERSE
input. The active speed
reference is based on the new control source and the
AUTO/MANUAL
setting.
From Speed Reference
Mode Select Block Diagram
(SPD LOOP REFERENCE)
(SPD LOOP ERROR)
+
D.5(E)
P.295
P.297
MUL
IN
A * B
1000
UNDERWIND ENABLE 1)
Netw. Drop 1, Reg. 32, Bit 5
SPEED FEEDBACK GAIN 1)
Netw. Drop 1, Reg. 38
KEYPAD,
TERMBLK
or SERIAL
EN
To CML Reference
Block Diagram
(SPD LOOP OUTPUT)
PI
KP HI
WLD LO
P.299
INIT
RST
SPD LOOP LAG FREQ
SPD LOOP
LAG BYPASS
WLG
LAG
(SPD LOOP
LAG OUTPUT)
P.215
P.217
P.298
OFF
*ON
OUT
NETWORK
P.000 CSS