Establishing planned downtime – Lincoln Electric IM8000 CHECKPOINT User Manual
Page 124
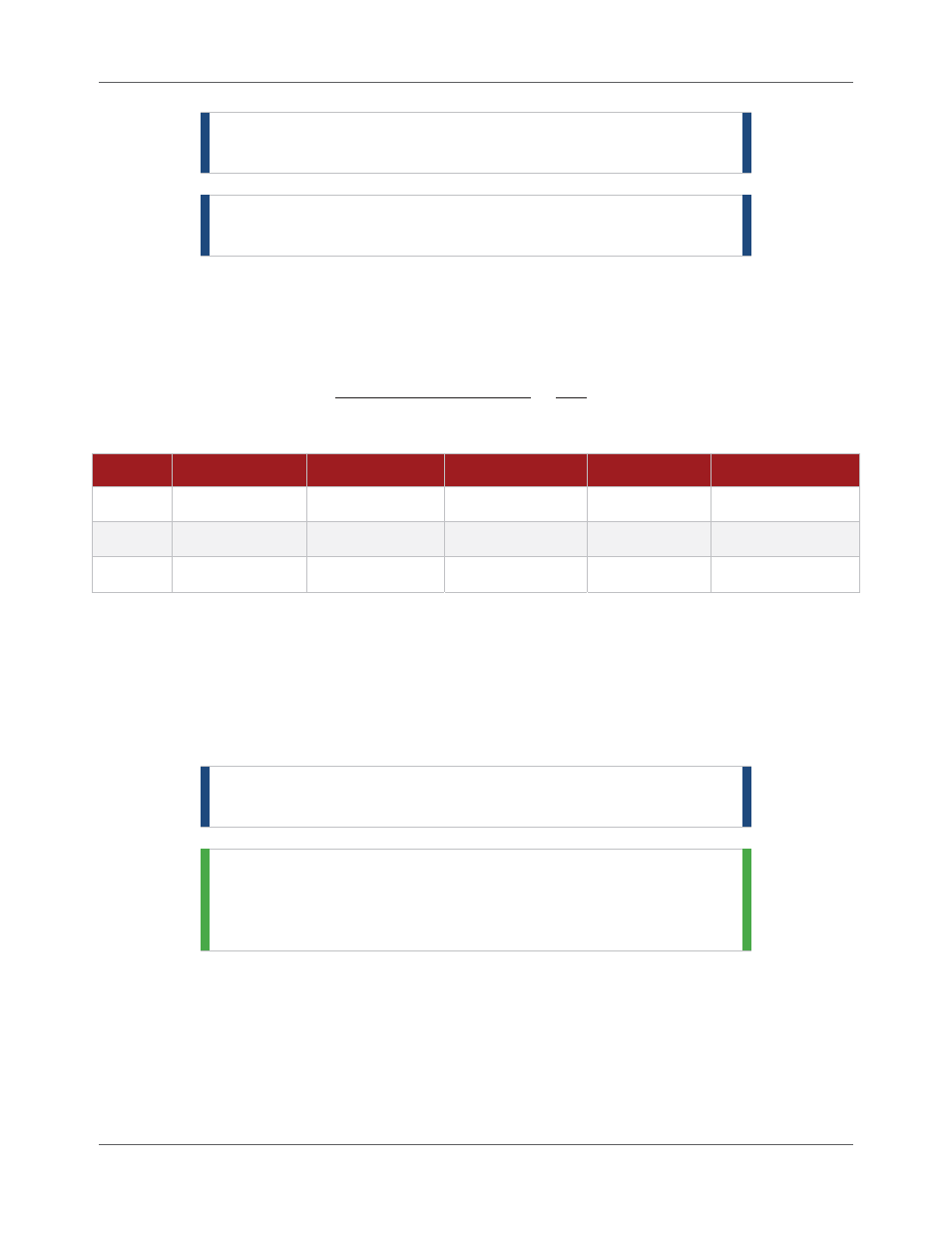
Chapter 9. Overall Equipment Efficiency (OEE)
Establishing Planned Downtime
9.10 CheckPoint™
User
Manual IM8000
NOTE |
The
Sum of Normalized Limits uses limits, not welds. A
single weld could have three (3) limits enabled.
NOTE |
WeldScore™ uses the actual WeldScore™ value from the
weld as a decimal (e.g., 0.96 for 96%).
Total Limits Enabled is the total number of limits that were enabled for the welds performed during the
selected time period. If there were three welds during a selected time period with the limits enabled as
outlined in Table 9.3, the Total Limits Enabled would be “8”.
The resulting Quality factor would be:
ܳݑ݈ܽ݅ݐݕ =
ܵݑ݉ ݂ ܰݎ݈݉ܽ݅ݖ݁݀ ܮ݅݉݅ݐݏ
ܶݐ݈ܽ ܮ݅݉݅ݐݏ ܧܾ݈݊ܽ݁݀
=
5.96
8
× 100 = 75%
Table 9.3
Example Welds
Weld
WeldScore™
Weld Duration
Amperage
Voltage
Wire Feed Speed
Weld 1
Enabled 0.96
Disabled
Disabled
Disabled
Disabled
Weld 2
Disabled
Enabled
0 Enabled
0 Enabled
1 Enabled
1
Weld 3
Disabled
Enabled
1 Enabled
1 Enabled
1
Disabled
Establishing Planned Downtime
CheckPoint™ uses Planned Downtime to calculate the Availability factor. In order for CheckPoint™ to
calculate your Availability factor as accurately as possible, you should define your plant’s expected
downtimes, from employee breaks to scheduled maintenance. You also need to define those times at the
Company Site level where no shift is running. You can define Planned Downtime starting at the plant level
all the way down to the individual Welding Power Source.
NOTE |
Planned Downtime takes precedence over all other time,
including Disconnected time.
TIP |
When you first begin with OEE, you may want to set the
bare minimum Planned Downtimes and analyze your data
after a few weeks. You can then begin to refine the
Planned Downtimes listed in CheckPoint™ as needed.