Electronic operation, Overview – Teledyne GFC-7000T - Trace CO2 Analyzer - manual User Manual
Page 215
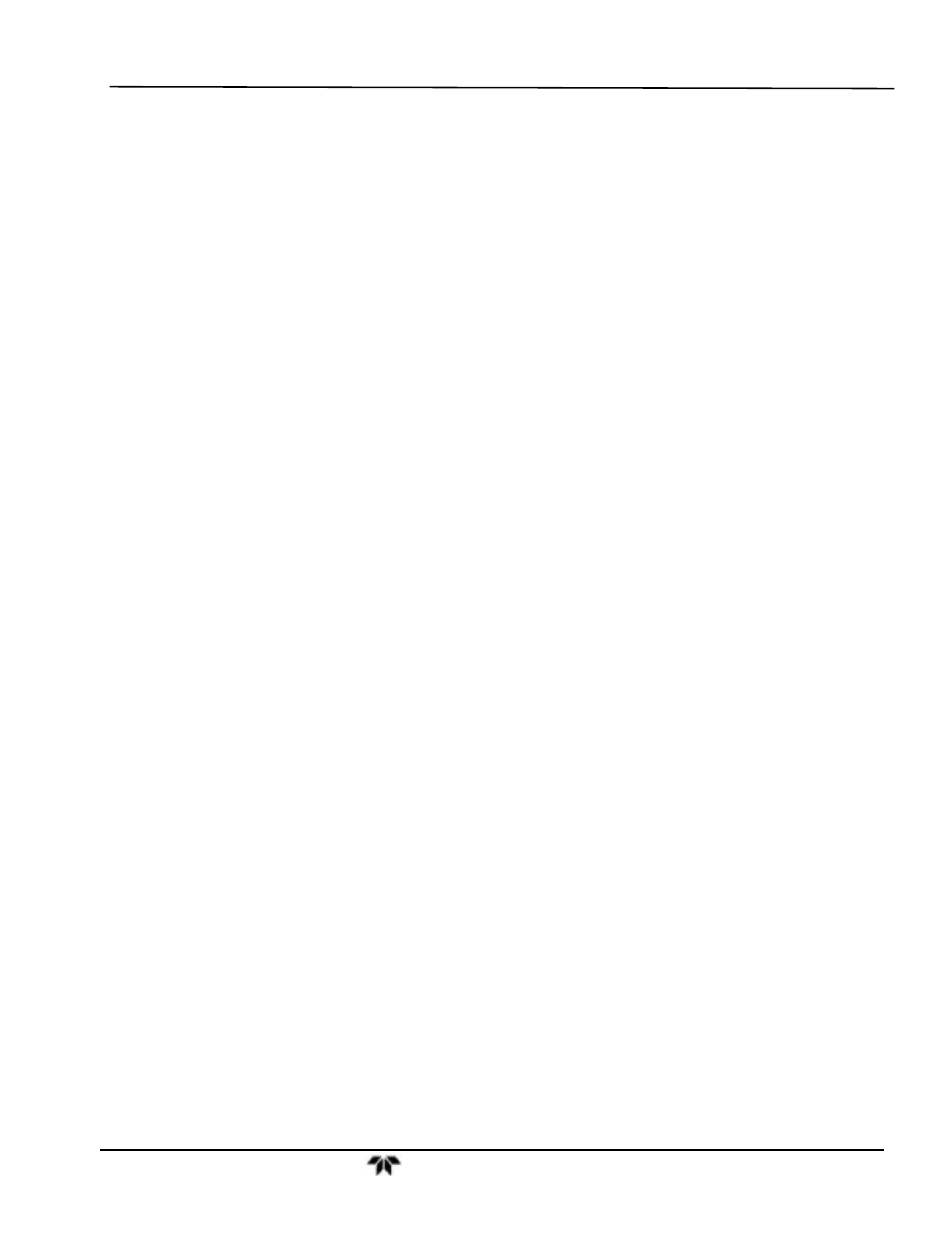
Theory of Operation
Model GFC7000TA Carbon Dioxide Analyzer
Teledyne Analytical Instruments
197
9.3. Electronic Operation
9.3.1. Overview
Figure 10-9 shows a block diagram of the major electronic components of the Model GFC 7000TA.
The core of the analyzer is a microcomputer/central processing unit (CPU) that controls various internal
processes, interprets data, makes calculations, and reports results using specialized firmware developed
by Teledyne Instruments. It communicates with the user as well as receives data from and issues
commands to a variety of peripheral devices via a separate printed circuit assembly called the Mother
Board.
The mother board, directly mounted to the analyzer’s inside rear panel, collects data, performs signal
conditioning duties and routs incoming and outgoing signals between the CPU and the analyzer’s other
major components.
Data is generated by a gas-filter-correlation optical bench which outputs an analog signal corresponding
to the concentration of CO
2
in the sample gas. This analog signal is transformed into two, pre-amplified,
DC voltages (CO2 MEAS and CO2 REF) by a synchronous demodulator printed circuit assembly. CO2
MEAS
and CO2 REF are converted into digital data by a unipolar, analog-to-digital converter, located on
the mother board.
A variety of sensors report the physical and operational status of the analyzer’s major components, again
through the signal processing capabilities of the mother board. These status reports are used as data for
the CO
2
concentration calculation and as trigger events for certain control commands issued by the CPU.
They are stored in memory by the CPU and in most cases can be viewed but the user via the front panel
display.
The CPU communicates with the user and the outside world in a variety of manners:
Through the analyzer’s touchscreen and LCD display over a clocked, digital, serial I/O bus (using a
protocol called I
2
C)
RS 232 & RS485 Serial I/O channels via Ethernet, Modbus
®
, Apicom or a terminal emulation program
Various DCV and DCA analog outputs, and
Several sets of Digital I/O channels.
Finally, the CPU issues commands via a series of relays and switches (also over the I
2
C bus) located on
a separate printed circuit assembly to control the function of key electromechanical devices such as
heaters, motors and valves.