Parameters a - 19, Ai-14 setup, Table a.1 f7 parameter list (continued) – Yaskawa F7 Drive User Manual User Manual
Page 184
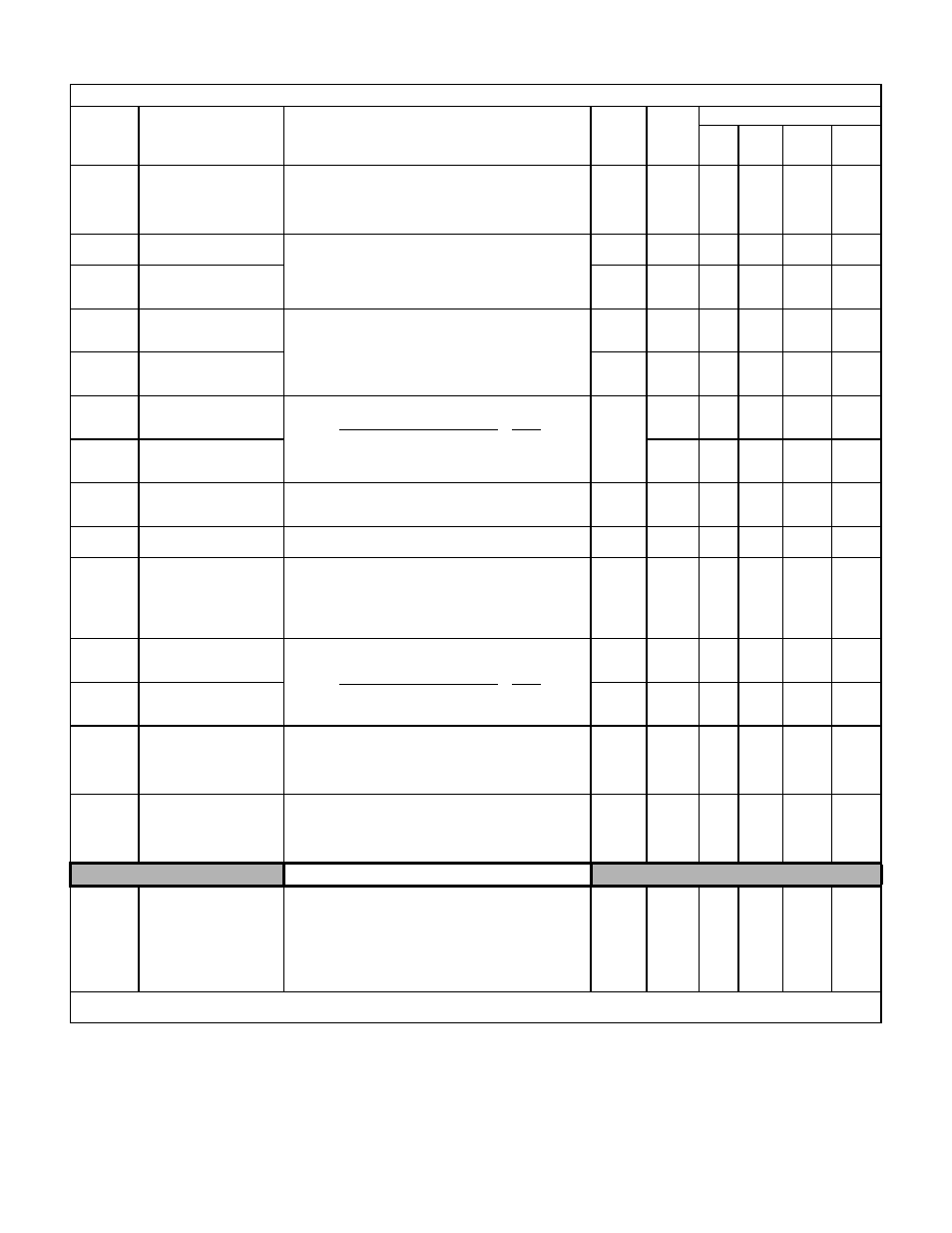
Parameters A - 19
F1-07
Integral Function During
Accel/Decel Selection
PG Ramp PI/I Sel
Sets integral control during acceleration/deceleration to either
enabled or disabled.
0: Disabled - The integral function is not used while accelerating
or decelerating.
1: Enabled - The integral function is used at all times.
0 to 1
0
-
A
-
-
F1-08
Overspeed Detection Level
PG Overspd Level
Configures the overspeed fault (OS) detection.
OS fault will occur, if the motor speed feedback is greater than the
F1-08 setting for a time longer than F1-09. F1-08 is set as a
percentage of the maximum output frequency (E1-04). See F1-03.
0 to 120
115%
-
A
-
A
F1-09
Overspeed Detection Delay
Time
PG Overspd Time
0.0 to 2.0
0.0 sec
-
A
-
A
F1-10
Excessive Speed
Deviation Detection Level
PG Deviate Level
Configures the speed deviation fault (DEV) detection.
DEV fault will occur if the speed deviation is greater than the
F1-10 setting for a time longer than F1-11. F1-10 is set as a
percentage of the maximum output frequency (E1-04).
Speed deviation is the difference between actual motor speed and
the frequency reference command. See F1-04.
0 to 50
10%
-
A
-
A
F1-11
Excessive Speed
Deviation Detection Level
PG Deviate Level
0.0 to
10.0
0.5 sec
-
A
-
A
F1-12
Number of PG
Gear Teeth 1
PG # Gear Teeth1
Sets the gear ratio between the motor shaft and the encoder (PG).
A gear ratio of 1 will be used if either of these parameters is set to 0.
This function is not available in flux vector control.
0 to 1000
0
-
A
-
-
F1-13
Number of PG
Gear Teeth 2
PG # Gear Teeth2
0
-
A
-
-
F1-14
PG Open-Circuit
Detection Time
PGO Detect Time
Configures the PG open (PGO) function. PGO will be detected if no
PG pulses are detected for a time longer than F1-14. See F1-02.
0.0 to
10.0
2.0 sec
-
A
-
A
F1-21
<3021>
PG Constant 2
PG Pulse / Rev 2
Sets the number of pulses for the encoder (pulse generator) for each
full rotation of Motor 2.
0 to
60000
1024
No
Q
No
Q
F1-22
<3021>
PG Rotation 2
PG Rotation Sel2
Determines the direction of rotation for the encoder (PG) connected
to Motor 2.
0: Phase A leads with Forward Run Command.
(Phase B leads with Reverse Run Command.)
1: Phase B leads with Forward Run Command.
(Phase A leads with Reverse Run Command.)
0, 1
0
No
Q
No
Q
F1-23
<3021>
Number of PG
Gear Teeth 1
PG Gear Teeth1
Sets the number of gear teeth (deceleration ratio) between Motor 2
and the pulse generator.
A gear ratio of 1 will be used if either of these constants is set to 0.
0 to 1000
0
No
A
No
No
F1-24
<3021>
Number of PG
Gear Teeth 2
PG Gear Teeth2
0 to 1000
0
No
A
No
No
F1-25
<3021>
Hardware Disconnect
Detection Selection CH 1
Hardware PGO ch1
Enables or disables the drive from detecting when the PG option on
CH1 has been disconnected.
0: Disabled
1: Enabled
Enabled when using PG-T2 or Z2.
0, 1
1
No
A
No
A
F1-26
<3021>
Hardware Disconnect
Detection Selection CH 2
Hardware PGO ch2
Enables or disables the drive from detecting when the PG option on
CH2 has been disconnected.
0: Disabled
1: Enabled
Enabled when using PG-Z2.
0, 1
1
No
A
No
A
AI-14 Setup
F2-01
AI-14 Input Selection
AI-14 Input Sel
Sets the function for channel 1 to 3 of the AI-14B analog input
reference option board.
0: 3-channel individual (Channel 1: terminal A1, Channel 2:
terminal A2, Channel 3: terminal A3)
1: 3-channel addition (Summed values of channels 1 to 3 is the
frequency reference)
When set to 0, select 1 for b1-01. In this case, the multi-function
input “Option/Inverter selection” cannot be used.
0 to 1
0
A
A
A
A
Denotes that parameter can be changed when the Drive is running.
* Enabled when an option card is connected to the PG encoder 2CH input (F1-21 to F1-24).
Table A.1 F7 Parameter List (Continued)
Parameter
No.
Parameter Name
Digital Operator Display
Description
Setting
Range
Factory
Setting
Control Method
V/F
V/F
w/PG
Open
Loop
Vector
Flux
Vector
Input pulses from PG (PPR) x 60
F1-01
F1-13
F1-12
x
Input pulses from PG (PPR) x 60
PG Constant (F1-21)
F1-24
F1-23
x