Health concerns, Laser safety eyewear (lse), Acoustical noise – Hypertherm HyIntensity Fiber Laser Rev.3 User Manual
Page 19: Warning signs, Gas, fumes and air quality
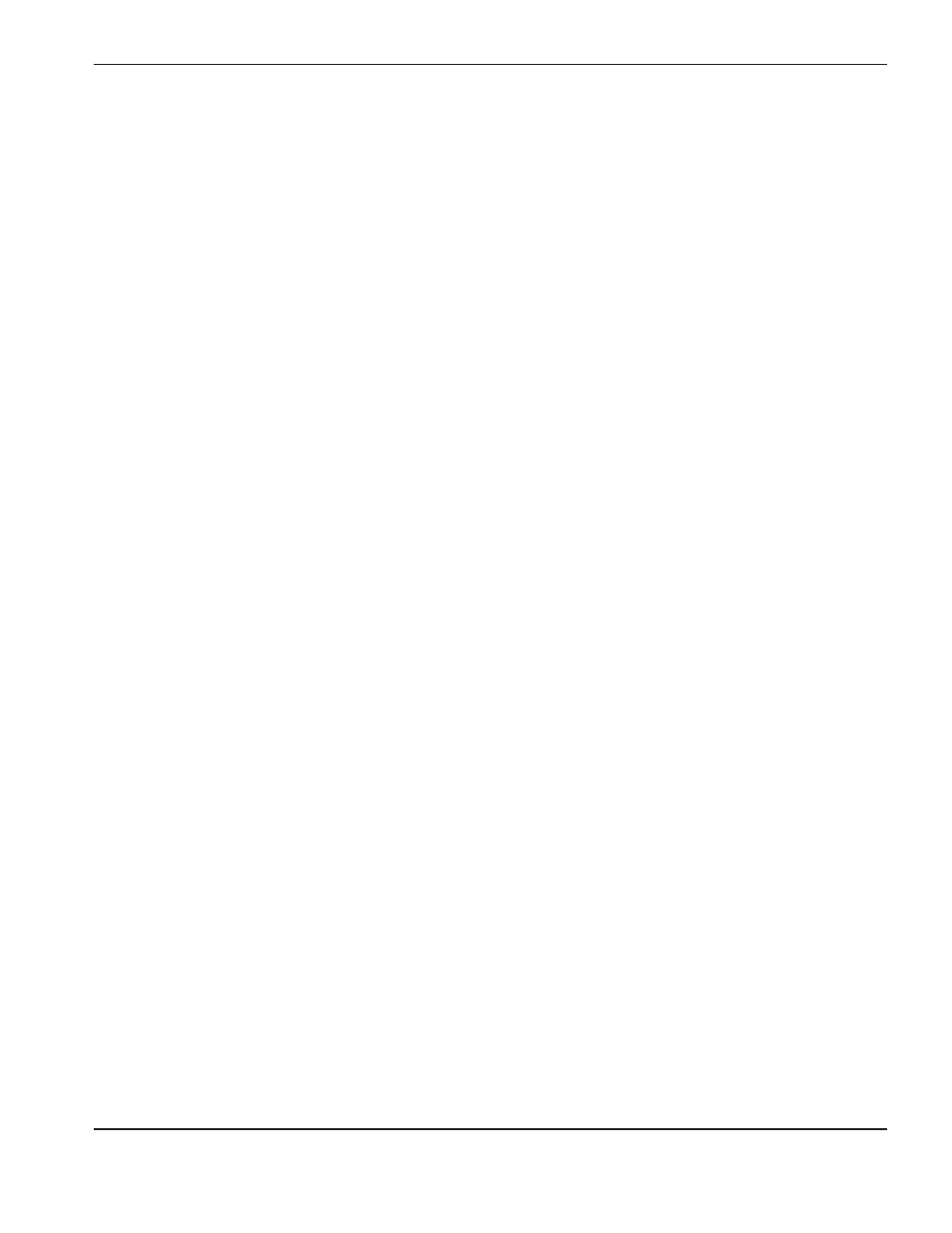
safety
H
ypertherm Fiber Laser
Instruction Manual – 807090 Revision 3
S-9
During installation it is vital that the laser hazard is fully managed. In particular, the machine builder is required to
implement the engineering requirements detailed in IEC/EN 60825-1. Based on the evaluation or certification of the
final laser cutting system, additional laser safety warnings may be provided by the machine builder or by the laser safety
officer at the installed site.
Health concerns
Personnel assigned to operate or maintain laser beam cutting equipment shall have been properly trained by the
machine builders representative or by a qualified instructor and shall understand the safety requirements of metal cutting
using lasers.
Laser safety eyewear (LSE)
Laser safety eyewear (LSE) is designed to reduce the amount of incident light of specific wavelengths to a safe level,
while transmitting sufficient light for good vision. As LSE often looks alike in style and color, it is important to specifically
check both the wavelength and optical density imprinted on all LSE prior to laser use, especially in multi-wavelength
facilities where more than one laser may be located. In the USA reference to ANSI Z136.1 is recommended for the
selection of appropriate eye wear to protect against reflections of laser radiation.
Acoustical noise
The noise generated by laser beam welding, cutting, or gouging may impair hearing. Hearing protection shall be worn
where the noise level exceeds limits as specified by the regulatory authority having jurisdiction Since operators and
nearby personnel can be exposed to noise levels in excess of 85 dB(A), it is important that their hearing be protected.
The most direct way to control excessive noise is to reduce the intensity at the source or install barriers in the final laser
cutting system between the source and the operator station(s). When engineering or administrative control methods
fail to bring noise exposure within levels established by the appropriate regulatory authority having jurisdiction, personal
protective devices such as earmuffs or earplugs shall be used. It is the responsibility of the machine builder and the
body responsible for the implementation of workplace / laser safety at the installed site to measure the acoustical noise
in application and ensure personnel are protected from noise levels that exceed limits.
Warning signs
Warning signs shall be posted in conspicuous areas to indicate laser and cutting hazards. The signs shall indicate the
need for the appropriate types of protective equipment.
Gas, fumes and air quality
Fumes and gases are generated by removal of metal from the workpiece being cut during laser beam cutting. The body
responsible for workplace / laser safety at the installed site needs to control the materials being cut. Before cutting any
unfamiliar materials or using any unfamiliar cleaning materials, the Material Safety Data Sheet (MSDS) shall be read to
determine whether any hazards may exist when the material removed will be converted to a gas by laser cutting.
Personnel shall not be exposed to concentrations of airborne contaminants above acceptable limits as established by
the authority having jurisdiction. The most direct way to control fumes and gases is by ventilation. Air Quality permits
may be needed to release fumes outside the building. Consult a local expert for information on local air quality permits,
ventilation and fume extraction. Where ventilation alone cannot protect personnel, appropriate personal respiratory
protection shall be used as required by the authority having jurisdiction. Where respirators are employed, requirements
for the selection and use of respirators shall include, as a minimum, the following:
A. Written procedures for the proper care, use, maintenance, and storage of respirators shall be provided, and the
employer shall ensure that these procedures are followed. These procedures shall be developed and set down
in writing in consultation with the joint health and safety committee or the health and safety representative, as
applicable; and made readily accessible, along with related schedules, to the welder and welding personnel.