Laser cutting, Mild steel – oxygen assisted, Laser cutting -38 – Hypertherm HyIntensity Fiber Laser Rev.3 User Manual
Page 146: Mild steel – oxygen assisted -38
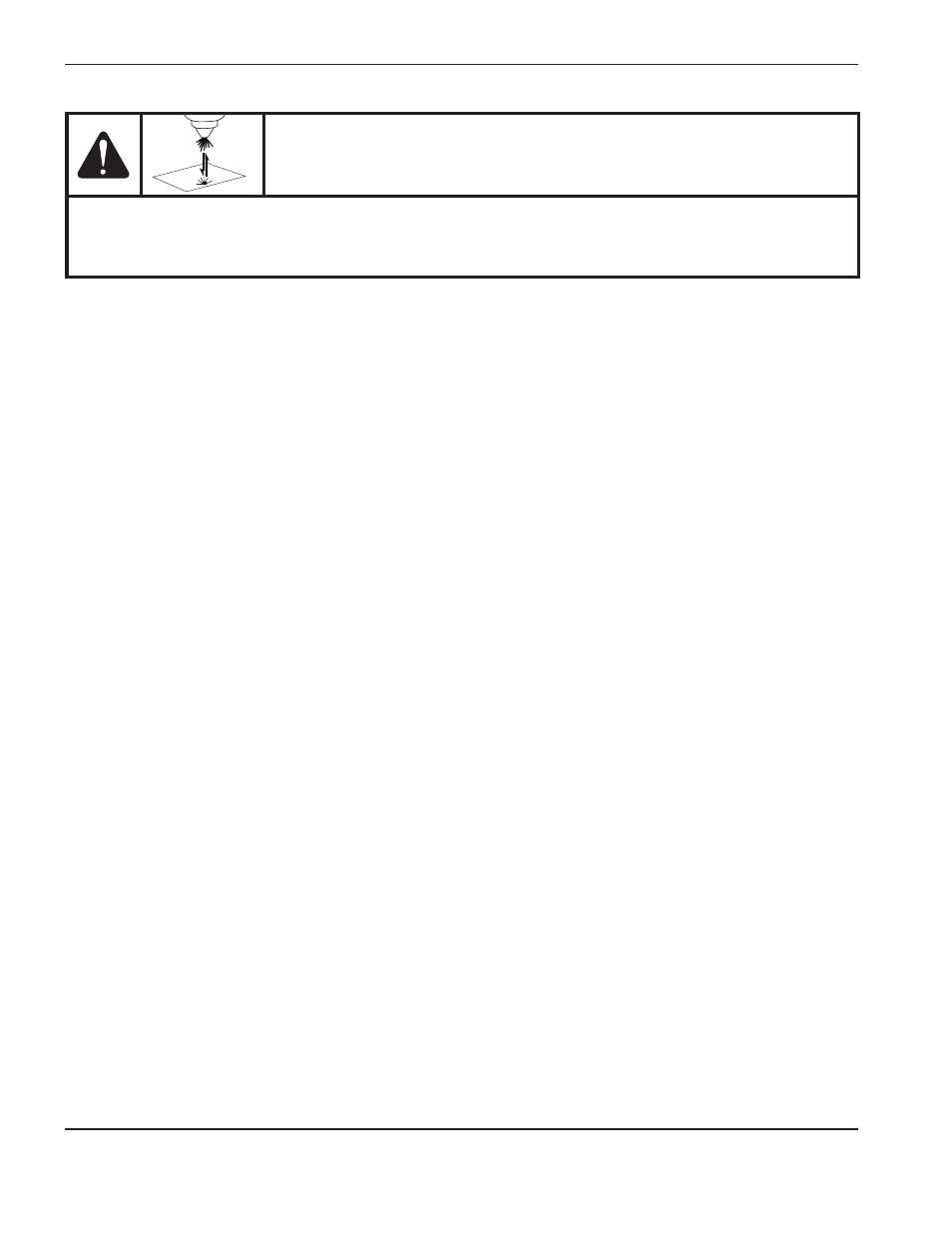
setup and OperatiOn
3-38
Hypertherm Fiber Laser
Instruction Manual – 807090 Revision 3
Laser Cutting
Mild steel – oxygen assisted
Laser cutting of mild steel with an oxygen assist gas is the most common, and perhaps the most complicated laser
processing application. Both the laser beam and the reaction between the oxygen and the iron in the steel provide the
required power to melt the material at the proper rate for the thickness being cut. As the material thickness increases,
the cutting speed needs to decrease at a rate that is not linear with the material thickness. For example, 10 mm material
will in general be cut at a speed that is less than half the speed for 5 mm material. The assist gas serves to blow the
liquid material out of the cut zone, so if the oxygen pressure is too low the material will not be removed quickly enough.
But since the reaction rate also depends on the oxygen pressure, too much oxygen can cause excessive burning and
flood the kerf with more liquid than can be removed. It is this balance of assist gas pressure and cut speed that need to
be maintained for proper cutting.
The laser beam’s focal position also has a large affect on the cutting process. If the focus is too close to the surface,
the kerf becomes too narrow and the assist gas cannot flow properly through the kerf to remove the liquid. If the focus
is too far above the surface, the kerf becomes too wide and there is not enough power to sustain the desired cut speed.
If the focus is too low in the material, the laser beam focus can vaporize the liquid which alters the gas and liquid flow,
disrupting the proper balance between the assist gas pressure and the cut speed.
Other factors can also affect the cutting process. The composition of the steel, surface condition, plate temperature,
oxygen purity, and laser power distribution can all impact the cut quality and speed for a given thickness. The relative
importance of these factors increases with plate thickness. Once conditions have been established for proper cutting,
controlling the repeatability of these factors as much as possible will help ensure a consistent process.
Piercing thicker mild steel is a key element to reducing cycle times and enabling proper cut initiation. There are several
methods for piercing mild steel. The simplest method is to place the nozzle at pierce height, turn on the assist gas, and
then turn on the laser at full power to pierce the material. This method creates a pierce hole in the material that is about
twice the nozzle diameter and leaves some material around the top edge of the pierce hole. The surrounding material will
be quite hot after the pierce, so you either need a lead-in that is about 1.0 – 1.5 times the material thickness or a delay
of a few seconds before starting the cut.
A second method is to pulse the laser and drill through the material. This method creates a pierce hole about the same
size as the laser beam and does not heat up the surrounding material as much as the previous method. However, the
pierce time will be about 1 second for each mm of material thickness, so it can take quite a while in thicker material. This
method is generally preferred when you need to cut a feature with dimensions that are about the same as the material
thickness, such as a 10 mm diameter hole in 10 mm thick mild steel.
The third method is to use a side jet to help control the piercing process. With this method the side jet blows away the
molten material as it exits the pierce hole and also controls the oxygen concentration interacting with the liquid steel.
This method is faster than the pulse piercing method and forms a smaller hole than the blast method, so less heat is
transferred to the surrounding material. This process is dependent on the side jet direction and pressure, so proper and
stable aiming of the jet is required.
The cut charts in the CNC provide a general guideline for the starting point of a particular thickness.
CAUtION
Highly reflective material can cause the beam to be reflected back through the beam delivery system
when the focus is near the surface of the workpiece, causing a significant increase in laser power that
can cause catastrophic failure of components.