Appendix b: trigger sensors (crank sensors), Rotor phasing, Trigger interface – Haltech E8 User Manual
Page 154: The input trigger
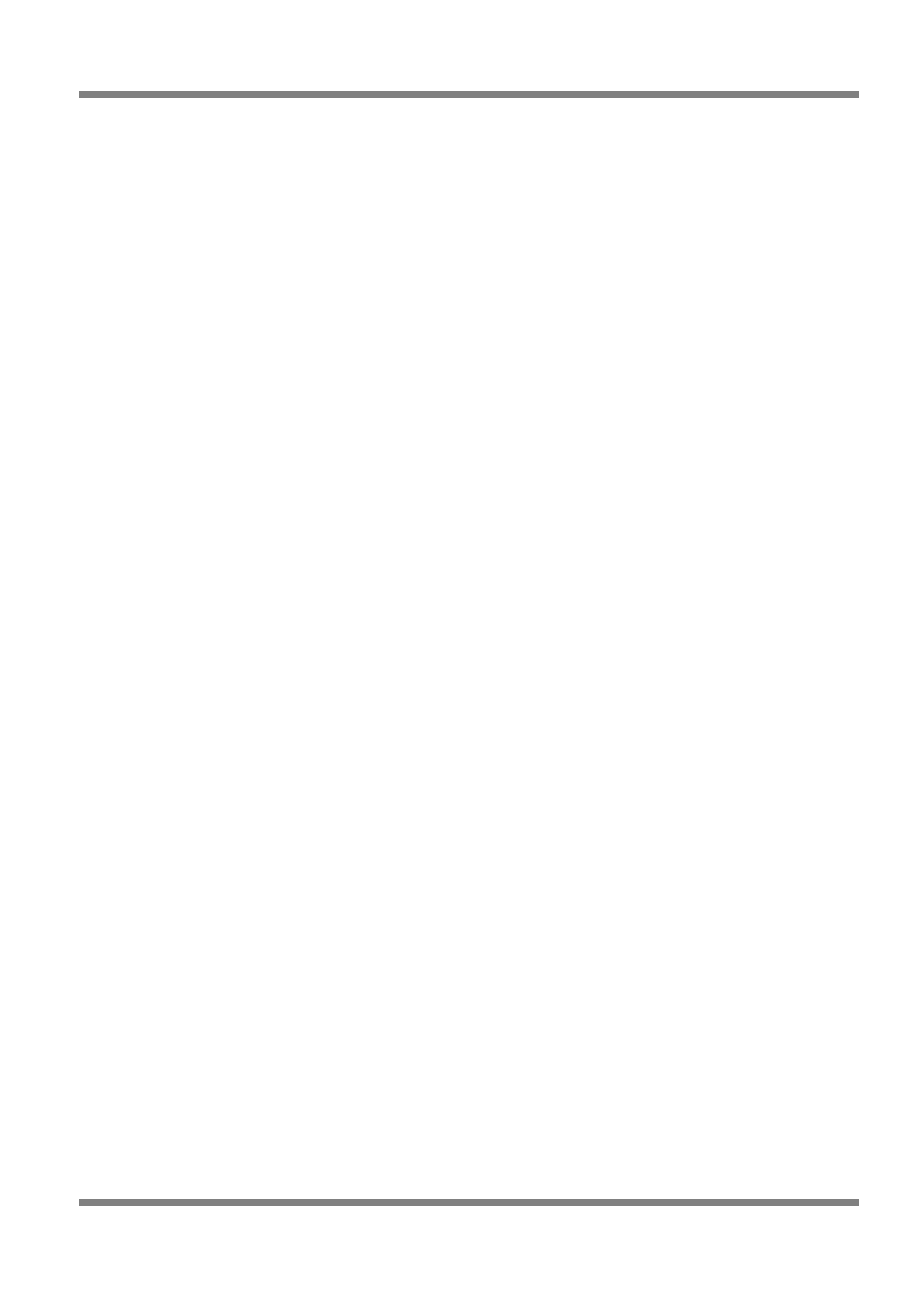
Haltech E11/E8 Instruction Manual
Make sure that you set the ignition output trigger edge correctly. If set to the wrong edge, the timing will be
out by significant amount and engine damage may result.
Appendix B: Trigger Sensors (Crank Sensors)
Rotor Phasing
One of the most important aspects to consider when modifying a distributor or trigger is the Rotor Phasing.
As an example, consider a distributor that uses a Hall effect sensor with a chopper wheel attached to the
distributor shaft. The Hall effect sensor is mounted to a plate that is rotated by a vacuum advance
mechanism and by centrifugal bob weights. This is a fairly conventional set up used in many vehicles with
electronic ignition. Simply removing the advance mechanisms and locking the plate so that it can’t move
may not be all that is required. The trigger edges generated by this modified distributor may fall outside
the trigger angle window allowed by the ECU. Something will have to be moved to allow the trigger edges
to fall within the required window.
If the distributor shaft is rotated so that the chopper wheel now triggers the sensor at 70° BTDC then a
problem of rotor phasing may have been induced. By the time the ignition pulse occurs, which could be up
to 60° later, the rotor button would have passed the plug lead terminal in the rotor cap and this could lead
to arcing in the distributor cap. The arcing could even be to the wrong plug lead terminal. If arcing doesn’t
occur, then the back EMF in the ignition coil primary could damage the ignition module or the ignition
system. Either way, the engine is not going to run correctly, if at all.
If the trigger sensor and rotor button phasing does not allow for usable ignition angles, the correct way to
fix the problem is to move the plate that the sensor is mounted on. Remember that all degrees referred to
here are crankshaft degrees, distributor degrees would be half those numbers referred to. Our example is
an engine that has the following timing requirements:
Minimum Timing
10° BTDC
Maximum Timing
40° BTDC
This gives a mid point, half way between the minimum and maximum timing, of 25°. Align the centre of the
rotor button with one of the plug lead terminals. It does not matter which one. This is where the rotor
button has to be when the engine is 25° BTDC. Now rotate the distributor shaft so that the rotor button is
where it should be when the engine is at 70° BTDC. i.e. move it back 45° crank degrees. This is where the
rotor button has to be when the chopper wheel triggers the sensor. Let’s assume that the trigger point of
the sensor is exactly in its centre. Move the plate the sensor is mounted on so that one of the vanes of the
chopper wheel is leaving the sensor. Adjust the position of the plate so that when the shaft rotates in its
normal direction, the centre of the sensor will become exposed. If it is not possible to move the sensor, it
will be necessary to rotate the trigger wheel relative to the shaft and the sensor.
Rotor phasing is not only a problem on distributors with advance mechanisms. Several factory distributors
have their triggers at points outside 60 - 100°. It is not advisable to just rotate the distributor until the
trigger is within this window. Care must be taken to ensure that the rotor phasing will not cause a problem.
Trigger Interface
Interfacing the ECU with your particular trigger system may be fairly straightforward or it may be
complicated. The variety of trigger designs available is the primary source of complication. This appendix
contains a lot of useful information about the different approaches to trigger design and is essential
information to anyone installing an ECU.
The Input Trigger
The ECU has been designed to trigger from either a square wave signal that varies from a ‘low’ of zero
volts (ground) to a voltage between 5 and 15 volts or from a magnetic inductive (reluctor) signal in
Page: 154
Copyright © Haltech 2008