Haltech E8 User Manual
Page 106
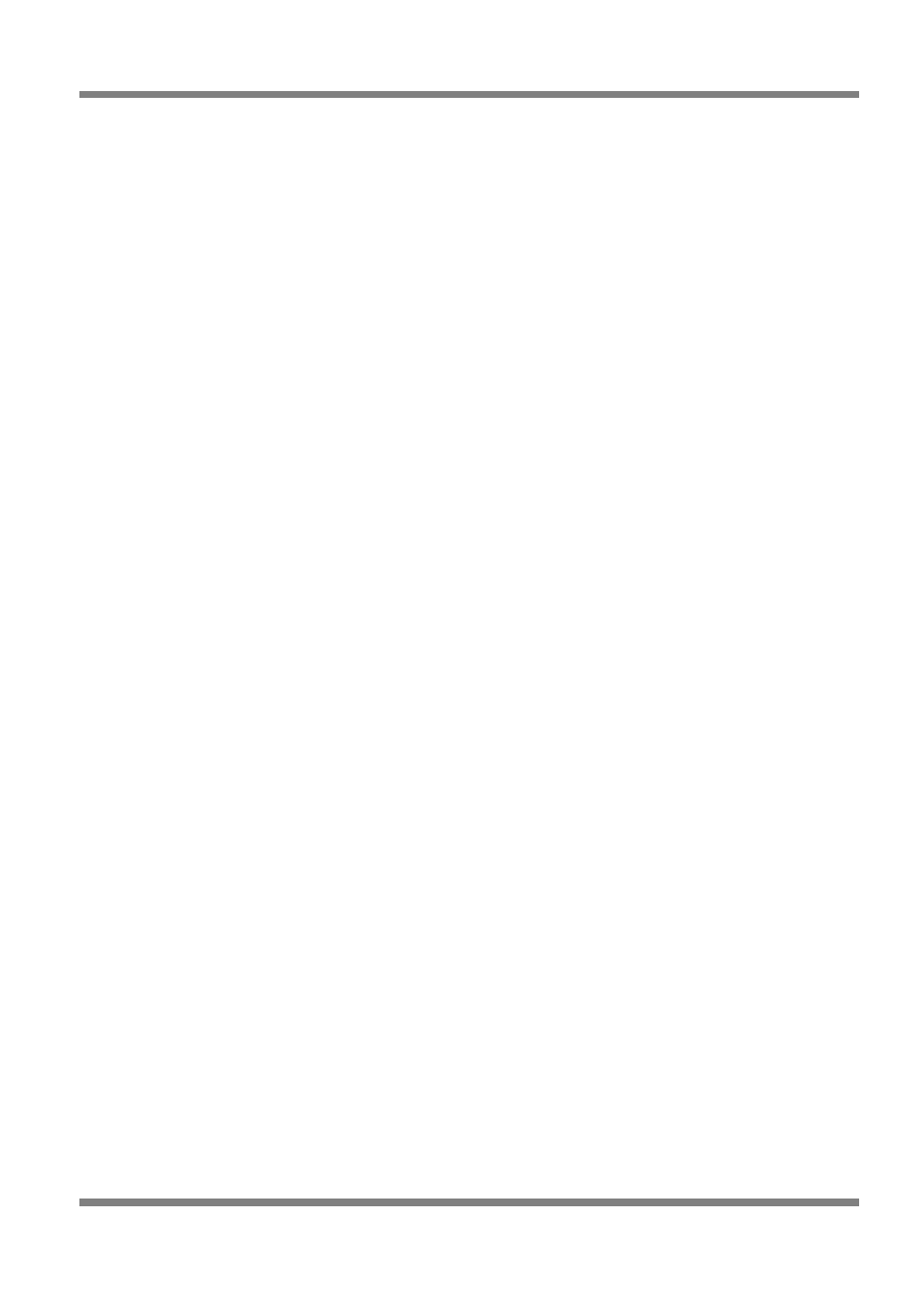
Haltech E11/E8 Instruction Manual
Setup of Stepper Motor Idle Control
The following steps will guide you through a method to setup and tune your idle control.
1.
Ensure that your Fuel and Ignition maps are well tuned and warm your engine up
to above the warm temp in the ‘Temperature Range’.
2.
Make sure that your throttle is properly calibrated so that throttle position in the
engine data reads zero percent when you are completely off throttle.
3.
Tick the ‘Enable Stepper Idle Control’ checkbox and enter in values for the stepper
motor. Check all the settings of the idle controller, the above values are a good
place to start.
4.
If the stepper motor range is unknown then tick the ‘Enable Manual Stepper Motor
Control’ checkbox and hit the ‘Apply’ button. Start from about half way along the
manual idle controller and increase the stepper motor position by 10 steps until
there is no more change in RPM. Copy this value into the ‘Stepper Motor Range’. If
the end is reached of the manual controller, increase the ‘Stepper Motor Range’
value and continue increasing the stepper position.
5.
Un-tick the ‘Enable Manual Stepper Motor Control’ checkbox and restart the
engine. The engine should idle around the ‘Warm Target RPM’, adjust this value to
change at what RPM the engine will idle when warm.
6.
Adjust the ‘Warm Start Position’ so it is about 10 – 15 steps above where the
stepper motor is sitting when the idle is controlled. The stepper position is shown in
the ‘Manual Idle Stepper Motor Control’ box.
7.
Adjust the ‘Warm Min Position’ so it is about 10 steps below where the stepper
motor is sitting when the idle is controlled.
8.
Steps 5 – 7 will need to be repeated for when the engine is cold.
Tuning Advance Sensitivity
Starting Point for PID values
•
Proportional Co-efficient
25%
•
Integral Co-efficient
10%
•
Derivative Co-efficient 0%
Tuning the PID Values
1. Set all Proportional, Integral and Derivative to zero
2. Bring up the Proportional in increments of 5% until you see a small oscillation in the RPM. Note:
the RPM will not reach the target RPM with only the Proportional part of the controller being used.
3. Bring up the Integral in increments of 5% until you cancel out the oscillation in the RPM. When the
Integral part is introduced the RPM will go to the target.
4. The Derivative term should remain at zero.
Notes
•
If the idle speed fluctuates or oscillates, reduce the idle sensitivity parameters slowly until the
oscillation stops. If the idle speed is slow to reach the target, increase the idle sensitivity
parameters slowly until it begins to oscillate and then reduce the values slightly.
Page: 106
Copyright © Haltech 2008