Rockwell Automation 2097-Vxxx Kinetix 350 Single-axis EtherNet/IP Servo Drive User Manual User Manual
Page 115
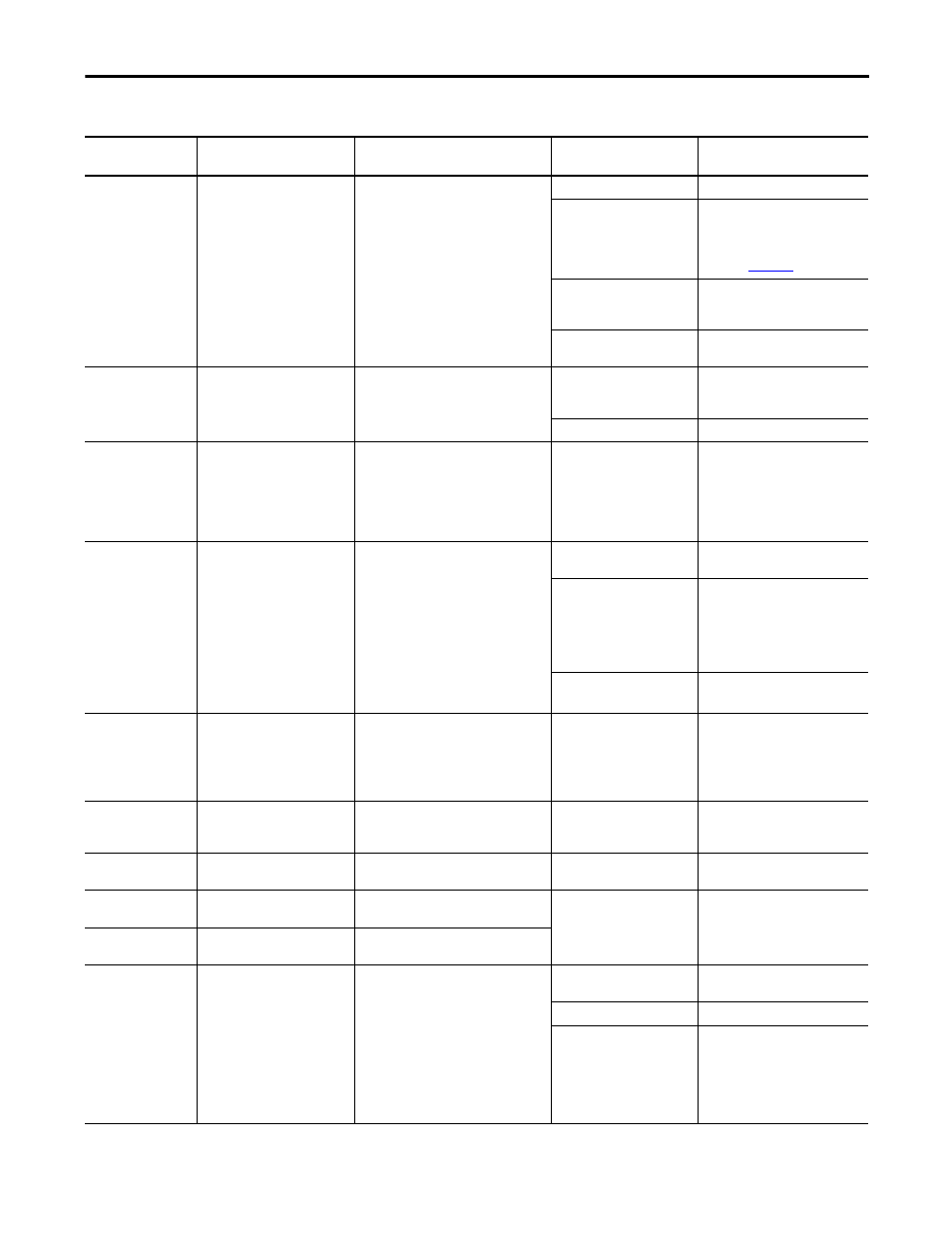
Rockwell Automation Publication 2097-UM002C-EN-P - December 2013
115
Troubleshoot the Kinetix 350 Drive Chapter 7
F 11
Inverter Overtemperature
Inverter thermal switch tripped.
Drive fan failed.
Replace the failed drive.
The cabinet ambient temperature
is above rating.
Check the cabinet temperature. See
Kinetix 350 Drive Power Specifications in
Kinetix Servo Drives Specifications
Technical Data,
publicat
The machine duty cycle requires an
RMS current exceeding the
continuous rating of the controller.
Change the command profile to reduce
speed or increase time.
The airflow access to the drive
system is limited or blocked.
Check airflow and re-route cables away
from the drive system.
F 13
Inverter Thermal Protection
The thermal model for the power transistors
indicates that the temperature has exceeded
110% of its rating.
The machine duty cycle requires an
RMS current exceeding the
continuous rating of the controller.
Change the command profile to reduce
speed or increase time.
Motor brake on.
Turn motor brake off.
F 33
Bus Undervoltage
With three-phase power present, the DC bus
voltage is below limits.
DC bus voltage for 460V system is
below 275V.
DC bus voltage for 230V system is
below 137V.
DC bus voltage for 120V system is
below 80V
•
Verify voltage level of the incoming
AC power.
•
Check AC power source for glitches or
line drop.
•
Install an uninterruptible power
supply (UPS) on your AC input.
F 35
Bus Overvoltage
The DC bus voltage is measured above a factory
limit.
Excessive regeneration of power.
Change the deceleration or motion
profile.
When the motor is driven by an
external mechanical power source,
it can regenerate too much peak
energy through the drive power
supply. The system faults to save
itself from an overload.
Use a larger system (motor and drive).
DC bus voltage for 460V
system is over 820V.
Install shunt resistor.
F 43
Feedback Loss
•
On sin/cos encoders, the sum of the square
of the sin/cos signals has been measured
below a factory limit.
•
On TTL encoders, the absolute value of the
differential A/B signals is below a factory
limit.
The motor feedback wiring is open,
shorted, or missing.
•
Check motor encoder wiring.
•
Run Hookup test in RSLogix 5000
software.
F 45
Feedback Serial Comms
(only TL-Series motors and
actuators )
The number of consecutive missed or corrupted
serial data packets from the feedback device has
exceeded a factory set limit.
Communication was not
established with an intelligent
encoder.
•
Verify motor selection.
•
Verify motor encoder wiring.
F 47
Feedback Self Test
The feedback device has detected an internal
error.
Damage to feedback device.
Call your Rockwell Automation sales
representative to return motor for repair.
F 50
Hardware Overtravel - Positive
Axis moved beyond the physical travel limits in
the positive direction.
Dedicated overtravel input is
inactive.
•
Check wiring.
•
Verify motion profile.
•
Verify axis configuration in software.
F 51
Hardware Overtravel - Negative
Axis moved beyond the physical travel limits in
the negative direction.
F 54
Excessive Position Error
Position error limit was exceeded.
Partial loss of feedback signals.
Check all wiring at motor feedback (MF)
connector.
Improperly sized drive or motor.
Verify sizing of system.
Mechanical system out of
specifications.
•
Increase the feed forward gain.
•
Increase following error limit or time.
•
Check position loop tuning.
•
Verify mechanical integrity of system
within specification limits.
•
Check motor power wiring.
Table 44 - F xx Fault Codes (continued)
Four-digit Display
RSLogix 5000
Fault Message
Problem or Symptom
Potential Cause
Possible Resolution