Safe torque-off wiring requirements – Rockwell Automation 2097-Vxxx Kinetix 350 Single-axis EtherNet/IP Servo Drive User Manual User Manual
Page 106
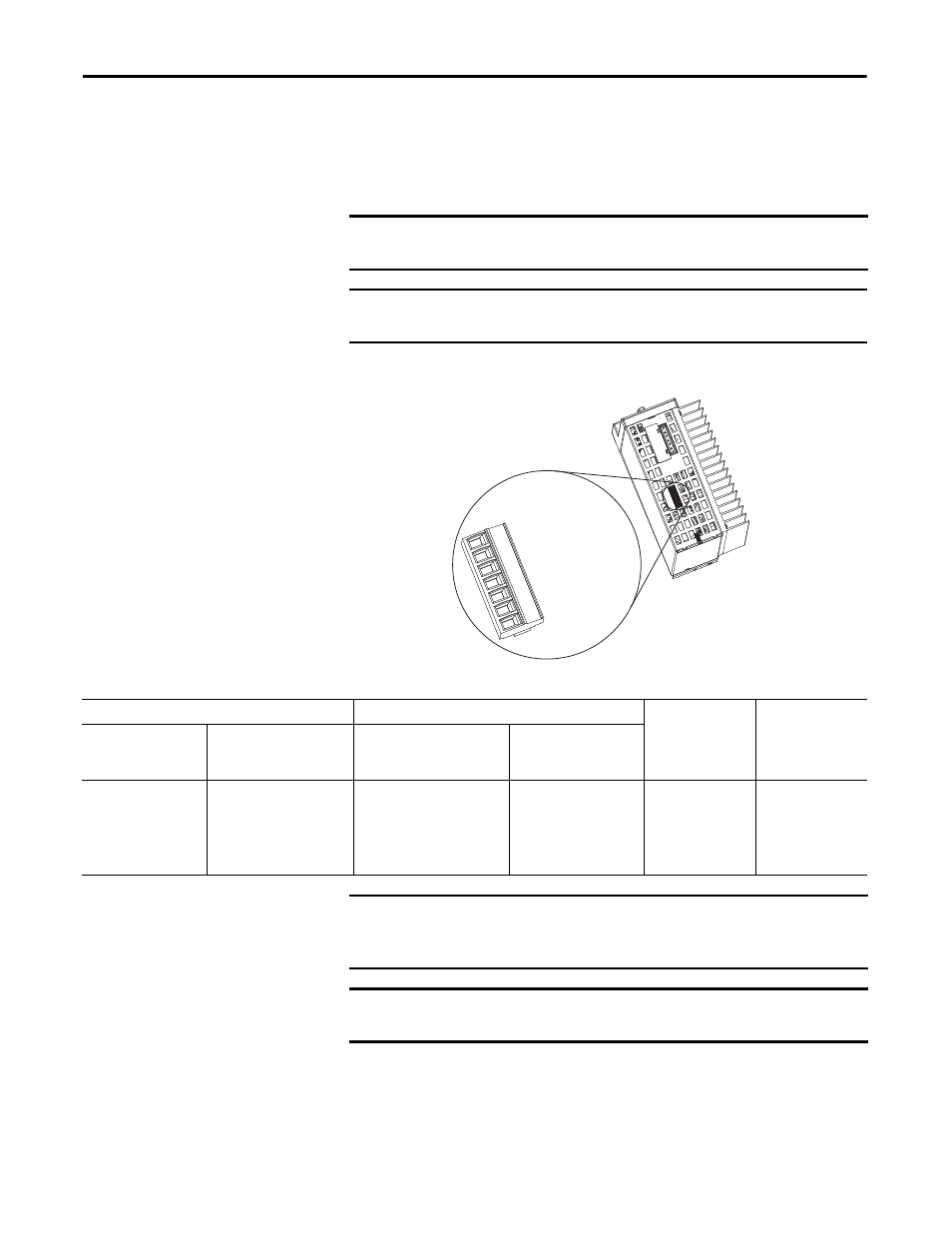
106
Rockwell Automation Publication 2097-UM002C-EN-P - December 2013
Chapter 6 Kinetix 350 Drive Safe Torque-off Feature
Safe Torque-off Wiring Requirements
These are the safe torque-off (STO) wiring requirements. Wire must be copper
with 75 °C (167 °F) minimum rating.
Figure 47 - Safe Torque-off (STO) Terminal Plug
IMPORTANT
The National Electrical Code and local electrical codes take precedence over the
values and methods provided.
IMPORTANT
Stranded wires must terminate with ferrules to prevent short circuits, per table
D7 of EN 13849.
1 2 3 4 5 6
+24 V DC c
ontrol
Contr
ol COM
Safety
status
Safety
input 1
Safety
COM
Safety
input 2
Table 40 - Safe Torque-off (STO) Terminal Plug Wiring
Safe Torque-off (STO) Connector
Recommended Wire Size
Strip Length
mm (in.)
Torque Value
N•m (lb•in)
Pin
Signal
Stranded Wire
with Ferrule
mm
2
(AWG)
Solid Wire
mm
2
(AWG)
STO-1
STO-2
STO-3
STO-4
STO-5
STO-6
+24V DC Control
Control COM
Safety Status
Safety Input 1
Safety COM
Safety Input 2
0.75 (18)
1.5 (16)
6 (0.25)
0.2 (1.8)
IMPORTANT
Use only pins STO-1 (+24V DC Control) and STO-2 (Control COM) of the motion-
allowed jumpers to defeat the safe torque-off function. When the safe torque-
off function is in operation, the 24V supply must come from an external source.
IMPORTANT
To be sure of system performance, run wires and cables in the wireways as
established in the user manual for your drive.