6 printer adjustments, 1 printing on alternate card stocks, 2 conducting the tape adhesion test – HID HDPii Plus User Guide 2.0 User Manual
Page 80: Printer adjustments, Printing on alternate card stocks, 6printer adjustments
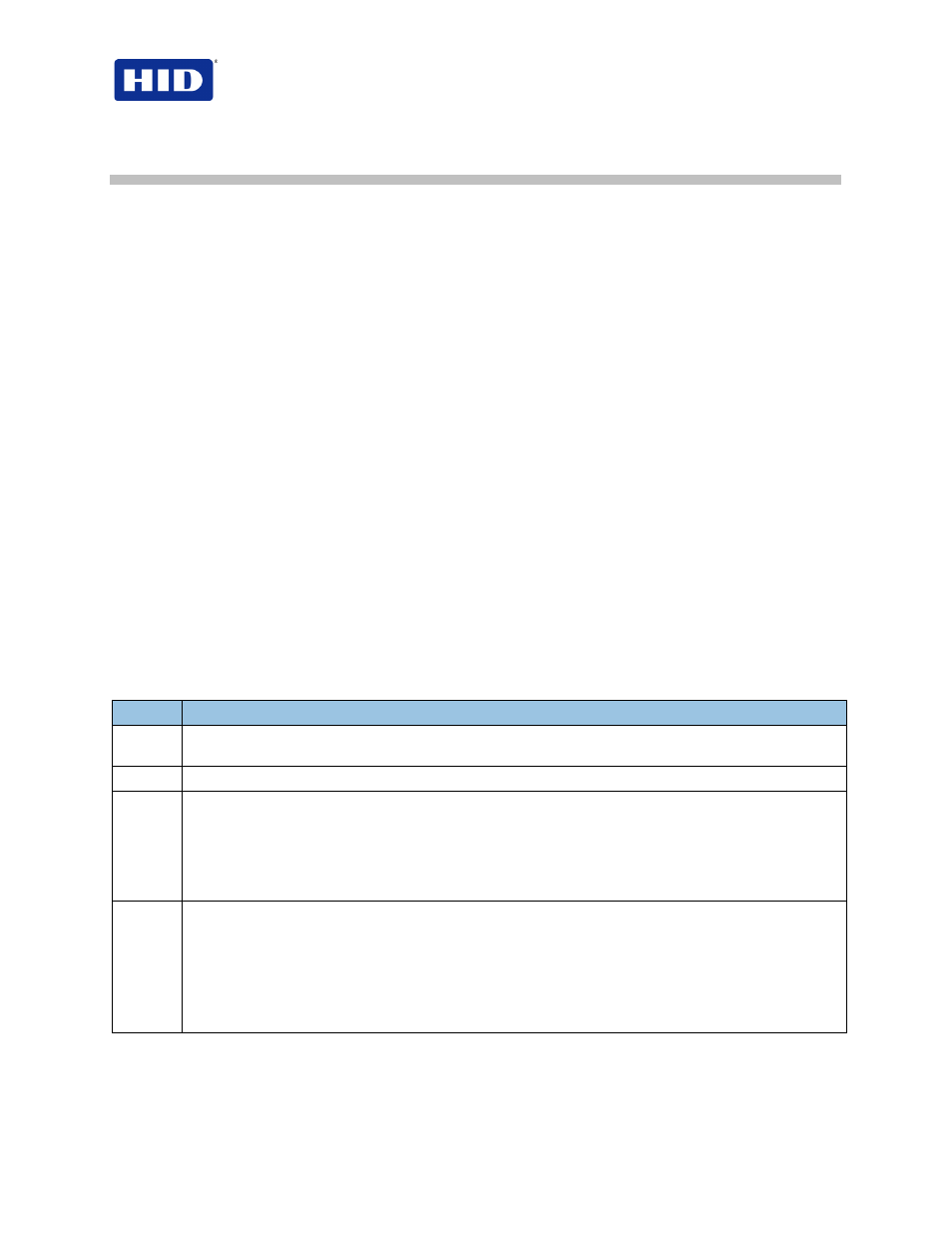
HDP5000 & HDPii Card Printer Encoder User Guide_L000950, 2.0
Page 80 of 103
December 2012
© 2012 HID Global Corporation. All rights reserved
6
Printer Adjustments
The purpose of this section is to provide the User with specific information on Printer adjustment
procedures.
6.1
Printing on Alternate Card Stocks
6.1.1 Selecting the Right Cards and optimizing the HDP Print Process
In order to optimize the Card Printer’s capabilities for cards with hard-to-print surfaces, we
recommend evaluating the card stock selection before installation of the Printer.
The variability in cards based on:
•
Different surface textures and different sources of raw materials: This may require
different InTM Film transfer parameters.
•
Varied methods of assembling IC smart cards and proximity cards: These particular
adhesives used to glue a smart chip to a plastic card may react differently to a Transfer
Roller’s pressure and temperature.
•
Cleanliness of card stock: The HDP process does not eliminate the need to use clean
card stock. The best-looking card always starts with the cleanest card surface. Dirt and
debris on a card can show up as blemishes on the card surface and may reduce the life of
the image itself.
6.1.2 Conducting the Tape Adhesion Test
It is important to conduct tape adhesion tests because one cannot be certain which transfer
temperature and Dwell Time will work best (when printing cards other than UltraCard III).
(
Note: The optimal transfer settings may vary from card type to card type.)
IMPORTANT: Inadequate time and temperature could produce cards that are more vulnerable
to accelerated wear and dye migration. Use sufficient time and temperature to transfer InTM Film
to the card to ensure a long lasting, durable card.
Step
Procedure
1
Test the adhesion quality of the InTM Film to the card by printing sample cards and completing an
adhesive tape test.
2
Select the UltraCard IIIs-Glossy PVC if the card is glossy and print a test card.
3
a. Apply a strip of ½ (12mm) wide Scotch-type clear adhesive tape (such as 3M brand 600), at
least 2 (50mm) long, firmly across the surface of the card, pressing out all air bubbles with a
fingertip.
b. Remove the tape by smoothly and rapidly (approximately 2 inches/second (50mm/sec)) pulling
it up at a perpendicular (90 degree) angle to the card. (
Note: The IPC recommends a minimum
of three tests for each card type evaluation.)
4
Visually examine the card and the strip of tape pulled from the card, to see if any portion of the InTM
Film was removed from the card.
•
If any residue (for example, oil or grease from fingertips) is present on the card surface, the
evaluation results may be affected.
•
If the printed, transferred InTM Film particles (a) pull away from the card and (b) adhere to the
tape, this indicates that inadequate adhesion of the InTM Film to the card. Increased heat and
Dwell Times are necessary to resolve this problem.