Outputs, Linearization, Duplex – Watlow EZ-ZONE RMH User Manual
Page 106: Cool output curve, Retransmitting a process value or set point
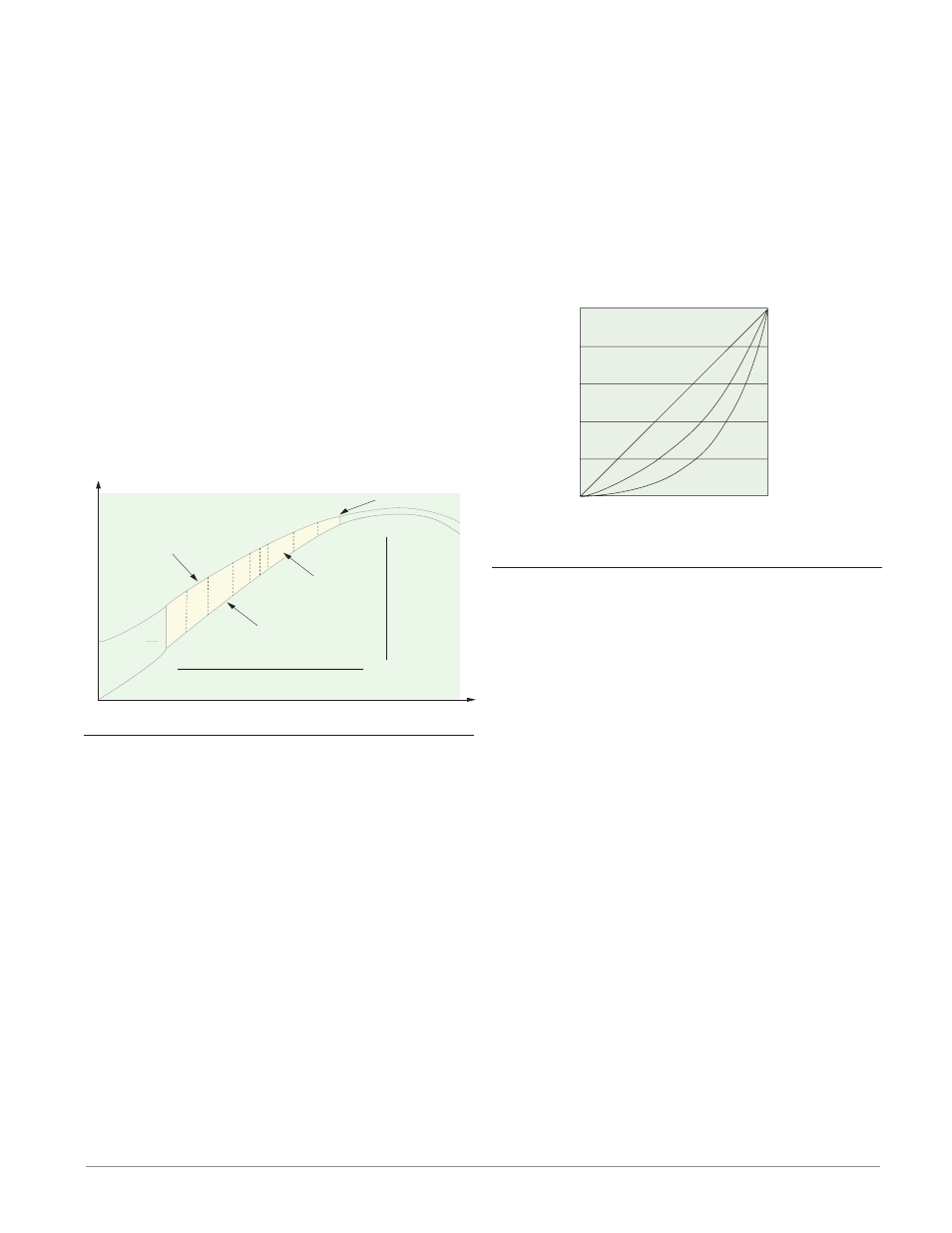
Watlow EZ-ZONE
®
RMH Module
•
103
•
Chapter 6 Features
Select the low and high values with Range Low
[`r;Lo]
and Range High [`r;hi] (Setup Page, Analog
Input Menu).
Linearization
The linearization function allows a user to re-linear-
ize a value read from an analog input. There are 10
data points used to compensate for differences be-
tween the sensor value read (input point) and the de-
sired value (output point). Multiple data points enable
compensation for non-linear differences between the
sensor readings and target process values over the
thermal or process system operating range. Sensor
reading differences can be caused by sensor place-
ment, tolerances, an inaccurate sensor or lead resis-
tance.
The user specifies the unit of measurement and
then each data point by entering an input point value
and a corresponding output point value. Each data
point must be incrementally higher than the previous
point. The linerization function will interpolate data
points linearly in between specified data points.
2
3
4
5 6
7
8
9
Reading from Sensor
without Linearization
(Actual Value)
Input Point 1
Output Point 1
Input Point 10
Output Point 10
Offset Zone
Reading from Sensor
with Linearization
(Displayed Value)
No Offset
T
emperature
Time
Outputs
Duplex
Certain systems require that a single process output
control both heating and cooling outputs. An EZ-
ZONE
®
RMH controller with a process output can
function as two separate outputs.
With a 4 to 20mA output the heating output will
operate from 12 to 20mA (0 to +100 percent) and the
cooling output will operate from 12 to 4mA (0 to -100
percent).
In some cases this type of output is required by
the device that the EZ-ZONE RMH controls, such
as a three-way valve that opens one way with a 12
to 20mA signal and opens the other way with a 4 to
12mA signal. This feature reduces the overall system
cost by using a single output to act as two outputs.
Outputs 1 and 3 can be ordered as process out-
puts. Select duplex [dUPL] as the Output Function
[``Fn]
(Setup Page, Output Menu). Set the output to
volts [uoLt] or milliamps [`MA] with Output Type
[`o;ty]
. Set the range of the process output with
Scale Low [`S;Lo] and Scale High [`S;hi].
Cool Output Curve
A nonlinear output curve may improve performance
when the response of the output device is nonlinear.
If a cool output uses one of the nonlinear curves a
PID calculation yields a lower actual output level
than a linear output would provide.
These output curves are used in plastics extruder
applications: curve 1 for oil-cooled extruders and
curve 2 for water-cooled extruders.
A
ctual Output
Po
wer
0
20
40
60
80
100
PID Calculation
Linear
Curve 1
Curve 2
Select a nonlinear cool output curve with Cool Out-
put Curve [`C;Cr] (Setup Menu, Loop Menu).
Retransmitting a Process Value or Set Point
The retransmit feature allows a process output to
provide an analog signal that represents the set point
or process value. The signal may serve as a remote
set point for another controller or as an input for a
chart recorder documenting system performance over
time.
In choosing the type of retransmit signal the op-
erator must take into account the input impedance
of the device to be retransmitted to and the required
signal type, either voltage or milliamperes.
Typically, applications might use the retransmit
option to record one of the variables with a chart re-
corder or to generate a set point for other controls in
a multi-zone application.
Outputs 1 to 3 and 7 to 9 can be ordered as pro-
cess outputs. Assign an analog source to Output
Function to accomplish retransmit of a process or set
point value.
Note:
The active set point is not retransmitted, only the
user requested closed loop set point which may not
be the closed loop set point in control. Retransmit-
ting a profiling closed loop set point is not allowed.