D ] system configuration example – Yaskawa MP2300S Basic Module User Manual
Page 58
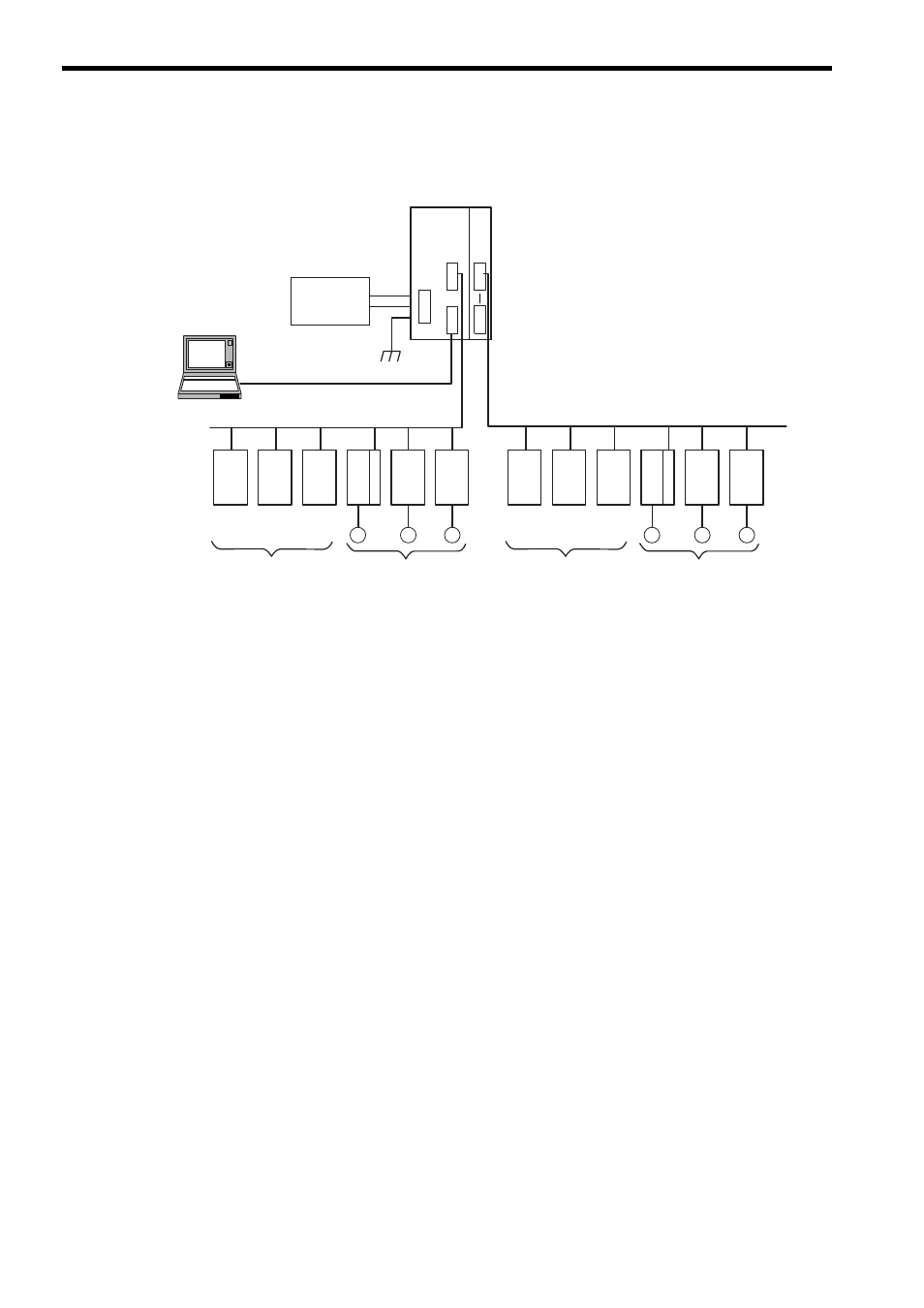
2.2 Basic Module
2.2.5 Built-in SVB Module
2-32
[ d ] System Configuration Example
The following diagram shows a system configuration example.
Use the specified cables and connectors. Refer to 1.1.5 (3) Cables in the Machine Controller MP2000-series SVB/
SVB-01 Motion Module User’s Manual (manual number: SIEP C880700 33) to select appropriate cables and con-
nectors to connect each device.
The SERVOPACK models that can be connected through MECHATROLINK-I differ from those connected through
MECHATROLINK-II. Refer to 1.4.1 MECHATROLINK-I/II Compatible Devices to select appropriate SERVOPACK
models for the MECHATROLINK interface to be used.
If both MECHATROLINK-I (4 Mbps) compatible devices and MECHATROLINK-II (10 Mbps) compatible devices are
connected in a system, make the settings in accordance with MECHATROLINK-I specifications.
When connecting a SERVOPACK to an SVB Module via MECHATROLINK, connect signal lines such as those for
overtravel, zero-point return deceleration limit switch, and external latch to the SERVOPACK. Refer to the relevant
SERVOPACK manual for details on the connections.
When connecting
Σ-II series SERVOPACKs (SGDH+NS100 or SGDH+NS115), do not connect a hand-held type
digital operator and SigmaWin+. If connected, alarms A.95 (command warning) and A.ED (execution not completed)
will occur for the commands sent from the SVB Module, and normal operation will be interrupted. If a digital operator
or SigmaWin+ must be connected to a
Σ-II series SERVOPACK, disconnect the SERVOPACK from the SVB Mod-
ule.
24-VDC
power supply
MP2300S
MECHATROLINK-
II
SGDV
M
IO2310
PL2900
PL2910
NS1
15
SGDH
M
SGDS
M
MECHATROLINK support
input/output modules
Servo drive
MECHATROLINK-
II
SGDS
M
IO2310
PL2900
PL2910
NS1
15
SGDH
M
SGDV
M
MECHATROLINK support
input/output modules
Servo drive
Ethernet
SVB-01
MPE720