Tool tip radius compensation trc – HEIDENHAIN TNC 640 (34059x-02) User Manual
Page 472
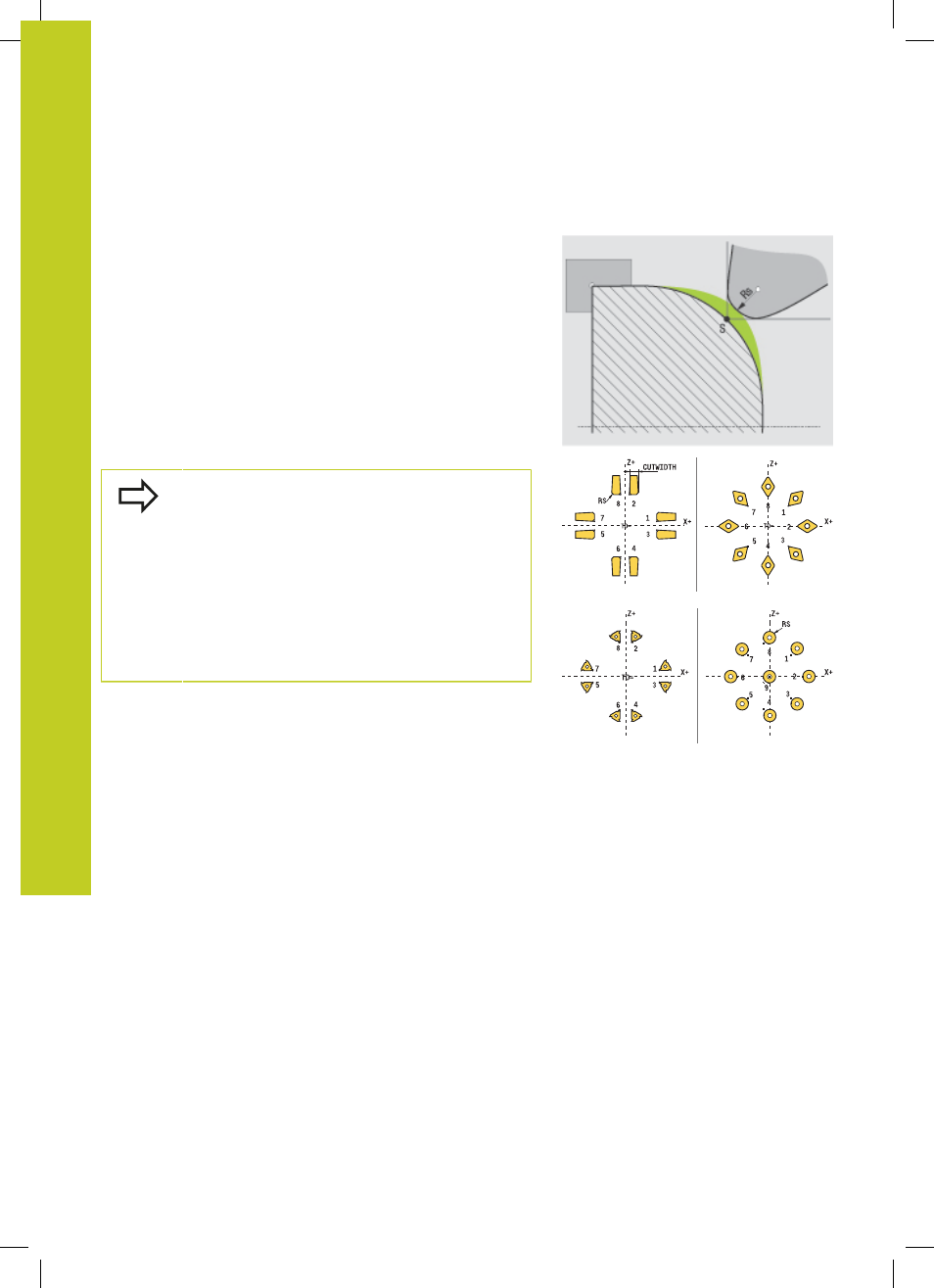
Programming: Turning Operations
14.2 Basis Functions (Software Option 50)
14
472
TNC 640 | User's Manual
HEIDENHAIN Conversational Programming | 5/2013
Tool tip radius compensation TRC
Turning tools have a radius at the tool tip (
RS). When machining
tapers, chamfers and radii, this results in inaccuracies on the
contour because programmed traverse paths are always referenced
to the theoretical tool tip S (see figure at upper right). TRC prevents
the resulting deviations.
In turning cycles the TNC automatically carries out tool tip radius
compensation. In specific traversing blocks and within programmed
contours, activate TRC with
RL or RR.
In turning cycles the TNC checks the cutting geometry with the
point angle
P-ANGLE and the setting angle T-ANGLE. Contour
elements in the cycle are processed by the TNC only as far as this
is possible with the specific tool. The TNC outputs a warning when
residual material is left behind.
When the position of the cutting edge is
neutral (
TO=2;4;6;8), the direction of the radius
compensation is ambiguous. In this case, TRC is only
possible within cycles.
The TNC can also run tool tip radius compensation
during inclined processing. The following limitation
applies here: if you activate inclined processing with
M128 then tool tip radius compensation without
a cycle, i.e. in traversing blocks with
RL/RR, is not
possible. If you activate inclined processing with
M144 this limitation does not apply.