Permitted tool shapes, Using other tools: delta values, D compensation without tcpm – HEIDENHAIN TNC 640 (34059x-02) User Manual
Page 449
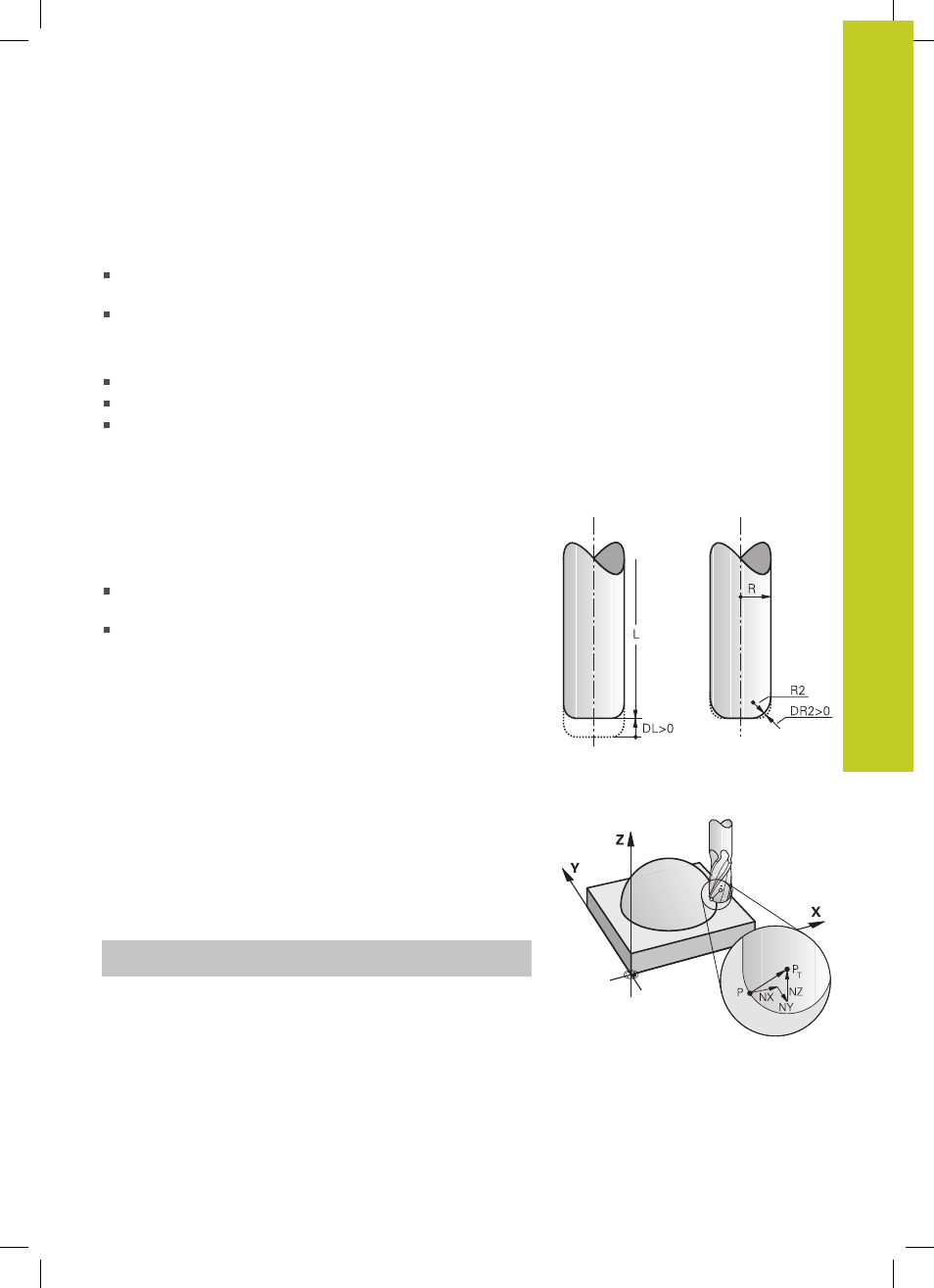
Three-dimensional tool compensation (software option 2) 12.6
12
TNC 640 | User's Manual
HEIDENHAIN Conversational Programming | 5/2013
449
Permitted tool shapes
You can describe the permissible tool shapes in the tool table via
tool radii
R and R2 (see figure):
Tool radius
R: Distance from the tool center to the tool
circumference
Tool radius 2
R2: Radius of the curvature between tool tip and
tool circumference
The ratio of
R to R2 determines the shape of the tool:
R2 = 0: End mill
R2 = R : Radius cutter
0 <
R2 < R: Toroid cutter
These data also provide the coordinates of the tool datum PT.
Using other tools: Delta values
If you want to use tools that have different dimensions than the
ones you originally programmed, you can enter the difference
between the tool lengths and radii as delta values in the tool table
or
TOOL CALL:
Positive delta value
DL, DR, DR2: The tool is larger than the
original tool (oversize)
Negative delta value
DL, DR, DR2: The tool is smaller than the
original tool (undersize)
The TNC then compensates the tool position by the sum of the
delta values from the tool table and the tool call.
3-D compensation without TCPM
The TNC carries out a 3-D compensation for three-dimensional
machining operations if the NC program contains surface-normal
vectors. In this case, the
RL/RR radius compensation and TCPM or
M128 must be inactive. The TNC displaces the tool in the direction
of the surface-normal vectors by the sum of the delta values (tool
table and
TOOL CALL).
Example: Block format with surface-normal vectors
1 LN X+31.737 Y+21.954 Z+33.165NX+0.2637581 NY+0.0078922
NZ-0.8764339 F1000 M3
LN:
Straight line with 3-D compensation
X, Y, Z:
Compensated coordinates of the straight-line
end point
NX, NY, NZ:
Components of the surface-normal vector
F:
Feed rate
M:
Miscellaneous function