Rockwell Automation 8510 AC Spindle Drive System User Manual User Manual
Page 78
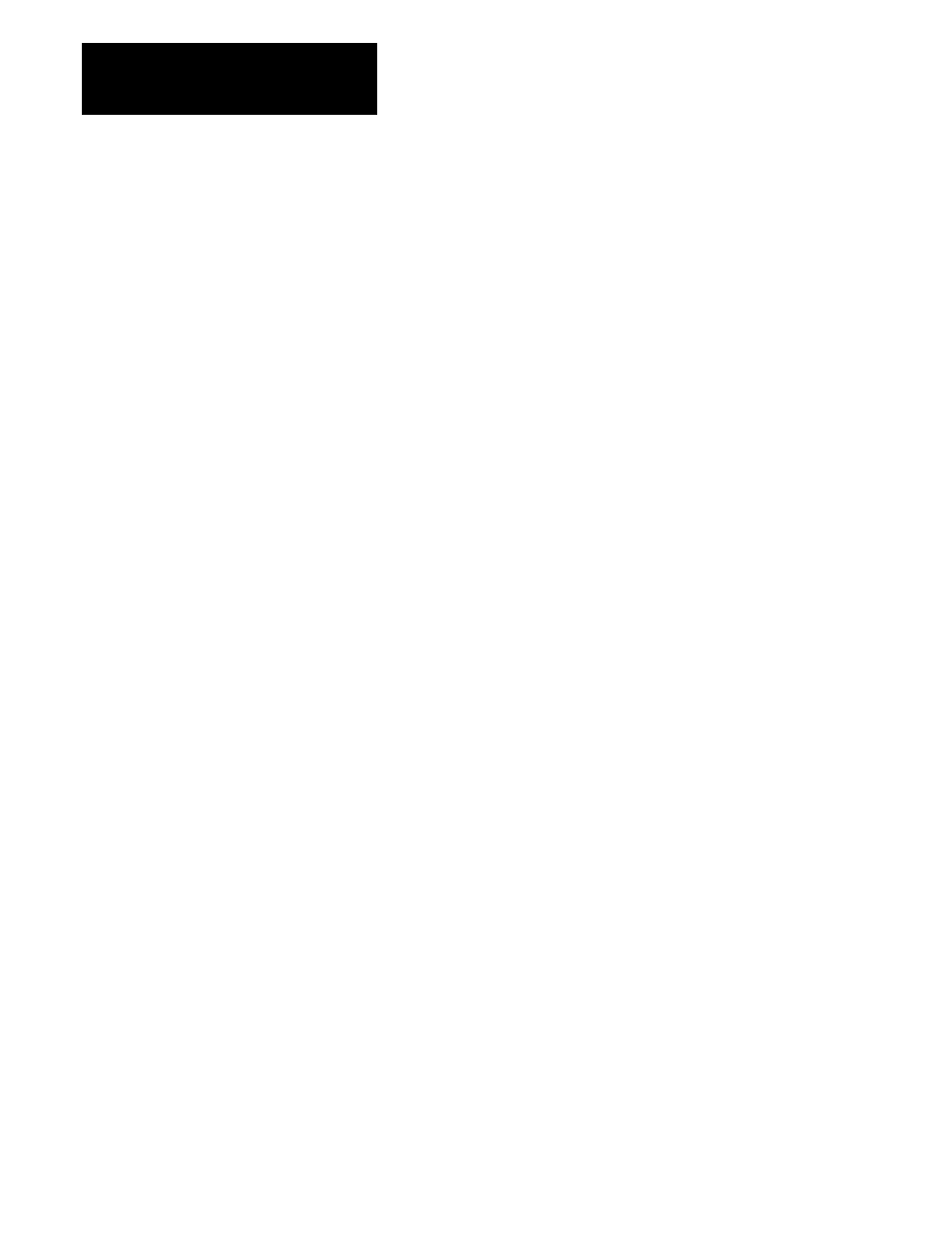
Wiring
Chapter 8
8-74
Wire Sizes
Unless noted, the wire sizes in this manual are recommended minimums
and assume type MTW wire (machine tool wire, 75
°
C, minimum) per
NFPA 79. In all cases, the user is responsible for selecting the appropriate
wire type to comply with all applicable national and local codes and to
satisfy the needs of the particular application and environmental
conditions. Since ambient conditions vary widely, on certain applications, a
derating factor has to be taken into account. Also, wiring to systems or
motors exceeding 15 meters (50 feet) in length (total includes to and from
device) may cause excessive voltage drops. Consult the National Electrical
Code or appropriate national or local code for factors on ambient
conditions, length etc.
Shielding
Reasonable care must be taken when connecting and routing power and
signal wiring on a machine or system. Radiated noise from nearby relays
(relay coils should have surge suppressors), transformers, other electronic
drives, etc. may be induced into the signal lines causing undesired
movement of the motor.
All signal wiring must use shielded cables. All power wiring must be
installed in a metal conduit or wireway. Power leads are defined here as the
transformer primary and secondary leads, motor leads and any 115V AC or
above control wiring for relays, fans, thermal protectors etc. Signal wiring
is defined as velocity command, feedback, enable lines and low level logic
signal lines.
Feedback, command signal and other shields must be insulated from each
other and terminated as specified in this chapter. This helps to minimize
radiated and induced noise problems and ground loops. Refer to the
paragraph entitled Grounding.
Open ended shields must be insulated so that they do not accidentally cause
ground loops.
All analog signals to and from the drive use twisted, shielded pairs. The
typical installation practice is to terminate the shield at the signal source
end. While this usually gives good results, there may be systems that
require other shield grounding schemes for best results. If noise is a
problem with the typical shield grounding methods, try terminating the
shields at the load end or at both ends and evaluate the results. There is no
single solution that is best for all situations.