Rockwell Automation 8510 AC Spindle Drive System User Manual User Manual
Page 104
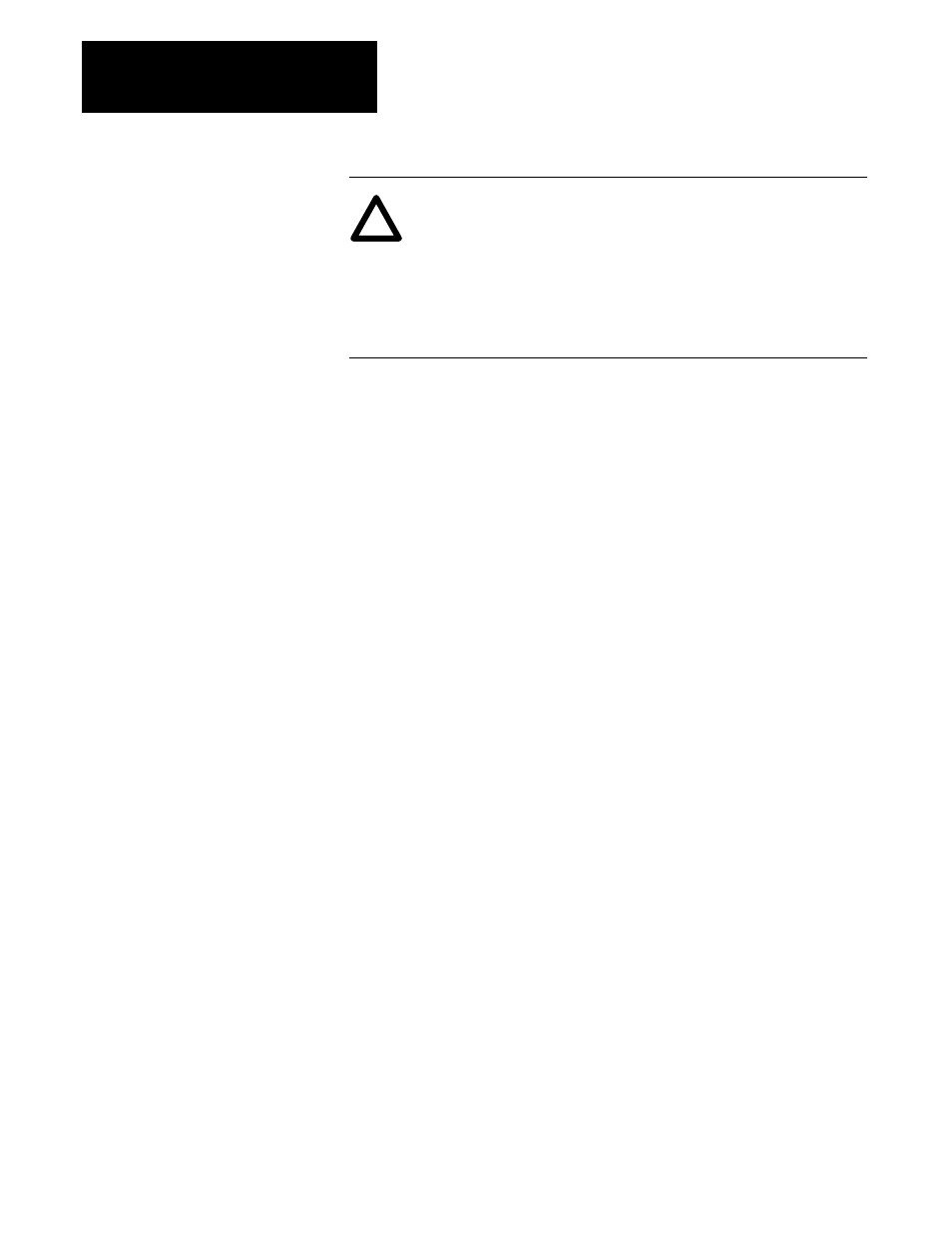
Start-Up
Chapter 9
9-100
ATTENTION: If an oscilloscope is used during start-up or
troubleshooting, it must be properly grounded. The oscilloscope
chassis may be at a potentially fatal voltage if not properly
grounded. Always connect the oscilloscope chassis to earth
ground.
When using an oscilloscope it is recommended that the test
probe ground be connected to the test point labeled “GND.”
!
a) Optimum tuning is obtained by observing the small signal step
response. The step should be small enough to assure that the drive
output does not become torque limited. In addition, the Acc Rate
parameter setting should be fast enough so that it does not limit
the acceleration rate. To simplify the tuning process, it is best to
separate the P Gain and I Gain tuning. First set Spindl I Gain
equal to zero. Observe test point TP1 during an accel/decel cycle
to a low speed. Increase Spindl P Gain until the desired response
rate is achieved but allow no more than one overshoot of the
commanded speed. Then increase the Spindl I Gain until the
desired level of low frequency and static stiffness is achieved.
Proper adjustment of the P Gain and I gain should provide a step
response with a relatively sharp corner and minimal overshoot of
commanded speed. If the system overshoots with a high
frequency ringing, the Spindl P Gain is too high. A low frequency
ringing indicates excess Spindl I Gain.
b) Observe the TP2 test point during an accel/decel cycle. As the
actual speed approaches commanded speed, the torque should
drop from maximum to a low running torque with only a small
overshoot. The overshoot should settle without ringing. Raise the
Spindl P Gain and lower the Spindl I Gain to reduce the ringing.
While running at maximum speed the peak to peak torque ripple
should be less than 2V DC. Lower both the Spindl P Gain and
Spindl I Gain to reduce the torque ripple.
o
15. If the 8510 must operate in servo mode, apply 24V DC to the
Spindle/Servo Mode Select input to activate servo mode. Servo
mode can be configured to operate over two different, input
selectable, maximum operating speed ranges. Apply 24V DC to the
Servo Input Scaling input to select the high operating speed range
and then repeat steps 12, 13, and 14.
In servo mode, it is usually desirable to set the Servo P Gain and
Servo I Gain as high as possible to achieve the most responsive
servo performance. When approaching the final speed, the torque
may overshoot with 1-2 “rings” but then should immediately settle
out.