Rockwell Automation 8510 AC Spindle Drive System User Manual User Manual
Page 133
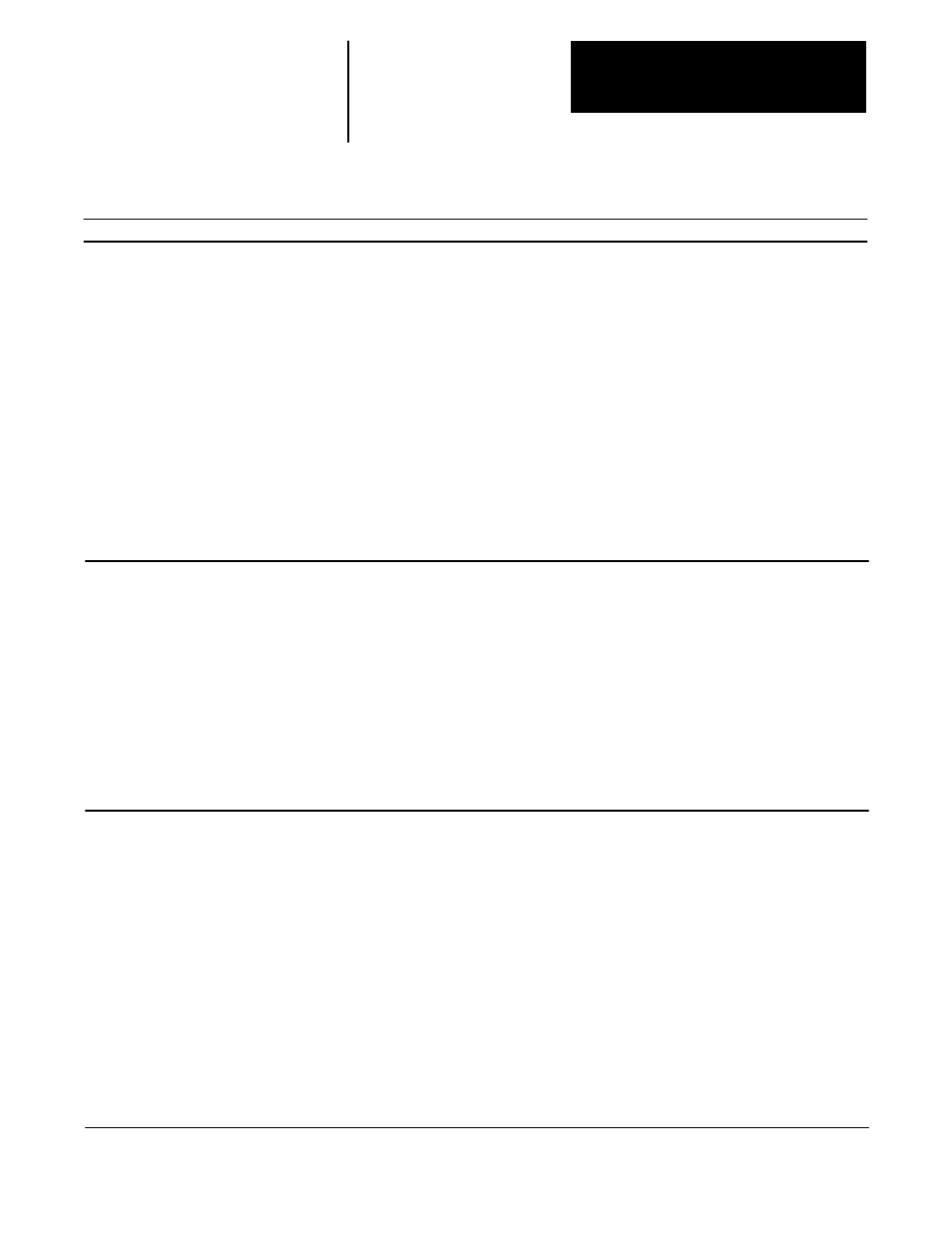
Troubleshooting
Chapter 11
11-129
Table 11.G
Problems that Occur during Spindle Orient Operation
Possible Solutions
Probable Cause
Problem
Motor runs contin-
uously at the
Orient Speed
parameter setting
without faulting
and without
orienting.
Use the ORIENT SETUP - FEEDBACK DEFN - Encdr Phasing
parameter to reverse the phasing of the orient feedback device.
Feedback device is incorrectly
phased.
The ORIENT SETUP - FEEDBACK DEFN - Encoder Type
parameter must be set to “OPTICAL PULSE” when an optical
encoder is used and to “MAGNET ANALOG” when the high
resolution magnetic feedback is used. Change this parameter to the
correct setting and store it in EEPROM by energizing the Drive
Enable input. After the correct setting is stored, AC power must be
removed from the drive and then reapplied to reset this parameter
value in the drive control software.
Wrong type of feedback device
has been specified.
Use the ORIENT SETUP - FEEDBACK DEFN - Encoder Lines
parameter to set the correct encoder line count or number of teeth
on the high resolution feedback gear.
The number of encoder lines has
been incorrectly programmed.
If problems were not found with other tests, replace Main Control
Board (CPU Board on A04/A06 drives).
Malfunctioning printed circuit
board.
Bad PG Marker
displayed- A
correct marker
pulse was not
detected within one
revolution of the
feedback device as
determined by the
programmed
number of lines on
the feedback
device.
Use the ORIENT SETUP - FEEDBACK DEFN - Encoder Lines
parameter to set the correct encoder line count or number of teeth
on the high resolution feedback gear.
The number of encoder lines has
been incorrectly programmed.
1. Verify that connector CN2 is connected to the drive.
2. Verify the wiring of the connector at the drive and at the
feedback device.
Feedback device not correctly
connected to the drive.
1. If an optical encoder is used, verify that the marker pulse is
present and of proper amplitude and width relative to the A and
B channel outputs.
2. If the high resolution magnetic feedback is used, verify the
output signals per Figure 11.4. Adjust the sensor relative to the
gear to obtain proper signals or replace the sensor head.
Malfunctioning feedback device.
If problems were not found with other tests, replace Main Control
Board (CPU Board on A04/A06 drives).
Malfunctioning printed circuit
board.
24
No.
The spindle
overshoots the
target position and
oscillates several
times before
stopping.
Adjust SERVO MODE - HI SPD RANGE P and I gains to obtain
quick stopping without overshoot when the Run command is
energized/de-energized.
Either the velocity loop or the
orient position loop is not tuned
correctly.
25
The accel/decel ramp rate setting limits the decel rate that can be
obtained during orient and a slow decel rate can cause overshoot.
Reduce the value of the Acc Rate #1 or Acc Rate #2 parameter
setting or select the quicker accel/decel rate setting.
The accel/decel ramp rate settings
are too slow relative to the orient
position loop settings.
Reduce the value of the ORIENT TUNE - Orient Speed parameter
setting or increase the value of the ORIENT TUNE - Orient Start
parameter setting. As explained in the 8510 Programming Manual
(publication 8510-5.2), these parameters control the orient position
loop gain and define the required deceleration rate.
The orient mode tuning requires a
faster decel rate than the drive can
provide.
26