Rockwell Automation 8510 AC Spindle Drive System User Manual User Manual
Page 10
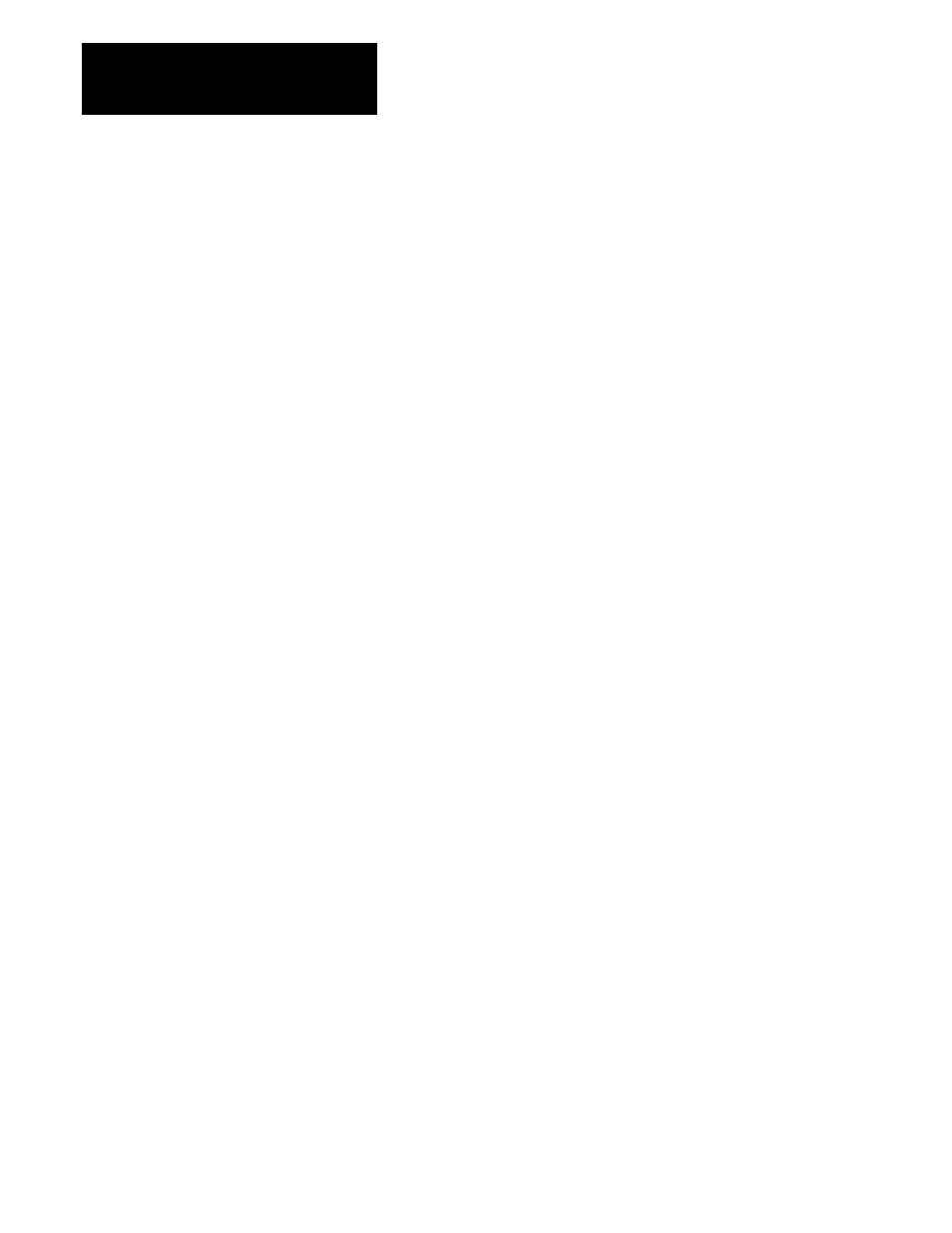
Introduction
Chapter 1
1-6
Control Of Dual Winding Motors
A 12:1 constant power range can be obtained by using dual winding
motors. AC motors are usually wired internally into either a
∆
or a Y
winding configuration. With the dual winding motors, a pair of externally
mounted contactors are used to reconfigure the motor windings between
∆
or Y connections while the motor is running. This winding reconfiguration
shifts the base speed operating point of the motor and effectively extends
the overall constant power operating range. These externally mounted
contactors are directly controlled by the 8510 drive. A single digital input
to the 8510 commands either the low speed or the high speed winding to be
selected. Within about 250 milliseconds, the drive will turn off the motor
current, open one contactor, close the other contactor, turn on the motor
current, and give an output back to the control system to indicate that the
winding has been changed. To prevent excessive speed changes during the
winding change operation, the motor should be running at no load.
With dual winding motors, totally independent parameter sets are stored for
each motor winding to assure optimum performance in each speed range.
When these motors are used, the gear range data sets are limited to three
instead of four. This gives a total of six unique sets of drive parameters (2
motor windings in each of 3 gear ranges).
Power Structure Design
Internal discrete wiring has been nearly eliminated by the use of a printed
circuit board to interconnect the entire power structure. Use of a circuit
board maximizes reliability and simplifies maintenance. The 8510 uses
high frequency, low loss IGBT power devices. The high switching
frequency minimizes motor noise and reduces motor heating. To remove
much of the heat from the drive cabinet, the 8510 heat sink extends through
the rear of the cabinet. As an option, the drive can be mounted inside the
cabinet and cooling air can be ducted out any side of the enclosure.
Programming and Diagnostics
An integral 2 line by 16 character display and 4 button keypad is used for
all programming and diagnostic displays. The menu driven programming
system is powerful yet simple to use. Diagnostic features include a digital
meter, I/O status, and fault displays. Programmed parameters are stored in
EEPROM. In addition, an offline programming system and a file
upload/download utility are available.
Simple Drive Tuning Procedures
All performance adjustments are digital parameters. Analog inputs are
self-zeroing. Scaling of zero and maximum command requires only the
push of a button. All velocity loop gains can be set with the drive
operating.
Programmable Analog Outputs
The user can configure two analog outputs to provide any of eight different
output signals. These include motor or spindle rpm, % load, % maximum
power, and orient error.