Rockwell Automation 8510 AC Spindle Drive System User Manual User Manual
Page 132
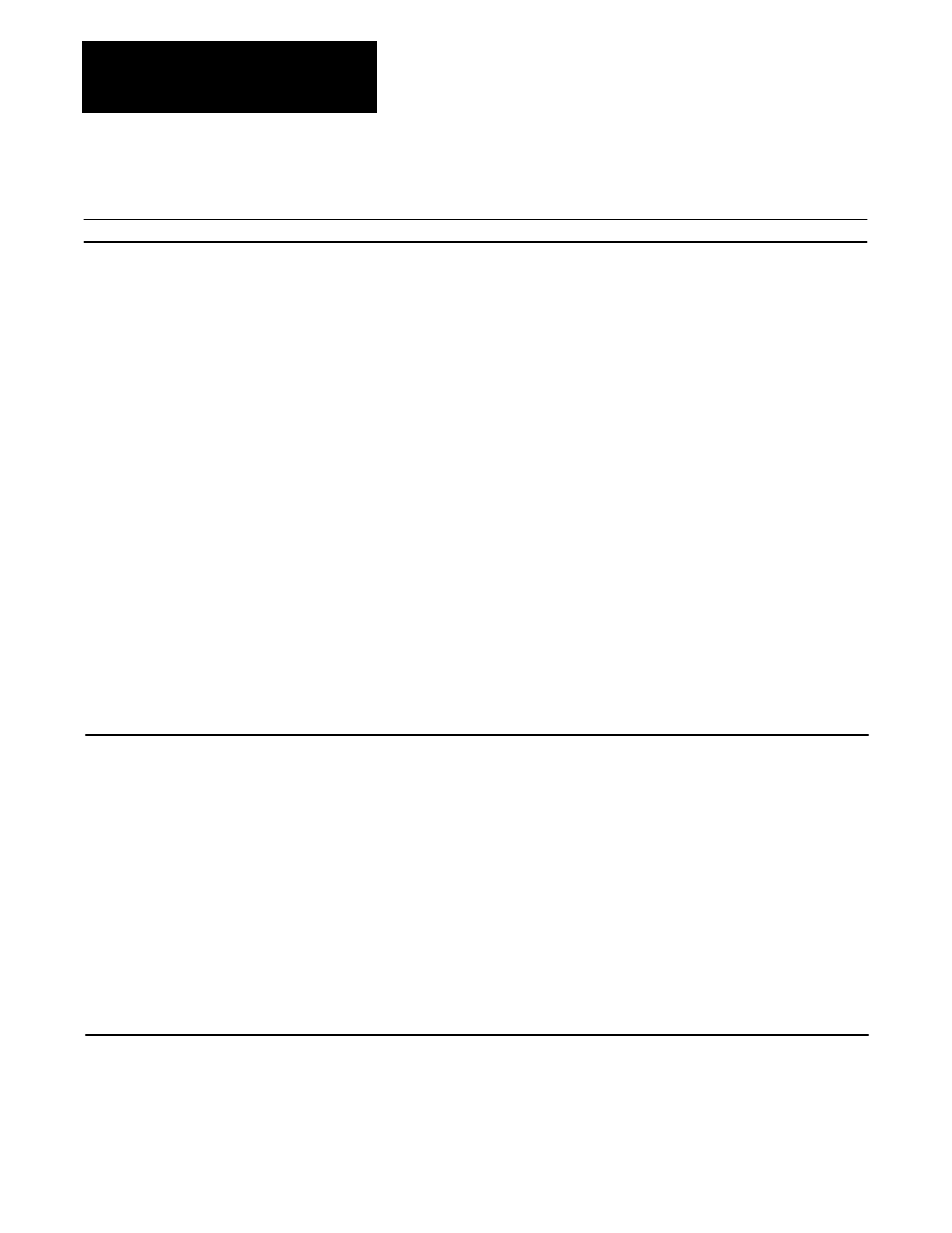
Troubleshooting
Chapter 11
11-128
Table 11.F (Continued)
Problems that Occur while the Drive is Operating
Possible Solutions
Probable Cause
Problem
Spd Error Hi
displayed - A
motor stall condi-
tion or an unex-
pected motor
acceleration or
deceleration was
detected.
Refer to fault condition 6 for solutions.
Resolver or resolver wiring is
malfunctioning.
If problems were not found with other tests, replace Main Control
Board (gate drive and CPU Boards on A04/A06 drives).
Malfunctioning printed circuit
boards.
Mtr Windg Chg displayed - The auxiliary contacts on the winding change contactors did not cycle as expected during the winding
change operation. Whenever the Motor Winding Select – Low/High input is Off, the auxiliary contact on the Low Speed Contactor
should be closed. Whenever the Motor Winding Select – Low/High input is On, the auxiliary contact on the High Speed Contactor
should be closed. This fault is monitored only when a 1327AD series dual winding motor has been selected with the MOTOR
SELECT - Catalog Num parameter.
1. Verify that connector CN1 is properly connected to the drive.
2. Verify that the connector CN1 and the contactors are correctly
wired.
3. Check the cable for continuity.
Interconnection problem between
the drive and the winding change
contactors.
Check the contactors to verify that they operate properly. Verify the
operation of the auxiliary contacts.
One of the winding change
contactors are malfunctioning.
If problems were not found with other tests, replace Main Control
Board (Gate Drive Board and possibly CPU Board on A04/A06
drives).
Malfunctioning printed circuit
board.
If problems were not found with other tests, replace Power Unit.
Malfunctioning Power Unit.
22
23
No.
1. Change duty cycle to reduce required motor torque.
2. Turn Low Torque Limit Select input Off or increase setting of
Low Torq Lmt parameter to allow sufficient torque to drive the
load. Increase rating of motor/drive system if necessary to drive
the load.
Load requires a torque that
exceeds motor torque limit
setting.
Check all power wiring to the motor for continuity and tight
connections. Use an ohmmeter to verify phase to phase continuity
for each motor phase.
Motor phase is open.
Check the contactors to assure they are making proper connections
at all times. Replace contactors if necessary.
(When using 1327AD series dual
winding motors) Malfunctioning
winding change contactor.
Use the parameter PARAMETER SET - ELECT CONFIG - Motor
Phasing to reverse the relative phasing of the motor to the resolver.
If during startup, the motor runs at
a constant low speed or reverses
direction frequently, the motor
versus resolver phasing is incorrect.
Check Catalog Num setting to verify that it matches the motor
nameplate. Incorrect parameter setting can cause torque loss.
Incorrect motor selected in
MOTOR SELECT ~ Catalog Num
parameter.