Rockwell Automation 8510 AC Spindle Drive System User Manual User Manual
Page 127
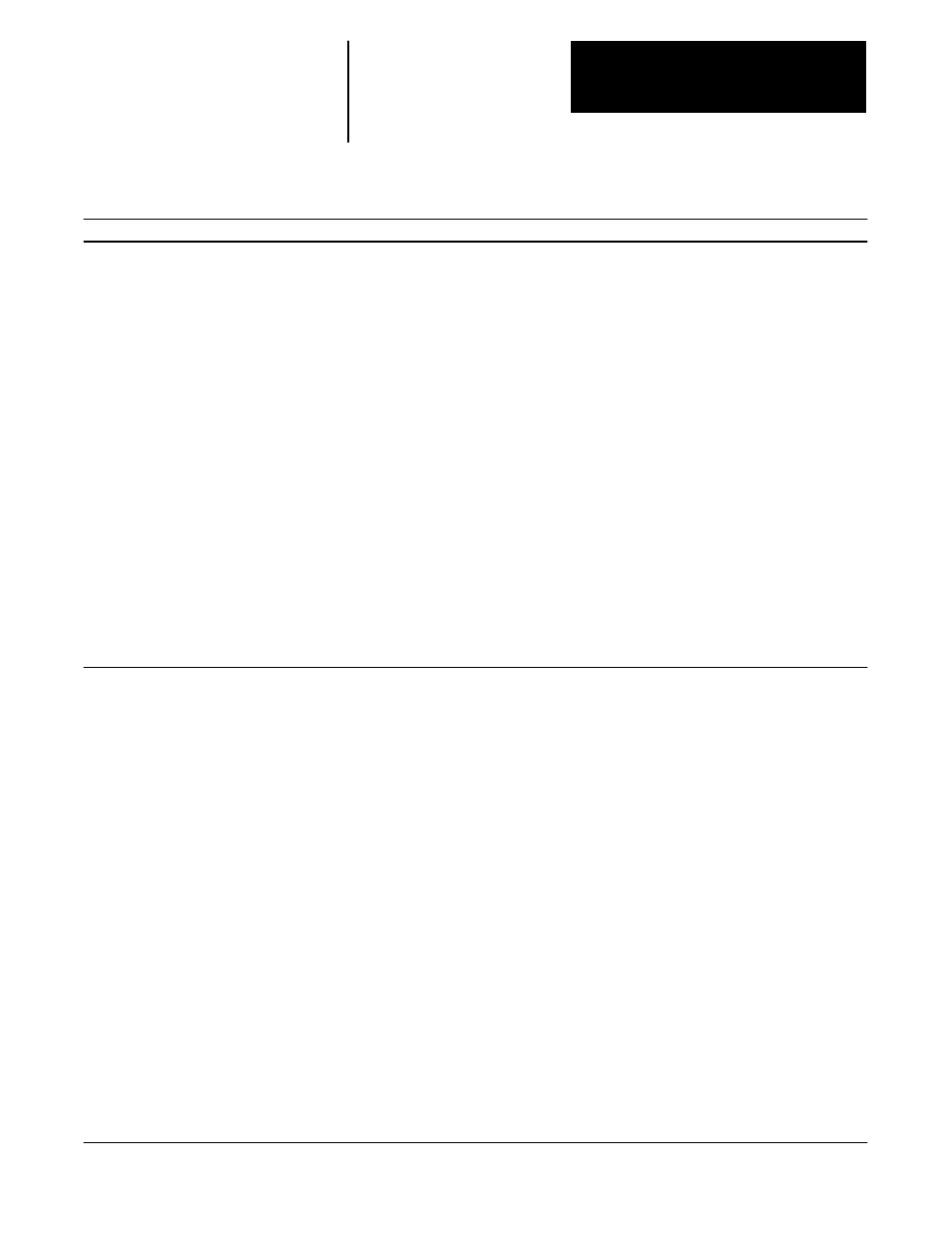
Troubleshooting
Chapter 11
11-123
Table 11.E (Continued)
Problems that Occur when Drive Enable applied (or during operation)
Possible Solutions
Probable Cause
Problem
Convrtr Short
displayed - Current
sensed by DC link
current sensor CT-R
was too high.
Usually indicates
problem with IGBTs
in converter bridge.
Remove power to the drive, and restart.
Momentary power outage while
motor is regenerating to a stop.
1. Check seating of Interconnect Boards into board connectors CN7
and CN8 (CN15 and CN16 on A04/A06 drives).
2. Remove interconnect board from CN7 and CN8 and inspect
contacts in both connectors to assure that they are making proper
contact with the Interconnect Board. Make certain it is inserted
correctly, so that “blank side,” if any, is towards outside of drive.
Malfunctioning drive
interconnections.
Remove all twelve 0.3A fuses and check with ohmmeter. Replace
any bad fuses.
Important: Be certain to properly reseat all fuses to avoid possible
damage to IGBTs.
Possible blown IGBT driver fuse
on Main Control Board (Gate
Drive Board on A04/A06 Drive).
Check IGBT modules M4, M5, and M6 (or IGBT2 in A04/A06
drive) according to procedure provided later in this chapter. Replace
Power Unit if IGBT is malfunctioning.
Malfunctioning IGBT module in
converter bridge.
If problems were not found with other tests, replace Main Control
Board (Gate Drive Board and possibly CPU Board on A04/A06
drives).
Malfunctioning printed circuit
board.
If problems were not found with other tests, replace Power Unit.
Malfunctioning Power Unit
current sensor or circuit board.
Motor Short dis-
played - Current
sensed by motor
phase current sensors
CT-U or CT-V was
too high. Usually
indicates a problem
with the motor or
motor wiring.
Check for proper hookup of contactors, motor, contactor coils, and
auxiliary contacts.
Improper connection of winding
changeover contactors when a
dual winding motor is being used.
Check Catalog Num setting to verify that it matches the motor
nameplate.
Incorrect motor selected in
MOTOR SELECT - Catalog Num
parameter.
Disconnect motor at the drive. Use a megger (high voltage
ohmmeter) to verify that the insulation resistance to ground for each
phase is at least 5 megohm. For dual winding type motors,
disconnect the power wires at the motor terminal box and use the
megger to measure phase-to-phase insulation resistance. Verify that
the insulation resistance between U & V, V & W, and W & U is at
least 5 megohms. For single winding motors, use an ohmmeter to
measure resistance between phases; depending on motor size, value
measured should be from 0.1-1.0 ohms and should be approximately
the same between each phase. Phase-to-phase and internal winding
shorts may not be detected with this test.
Shorted or voltage breakdown of
motor or motor cabling to ground
or another phase.
Verify that the motor power cable is securely fastened to the drive
and motor terminal blocks and that no stray wire strands are shorting
out any phases.
Improper motor power
connections.
Replace the Main Control Board (Gate Drive Board and possibly
CPU Board on A04/A06).
Malfunctioning printed circuit
board.
If problems were not found with other tests, replace the Power Unit.
Malfunctioning Power Unit.
9
10
No.