Rockwell Automation 8510 AC Spindle Drive System User Manual User Manual
Page 134
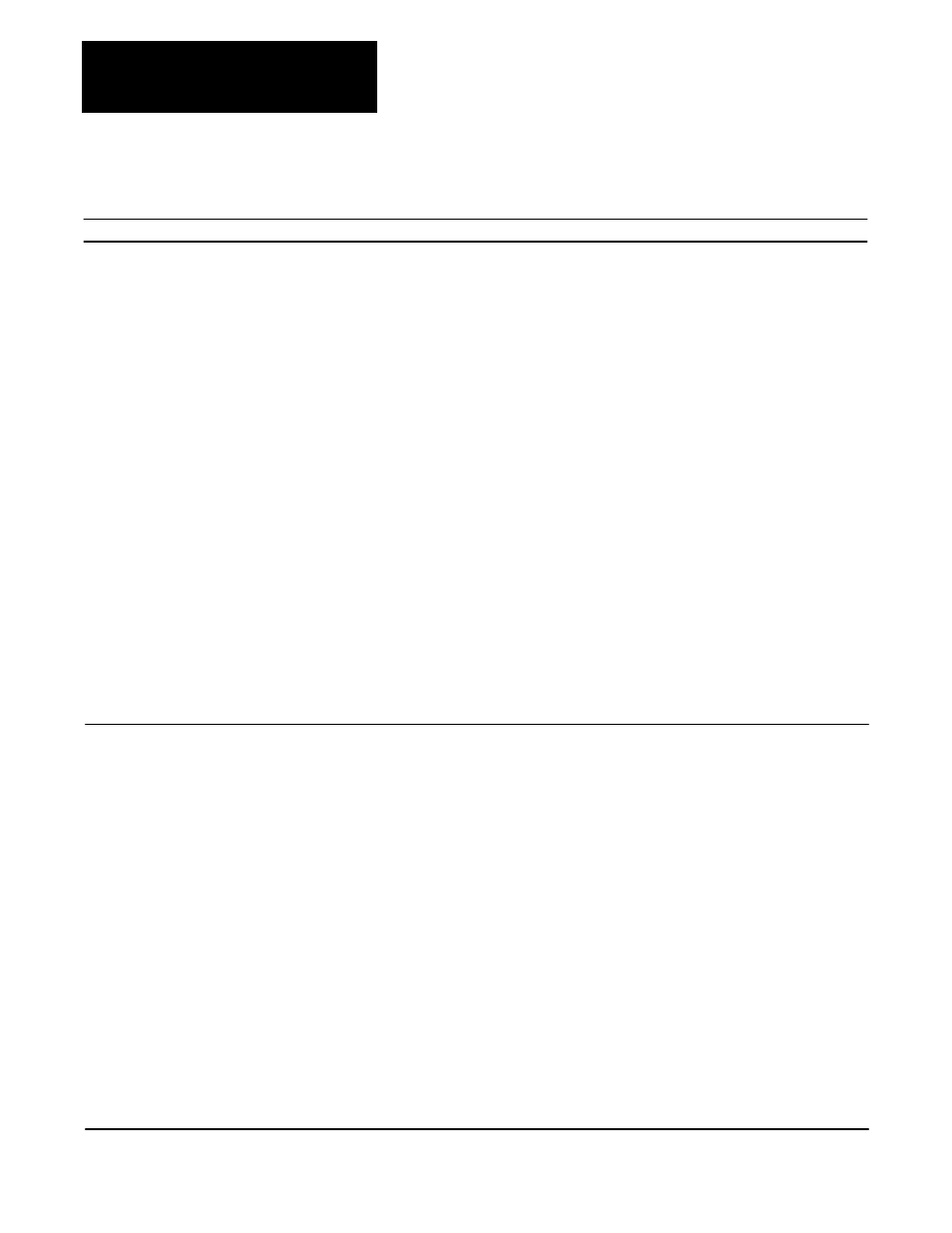
Troubleshooting
Chapter 11
11-130
Table 11.G (Continued)
Problems that Occur during Spindle Orient Operation
Possible Solutions
Probable Cause
Problem
Bad PG Count
displayed - An
incorrect number
of spindle position
feedback counts
was detected
between two
successive markers
pulses as deter-
mined by the
programmed
number of lines on
the feedback
device.
Use the ORIENT SETUP - FEEDBACK DEFN - Encoder Lines
parameter to set the correct encoder line count or number of teeth
on the high resolution feedback gear.
The number of encoder lines has
been incorrectly programmed.
1. Verify that connector CN2 is connected to the drive.
2. Verify the wiring of the connector at the drive and at the
feedback device.
Feedback device not correctly
connected to the drive.
Use the ORIENT SETUP - FEEDBACK DEFN - Encdr Phasing
parameter to reverse the phasing of the orient feedback device.
Feedback device is incorrectly
phased.
1. If an optical encoder is used, verify that the A, B, and Z channel
outputs are present and have proper amplitude/phase
relationships and that the signals are relatively free of electrical
noise.
2. If the high resolution magnetic feedback is used, follow the
procedure shown in Figure 11.4 to verify the output signals.
Adjust the mounting of the gear and the position of the sensor
relative to the gear to obtain proper signals or replace the sensor
head.
Malfunctioning feedback device.
If problems were not found with other tests, replace Main Control
Board (CPU Board on A04/A06 drives).
Malfunctioning printed circuit
board.
Bad PG Output
displayed - The
electrical signals
from the high
resolution magnetic
feedback device
are abnormal.
If an optical encoder is being used, the ORIENT SETUP -
FEEDBACK DEFN - Encoder Type parameter must be set to
“OPTICAL PULSE”. When this parameter is changed and then
stored in EEPROM, AC power must be removed from the drive and
then reapplied to reset this parameter value in the drive control
software.
Wrong type of feedback device has
been specified.
The gear and sensor must be installed in accordance with the
mechanical tolerance specifications in the High Resolution
Magnetic Feedback Instructions (8510-5.13). At test point A on the
Main Control Board (CPU Board of A04/A06 drive), the amplitude
modulation of the signal should be less then 0.1 volts when the gear
is properly installed. The magnitude of the signal can be changed
by changing the gear to sensor airgap.
The gear or sensor are not
correctly installed.
1. Verify that proper signals are received from the sensor. See
Figure 11.4 for correct waveforms.
2. If not correct, check cables and connectors for continuity and
proper connections.
3. If cables and connections are OK, replace sensor.
Interconnecting cable or sensor are
defective.
If problems were not found with other tests, replace Main Control
Board (CPU Board on A04/A06 drives).
Malfunctioning printed circuit
board.
27
28
No.
Either increase the value of ORIENT TUNE - Orient Start or
decrease the value of ORIENT TUNE - Orient Speed.
The ORIENT TUNE - Orient Start
parameter value is much too low
relative to the value of ORIENT
TUNE - Orient Speed parameter.