Rockwell Automation 8510 AC Spindle Drive System User Manual User Manual
Page 103
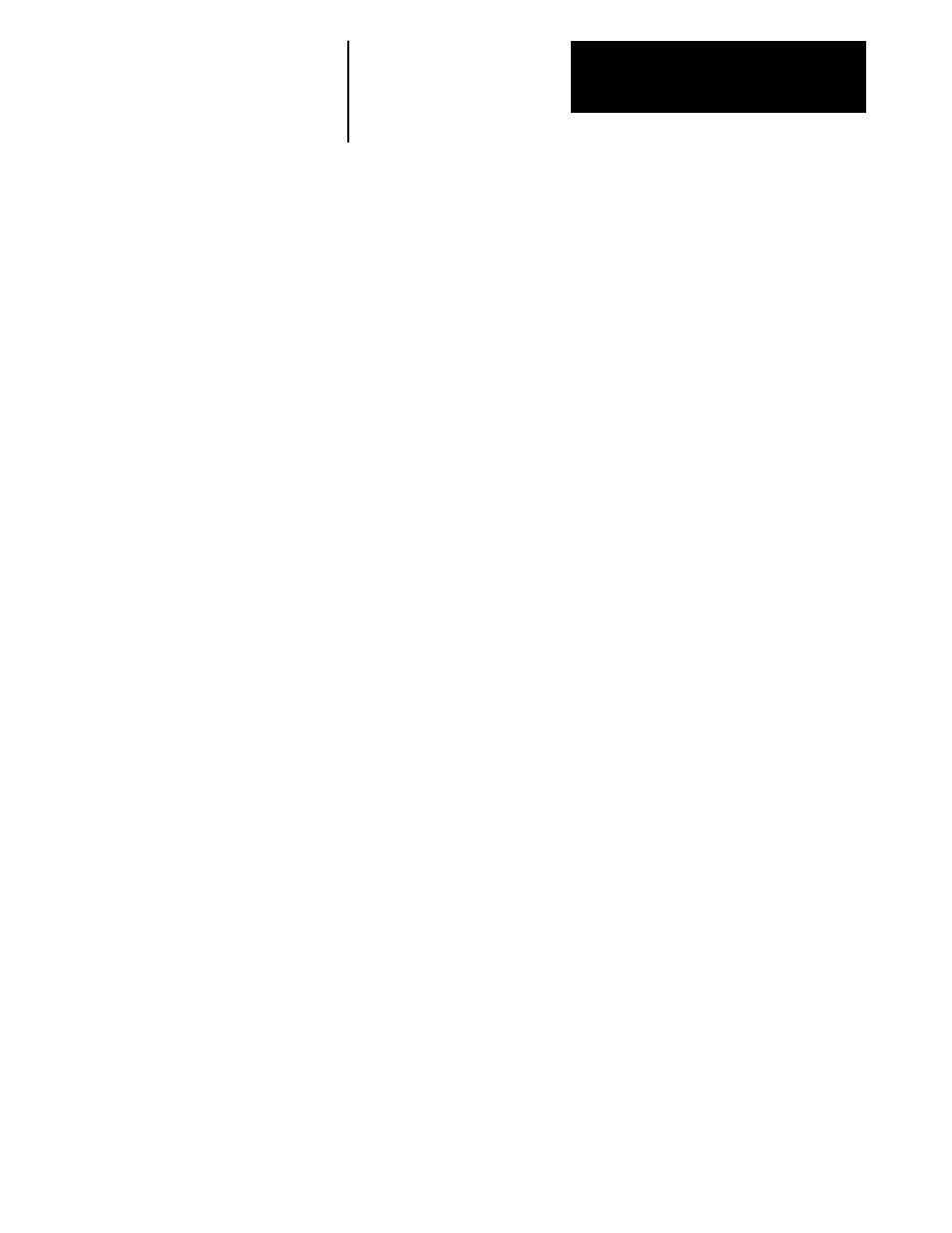
Start-Up
Chapter 9
9-99
o
12. When a positive analog speed command is applied along with the
Forward Run command, the motor should rotate counterclockwise
when viewed from the output shaft end. If it does not rotate in this
direction, remove the Run and Drive Enable inputs. Use the
PARAMETER SET – ELECT CONFIG – Cmnd Phase #1 parameter
to reverse the phasing of the input command. Reapply the Drive
Enable and Run inputs and check for correct operation.
o
13. If an analog speed command is being used, the most accurate
calibration is achieved by allowing the drive to measure the zero
speed command and maximum speed command input voltages.
a) Select the ANALOG CAL – MEASURE INPUT – Zero Volt In
parameter and apply the actual zero speed input command from
the CNC or other control system. Press Select to store the value.
b) Select the ANALOG CAL – MEASURE INPUT – Max +Volt In
parameter and apply the actual maximum speed input command
from the CNC or other control system. Press the Select key to
store the value. This completes the analog channel calibration for
spindle mode.
o
14. Velocity loop compensation can be tuned while the drive is enabled.
The step response of the drive can be tested by applying and
removing the speed command or by turning the Forward (or
Reverse) Run input On and Off. Basic adjustment can be obtained
by observing the motor shaft or spindle as the motor stops in
response to a step command. The Spindl P Gain and Spindl I Gain
should be adjusted to give a smooth, quick stop without visible
motor reversal. When running, the motor should not make growling
or rumbling noises. Excess motor or gear box noise indicates excess
torque ripple and excess gain.
The general effect of the P and I gain parameters is:
- Increasing P shortens response time and increases bandwidth.
- Increasing I increases bandwidth and quickens system response to
load and command transients. Static velocity error is eliminated.
- Too much P will cause high frequency oscillation.
- Too much I will cause overshoot of commanded speed or low
frequency oscillation.
For more accurate setup, an oscilloscope must be used. Following
the procedure in the Programming Manual, program Analog Output
#1 to output Motor Speed and Analog Output #2 to output % Torque.
Simultaeously press the Mode and Scroll – keys twice to store the
parameter changes to EEPROM and cause the display to change to
DISPLAY TYPE – METER DISPLAY. Then remove and reapply
Drive Enable for these settings to take effect. Near the center of the
I/O Board (smaller board in lower left corner of drive) are test points
for Analog Output #1 (ANAOUT#1 – TP1), Analog Output #2
(ANAOUT#2 – TP2), and Analog Signal Ground (ANA-SG – TP4).
On both test points,
±
10V DC = maximum output.