10ć24 – Rockwell Automation 1771-QDC, D17716.5.86(Passport) PLASTIC MOLDING MODULE User Manual
Page 232
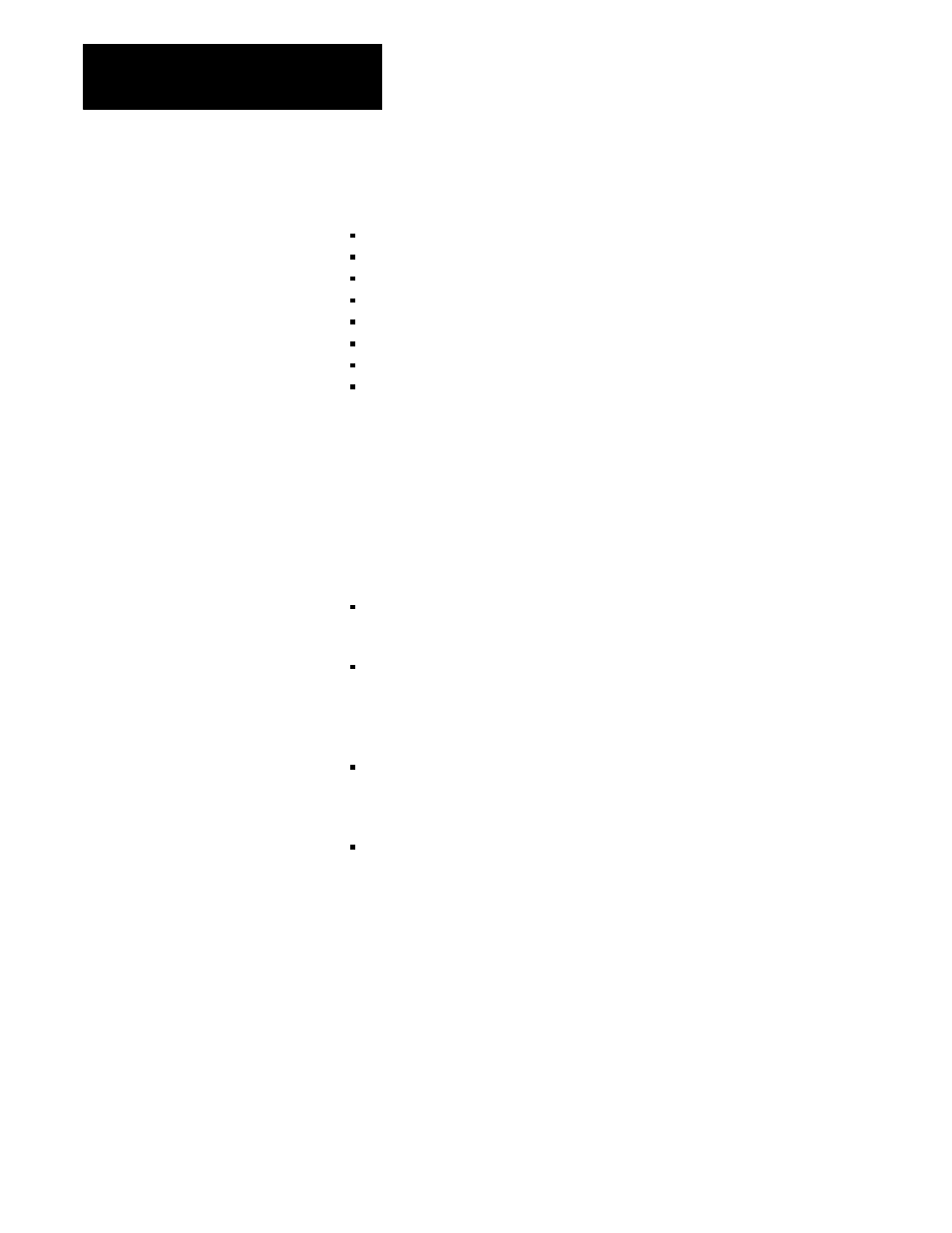
Tune Your Machine
Chapter 10
10-24
In this section, we discuss the usage and effect of the following items as
they apply to clamp operation:
Clamp-control
Objectives
Profile
Requirements
Unselected Valve Set-output Values
Logical Bridges and End-of-profile Set-output Values
Acceleration and Deceleration Ramp Rates
Pressure Alarm Setpoints
Watchdog
Timer
Expert Response Compensation
We assume you are familiar with conventions, terminology, and procedures
used in the Injection Molding Industry, in this manual, and in the Plastic
Molding Module Reference Manual.
Most molders share the following objectives when tuning their clamp
operation and setting up molds to produce parts. These objectives apply to
both toggle and hydraulic machines.
Repeatable mold full open position. Automated removal of parts from
mold cavities makes repeatable mold full open positioning a necessity.
Precise pressure control during low pressure close. This is necessary
to detect obstructions to mold closure and prevent mold damage.
Recent advances in control technology let you do this with closed-loop
algorithms, not relying on hydraulic components and circuit design.
High speed clamp operation. This lets you achieve minimum machine
cycle time with repeatable mold positioning and precise low pressure
close control.
Smooth clamp operation. Abrupt clamp movements can cause
damage to clamp mechanisms and accelerate wear on machine
hydraulics.
Tuning Considerations
for Clamp Operation
ClampĆcontrol Objectives