Rockwell Automation 1771-QDC, D17716.5.86(Passport) PLASTIC MOLDING MODULE User Manual
Page 195
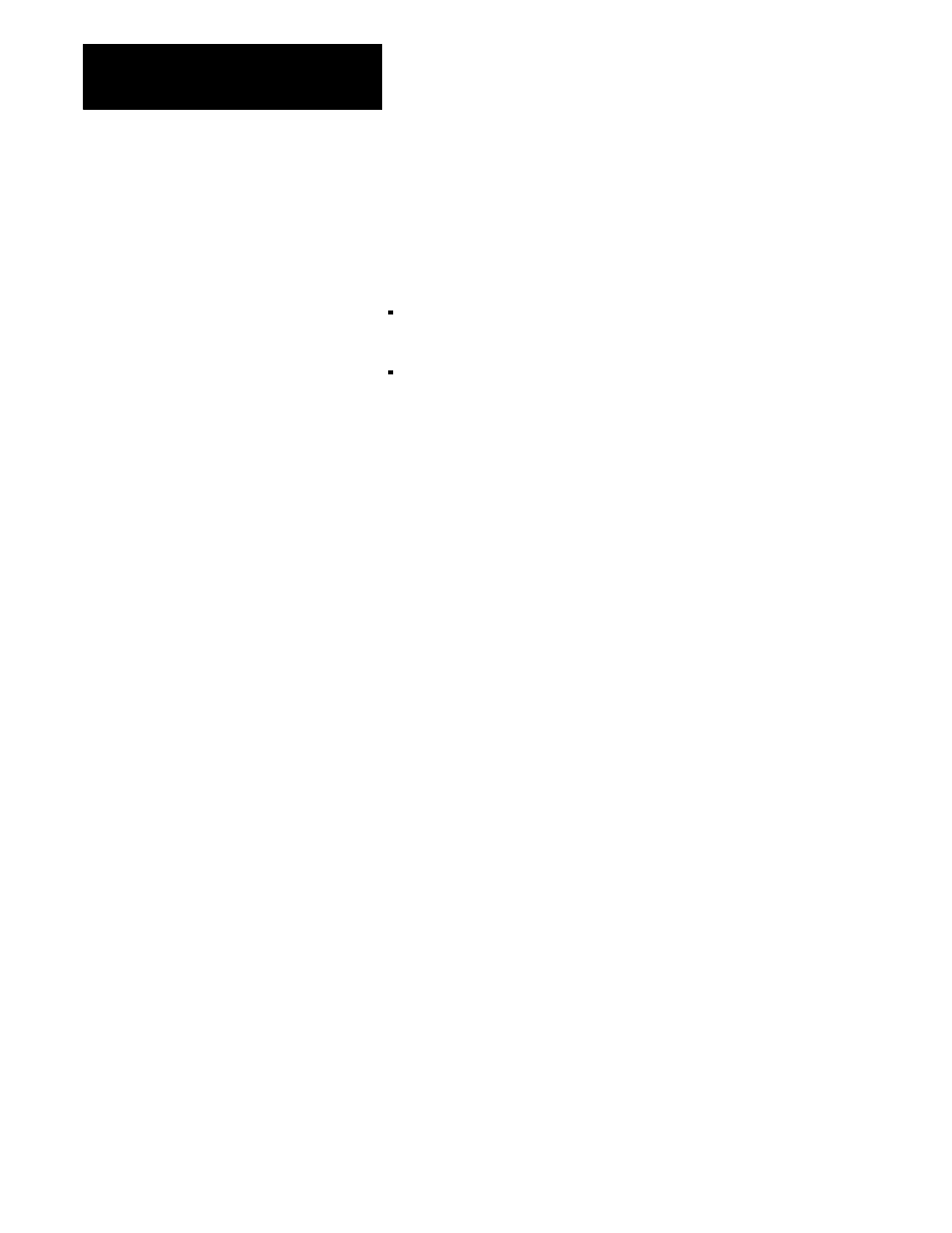
Span Your Valves
Chapter 9
9-38
3.
While observing actual pressure in SYS26 (N40:178) and the output
in SYS41-44 (N40:193-196) that corresponds to the selected
plastication valve, run a plastication backpressure vs. position profile.
Do this by toggling DYC04-B08 (B34/408) from 0 to 1 to 0.
4.
With your programming terminal, record:
maximum profile backpressure displayed in SYS26 (N40:178)
Record here a) ___________
%-output signal in SYS41-44 (N40:193-196) corresponding to the
ram (screw) plastication valve
Record here b)___________
5.
Compute the signal level required for the Selected Pressure Valve,
Output for Maximum PLC44 as follows:
(Max desired (Observed %-signal output in SYS41-44 that
backpressure) x corresponds to the ram plastication valve)
PLC44 = ––––––––––––––––––––––––––––––––––––––––––––––––––
Observed Pressure in SYS26
Important: If your valve is reverse acting, apply the algebraic sign (–) of
value b correctly when computing PLC44.
(PPC10) x (Your recorded value b)
PLC44 = –––––––––––––––––––––––––––
(Your recorded value a)
PLC44 = _______________ For example, 1000 for 10%
6.
Enter new values into the PLC data table:
- value from step 5 into PLC44 (N44:400)
- maximum desired backpressure PPC10 from step 5 into PLC42
(N44:398)
7.
Download the PLC and PPC blocks to the QDC module.
Important: If downloading from your programming terminal, download
PLC followed by PPC with download bits B21/13 and 14 (chapter 4).
8.
Run an open-loop backpressure vs. position profile. Do this by
toggling DYC02-B08 (B34/408) from 0 to 1 to 0.