5 parameters, P503 master function output, P504 pulse frequency – NORD Drivesystems BU0505 User Manual
Page 119: P505 absolute mini. freq
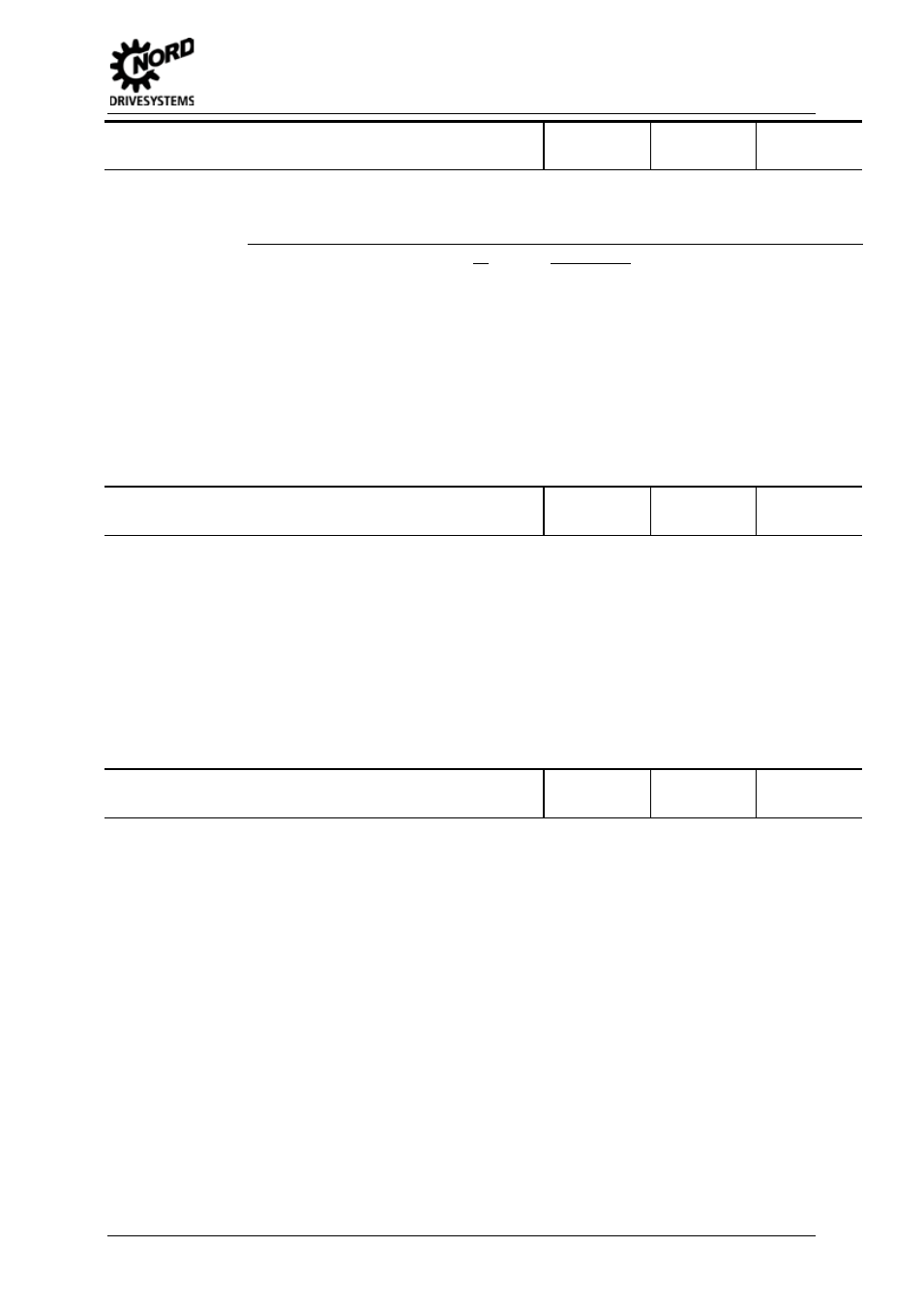
5 Parameters
BU 0505 GB-1013
119
P503
Master function output
(Master function output)
S
0 ... 5
{ 0 }
For master-slave applications this parameter specifies on which bus system the master transmits
the control word and the master values (P502) for the slave. On the slave, parameters (P509),
(P510), (P546 ... ) define the source from which the slave obtains the control word and the master
values from the master and how these are to be processed by the slave.
0 = Off:
no output of control word and master values.
1 = USS:
output of control words and master values to USS.
2 = CAN:
output of control words and master values to CAN (up to
250 kBaud).
3 = CANopen:
output of control words and master values to CANopen.
4 = System bus active:
no output of control word and master values, however via the
ParameterBox or NORD CON, all participants which are set
to System bus active are visible.
5 = CANopen+Sys.bus active: output of control word and master values on CAN open via
the ParameterBox or NORD CON, all participants which are
set to system bus active are visible.
Pos : 263 /Anleit ungen/5. / 6. Parametrier ung [BU 0500 / BU 0200]/ Par ameter/ P500-P599/ Paramet er P504 – Pulsfreq uenz @ 0\ mod_1328091806774_388. doc x @ 10973 @ @ 1
P504
Pulse frequency
(Pulse frequency)
S
3.0 ... 16.0 kHz
{ 6.0 / 4.0 }
The internal pulse frequency for controlling the power unit can be changed with this parameter. A
higher setting reduces motor noise, but leads to increased EMC emissions and reduction of the
possible motor nominal torque.
NOTE:
The radio interference suppression limit curve A 1 according to EN 55011 is
complied with
using the standard value (FI output power ≤ 37 kW: 6.0 kHz,
otherwise 4.0 kHz) and taking the wiring guidelines into account.
NOTE:
Raising the pulse frequency leads to a reduction of the possible output current,
depending on the time (I
2
t curve). When the temperature warning limit (C001) is
reached, the pulse frequency is gradually reduced to the standard value If the
inverter temperature reduces sufficiently, the pulse frequency is increased to the
original value.
Pos : 264 /Anleit ungen/5. / 6. Parametrier ung [BU 0500 / BU 0200]/ Par ameter/ P500-P599/ Paramet er P505 – Absol ut e Mi nimalfr equenz @ 0\ mod_1328091889383_388. doc x @ 10996 @ @ 1
P505
Absolute mini. freq.
(Absolute minimum frequency)
S
P
0.0 ... 10.0 Hz
{ 2.0 }
States the frequency value that cannot be undershot by the FI. If the setpoint becomes smaller
than the absolute minimum frequency, the FI switches off or changes to 0.0Hz.
At the absolute minimum frequency, braking control (P434) and the setpoint delay (P107) are
actuated. If a setting value of "Zero" is selected, the brake relay does not switch during reversing.
When controlling lift equipment without speed feedback, this value should be set to a minimum of
2Hz. From 2Hz and higher, the current control of the FI operates and a connected motor can
supply sufficient torque.
NOTE:
Output frequencies < 4.5 Hz lead to current limitation. For further details, see Section 8.5,
Pos : 265 /Anleit ungen/5. / 6. Parametrier ung [BU 0500 / BU 0200]/ Par ameter/ P500-P599/ Paramet er P506 – Aut omatis che St örungsquitti erung @ 0\mod_1328091934274_388. doc x @ 11019 @ @ 1