Time proportioning control, Trend displays, Tuning – West Control Solutions Pro-EC44 User Manual
Page 240: Tuning menu, Tuned, Time proportional control, Time proportioning, Trend display, Automatic tuning, And tuning
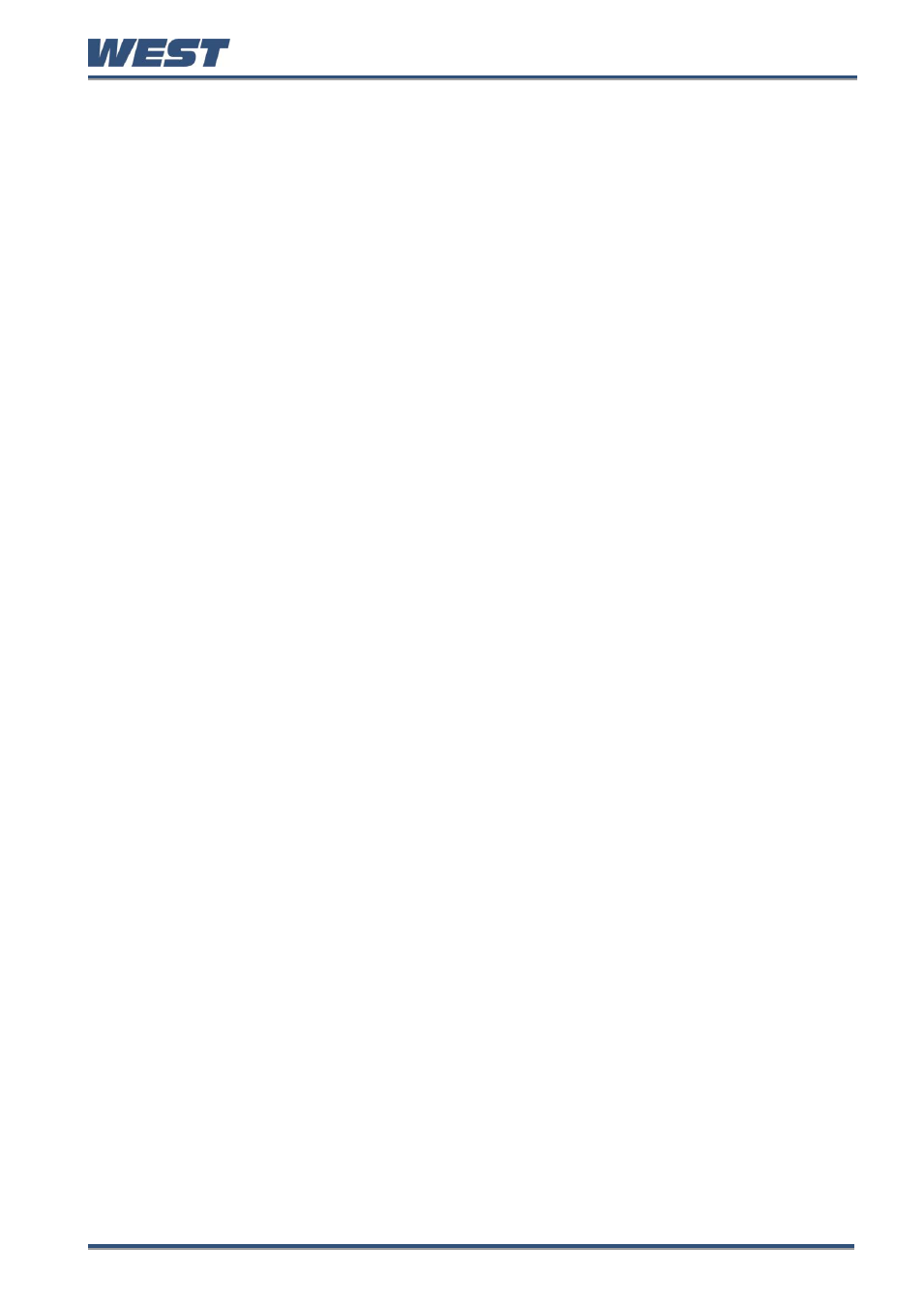
Pro-EC44 2-Loop Graphical Profile Controller & Recorder
Pro-EC44 Product Manual - 59540-1 October 2013
Page 233
Time Proportioning Control
Time proportioning control is accomplished by cycling the output on and off during the
prescribed cycle time, whenever the process variable is within the proportional band(s). The
PID control algorithm determines the ratio of time (on vs. off) to achieve the level of the
correcting variable required to remove the control deviation error. E.g. for a 32 second cycle
time, 25% power would result in the output turning on for 8 seconds, then off to 24 seconds.
This type of output might be used with electrical contactors, solid state relays or solenoid
valves. Time proportioning control can be implemented with relay, triac or SSR driver
outputs.
Also refer to: Control Deviation; Correcting Variable; Continuous Control; Cycle Time; PID;
Primary Proportional Band; Relay; Secondary Proportional Band; Solenoid Valve; SSR and
Triac.
Trend Displays
Trend views are a standard feature on all models. They graphically represent recent process
conditions for the control loops, showing the most recent 120 out of 240 stored data points.
This data can be the process variable; process variable & setpoint (shown as a doted line) or
the minimum and maximum value of the process variable measured since the last sample.
The scaling adjusts automatically to the visible data. Any active alarms are indicated above
the graph. The user can scroll the right hand cursor line back to examine all 240 data points.
Their sample interval and data to display is set in display configuration.
Unlike the optional data recorder, trend views do not retain the stored data if the power is
turned off.
Also refer to: Alarm Types; Display Configuration; Operation Mode; and Process Variable;
Setpoint.
Tuning
PID Controllers must be tuned to the process in order for them to attain the optimum level of
control. Adjustment is made to the tuning terms either manually, or via the automatic tuning
facilities. Tuning is not required if the controller is configured for on-off Control.
Also refer to: Auto Pre-Tune; Controller; Derivative Action; Integral Action; On-Off control;
PID; Pre-Tune; Primary Proportional Band; Self-Tune; Secondary Proportional Band and
Tuning Menu.
Tuning Menu
The tuning menu can be accessed from the main menu. This menu is lock-code protected.
It gives access to the pre-tune, auto pre-tune and self-tune facilities. These assist with PID
tuning, by setting up Proportional bands, Integral and Derivative time values.
Pre-tune can be used to set PID parameters initially. Self-tune may then be used to optimise
the tuning if required. Pre-tune can be set to run automatically after every power-up by
enabling Auto Pre-Tune.
Refer to the Automatic Tuning information in the Configuration & Use section.
Also refer to: Auto Pre-Tune; Derivative Action; Integral Action; Lock Codes; Main Menu; On-
Off control; PID; Pre-Tune; Primary Proportional Band; Self-Tune and Secondary
Proportional Band.