Controller, Controller mode, Correcting variable – West Control Solutions Pro-EC44 User Manual
Page 218: Custom display mode, Cycle time, Data recorder, Deadband
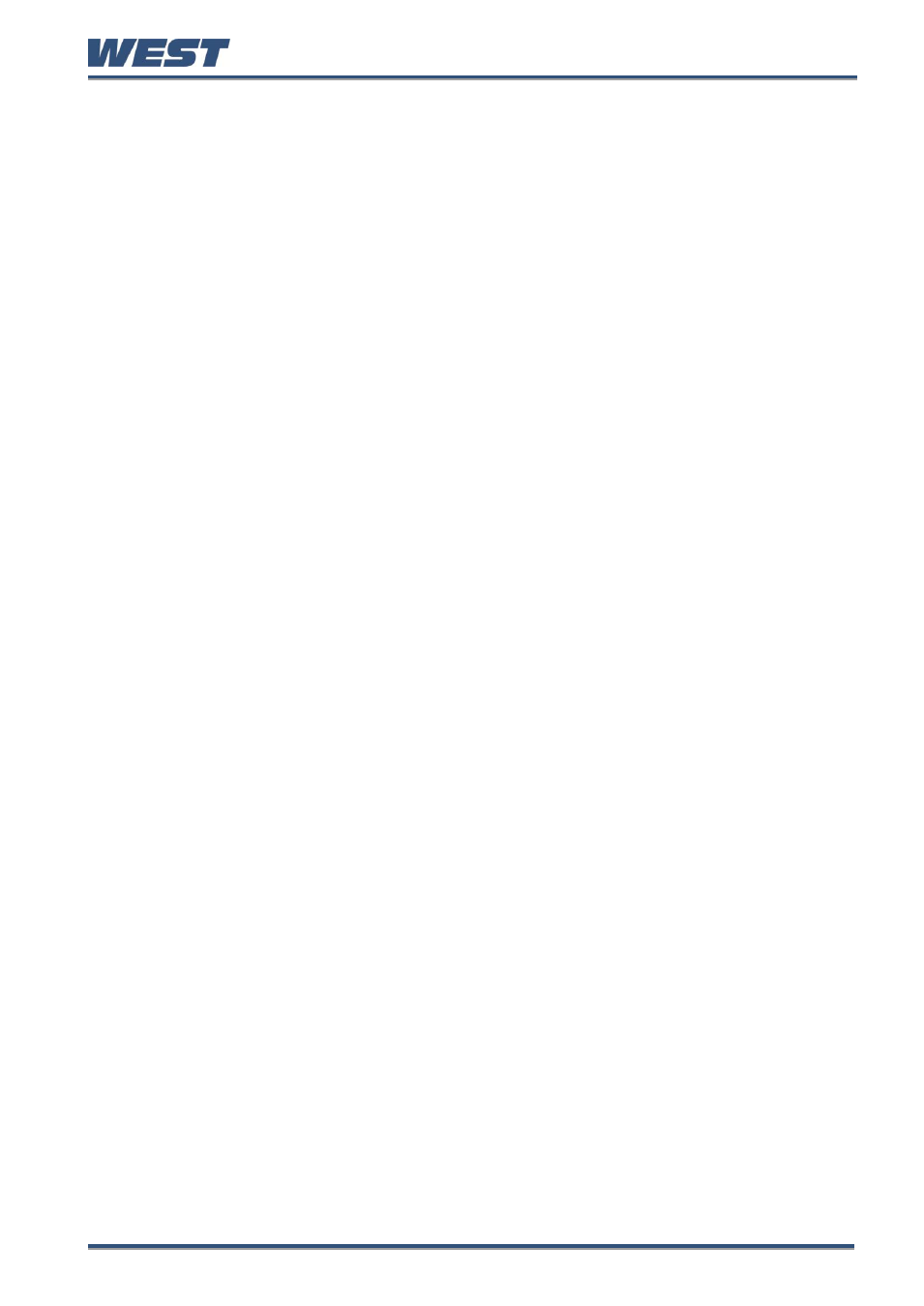
Pro-EC44 2-Loop Graphical Profile Controller & Recorder
Pro-EC44 Product Manual - 59540-1 October 2013
Page 211
Controller
An instrument that controls one or more process control loops. For each control loop it
compares a process variable to a target setpoint, and attempts to make the process maintain
the setpoint value by applying a correcting variable (e.g. turning on a heater or dosing with
alkali if controlling pH). The controller uses proportional (P, PI, PD o PID) or On-Off control.
Also refer to: Correcting Variable; Indicator; Limit Controller; On-Off Control; PD Control; PI
Control; PID; Process Variable; Proportional Control; Profiler and Setpoint.
Controller Mode
The normal operating mode when profiling is not fitted or it is not being used.
Also refer to: Controller; Profiler and Profiler Mode
Correcting Variable
The output level from a controller used to adjust the process variable up or down, in order to
remove any control deviation. This might be turning on a chiller in a temperature application
or increasing the variable speed drive of a pump in a flow application. The level of correcting
variable is commonly referred to as the controller output power.
Also refer to: Control Deviation; PID; Primary Power Output Limit and Process Variable
CPU
This stands for Central Processing Unit and refers to the on-board microprocessor that
controls the measurement, control, alarm; display and other functions of the instrument.
Custom Display Mode
The user can copy up to 50 Configuration Menu parameters into operation mode using the
PC software. If enabled in the display configuration sub-menu, the configured parameters
follow the normal operation mode screens. In this mode these screens are not protected by a
lock code.
Also refer to: Control Configuration; Display Configuration; Lock Codes and Operation Mode
Cycle Time
For time proportioning outputs, the cycle time is the period over which the controller
averages the ON vs. OFF time, in order to provide the required correcting variable. Each
control loop has separate cycle times for the primary and secondary control outputs. Shorter
cycle times give better control, but at the expense of reduce life for any electromechanical
control devices (e.g. relays or solenoid valves). Short cycle times do not harm SSRs.
Also refer to: Correcting Variable; PID; Primary Proportional Band; Proportional Control;
Relay; Secondary Proportional Band; Solenoid Valve; SSR and Time Proportioning.
Data Recorder
The Data Recorder option can record the process values, setpoints, alarms and events over
time. Recordings can be transferred to a USB memory stick or via the serial communications
options for analysis in the PC software or spreadsheets. This option includes a battery
backed-up real time clock (RTC) which continues to keep time when the instrument is
powered down.
Refer to the Data Recorder Option section of this manual for full details.
Also refer to: PC Software and Recorder Configuration.
Deadband
- Refer to Overlap/Deadband.