Profile setup via modbus – West Control Solutions Pro-EC44 User Manual
Page 194
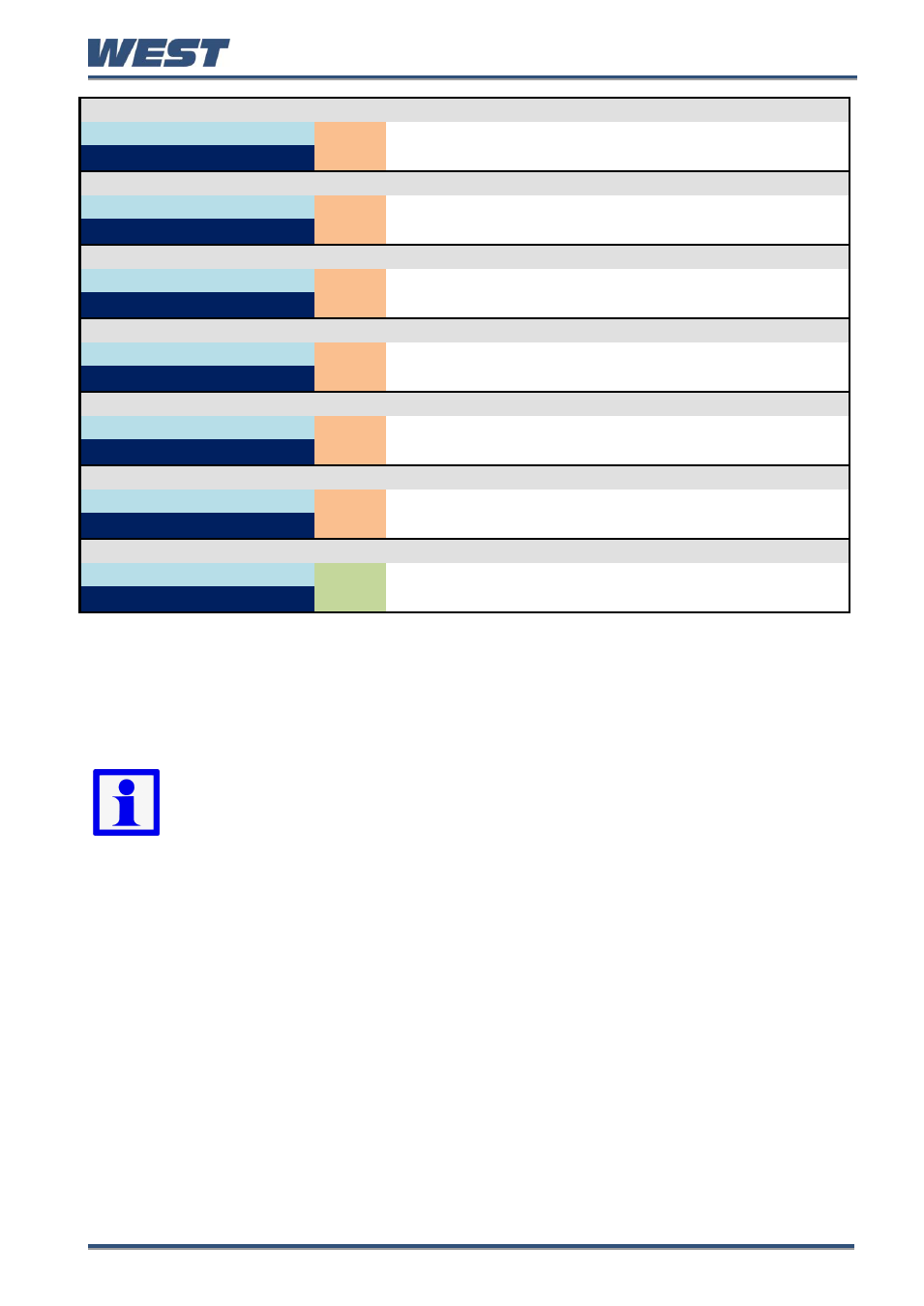
Pro-EC44 2-Loop Graphical Profile Controller & Recorder
Pro-EC44 Product Manual - 59540-1 October 2013
Page 187
Current Profile Running Time
Current Profile Running Time
Dec
8235
24619 49238
RO
The elapsed time of the current running profile in seconds since
it began running.
Hex
202B
602B
C056
Current Profile Remaining Time
Current Profile Remaining Time
Dec
8236
24620 49240
RO
The remaining time for the current running profile before
reaching its end segment, in seconds
Hex
202C
602C
C058
Current Segment Running Time
Current Segment Running Time
Dec
8237
24621 49242
RO
The elapsed time of the current profile segment in seconds
Hex
202D
602D
C05A
Current Segment Remaining Time
Current Segment Remaining Time
Dec
8238
24622 49244
RO
The remaining time for the current profile segment in seconds
Hex
202E
602E
C05C
Total Hold Time
Total Hold Time
Dec
8239
24623 49246
RO
Total (accumulated) time the current profile has been held in
seconds
Hex
202F
602F
C05E
Current Segment Loops Run
Number of Current Segment Loop-backs
Dec
8240
24624 49248
RO
The number of times the current looping segment has looped
back
Hex
2030
6030
C060
Profile Setup
Profile Setup via Modbus
Dec
8198
24582 49164
RW
Note: Refer to the Profile Setup Over Modbus information
below for setting up profiles via comms
Hex
2006
6006
C00C
Profile Setup via Modbus
The information in this section is intended for advanced users writing their own software
code. Most users will create or edit profiles using the instrument keypad, or using the the PC
software (available from your supplier). Either method allows quick and easy editing of
profiles.
Advanced users can setup or edit profiles by writing to the Profile Configuration parameter at
address 8198 (0x2006). This can only be accessed by using Modbus function code 23
(0x17). The instrument replies with a status message.
When creating a new profile the steps below must be followed exactly, either to create a
profile at the next available position, or at the position you specify.
Each message in the sequence includes a 2 byte Command Code that tells the instrument
the purpose of the message, and therefore the meaning of the data contained in it.
Instruction Sequence to create a profile at the next available position
1. Create a profile by writing the profile header data using the Command Code value CP
(0x43, 0x50). This starts the profile creation process by reserving a profile memory slot.
The profile number is returned by the instrument in the Edit Response Message.
Note: There is a global block on profile creation or editing via Modbus while a
profile is running. An attempt to do so returns the error code 0x15.
The only profile related commands allowed while a profile runs are the Profile
Control & Status Parameters in the previous section.