Yaskawa Sigma-5 User Manual: Design and Maintenance - Rotary Motors User Manual
Page 166
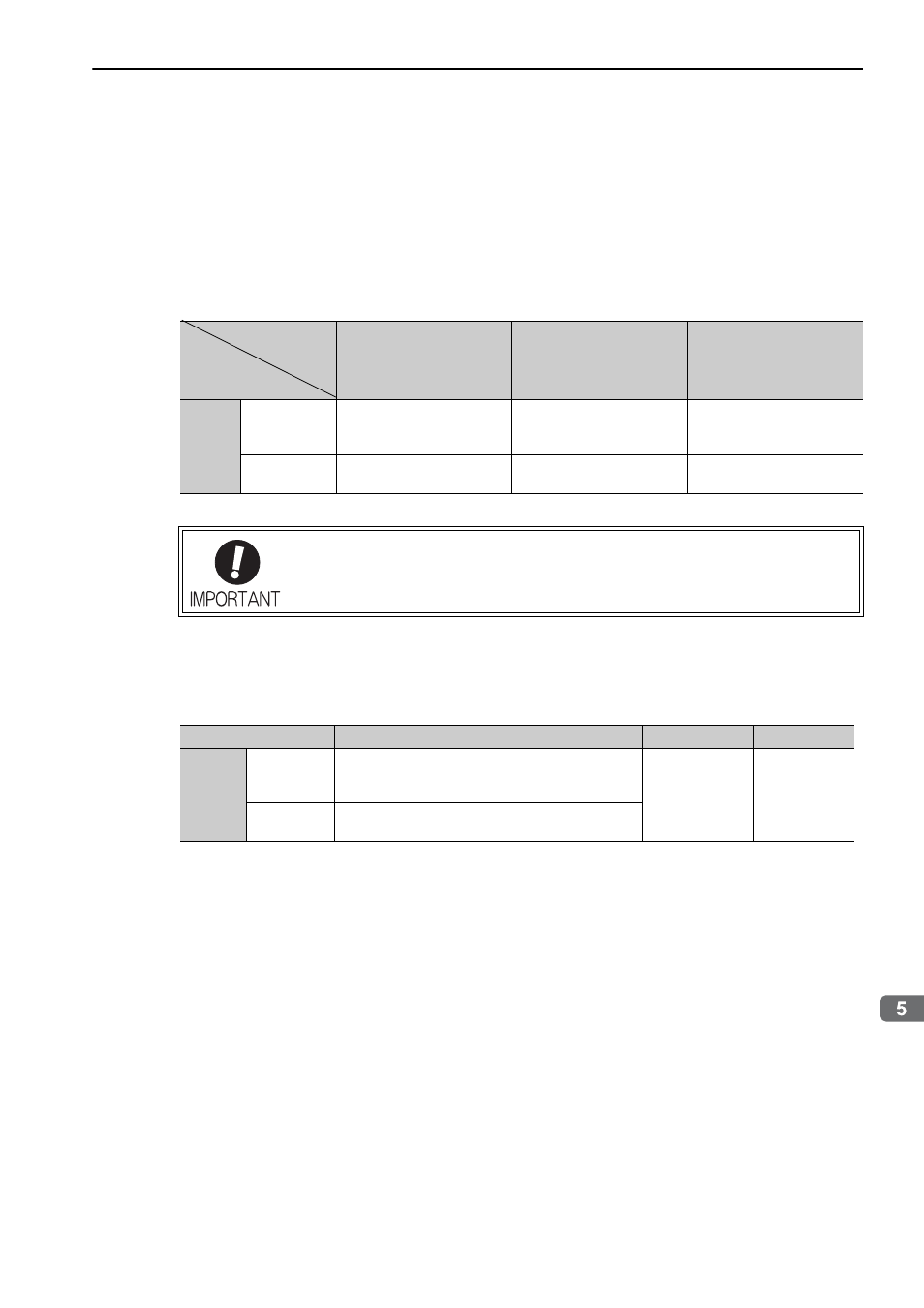
5.4 Advanced Autotuning by Reference (Fn202)
5-29
Adjustments
Friction Compensation
This function compensates for changes in the following conditions.
• Changes in the viscous resistance of the lubricant, such as the grease, on the sliding parts of the machine
• Changes in the load resistance resulting from fluctuations in the machine assembly
• Secular changes in the load resistance
Conditions to which friction compensation is applicable depend on the mode. The friction compensation set-
ting in Pn408.3 applies when the mode is 1.
Feedforward
If Pn140 is set to the factory setting and the mode setting is changed to 2 or 3, the feedforward reference
(Pn109) (refer to 5.9.1) will be lost.
The following settings are required if model following control is used from the host controller (through the
command option module) together with the speed feedforward input or torque feedforward input.
Mode = 1
Mode = 2
Mode = 3
Pn408
n.0
[Factory
setting]
Adjusted without the friction
compensation function.
Adjusted with the friction
compensation function.
Adjusted with the friction
compensation function.
n.1
Adjusted with the friction
compensation function.
Adjusted with the friction
compensation function.
Adjusted with the friction
compensation function.
• Model following control is used to make optimum feedforward settings in the servo.
Therefore, model following control is not used from the host controller together with
either the speed feedforward input or torque feedforward input. An improper speed
feedforward input or torque feedforward input may result in overshooting.
Mode
Friction
Compensation
Selecting
Parameter
Function
When Enabled
Classification
Pn140
n.0
Model following control is not used together with
speed/torque feedforward input.
[Factory setting]
Immediately
Tuning
n.1
Model following control is used together with speed/
torque feedforward input.