3 monitoring analog signals, 1) monitor signal – Yaskawa Sigma-5 User Manual: Design and Maintenance - Rotary Motors User Manual
Page 142
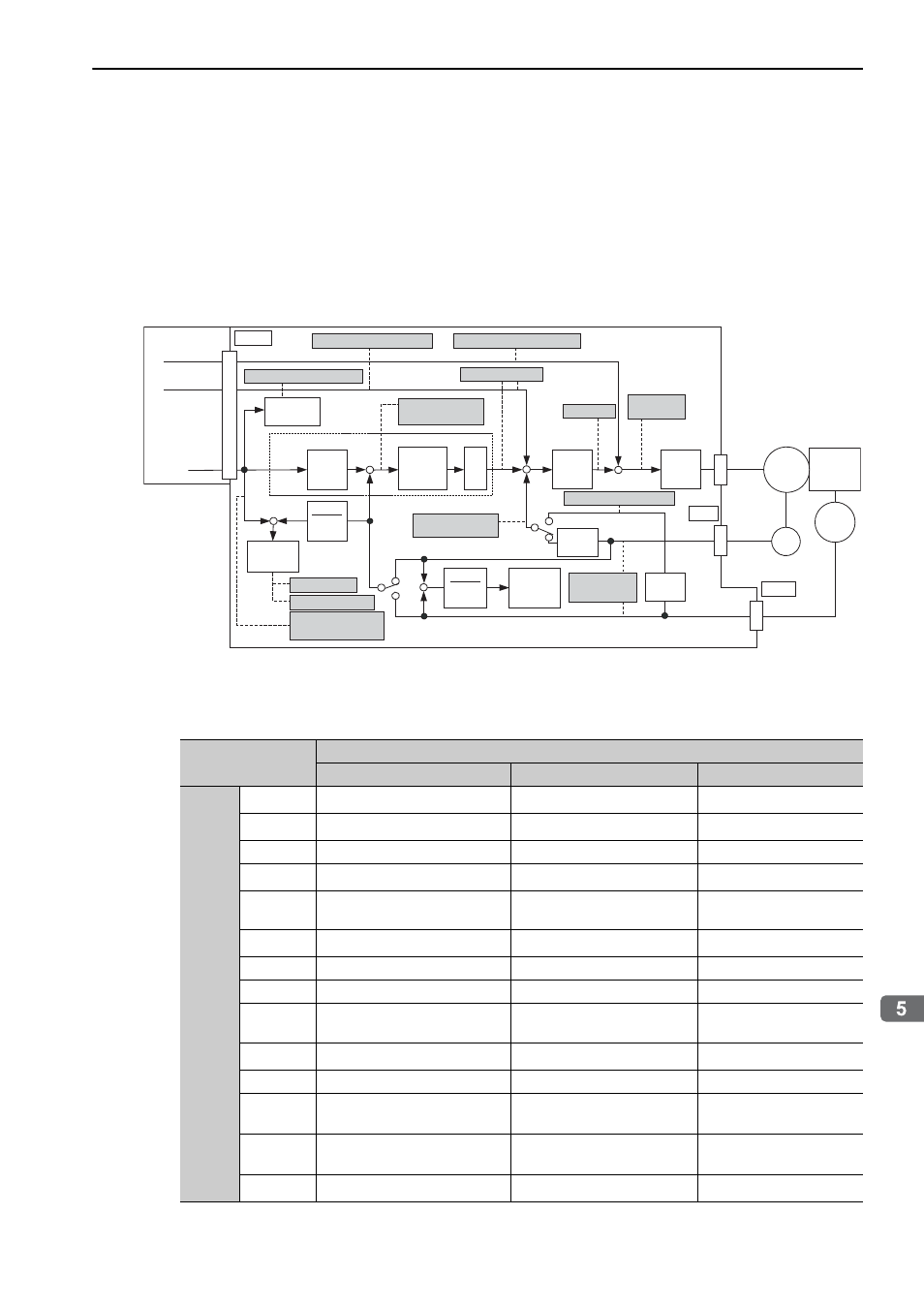
5.1 Adjustments and Basic Adjustment Procedure
5-5
Adjustments
5.1.3 Monitoring Analog Signals
Check the operating status and signal waveform when adjusting the servo gain. Connect a measuring instru-
ment, such as a memory recorder, to connector CN5 on the SERVOPACK to monitor analog signal waveform.
The settings and parameters for monitoring analog signals are described in the following sections.
(1) Monitor Signal
The analog signals that can be monitored are shaded in the following diagram.
The following signals can be monitored by selecting functions of parameters Pn006 and Pn007.
Pn006 is used for analog monitor 1 and Pn007 is used for analog monitor 2.
Kp
1
(U/V/W)
-
+
+
-
+
+ +
+
-
-
+
1
Command
option module
1
M
Kp
CN31
ENC
CN2
CN10
Torque
feedforward
Speed
feedforward
Position
reference
SERVOPACK
Speed feedforward
Position reference speed
Position
amplifier error
Motor rotational
speed
Speed reference
Active gain
Torque
reference
Speed
conversion
Electric
gear
Speed
loop
Current
loop
Fully-closed loop (option)
Electric
gear
Electric
gear
Position loop
Torque feedforward
Error
counter
Error
counter
Error
counter
Load
Position Error
Positioning completed
Completion of position
reference completed
External encoder speed
Speed
conversion
Speed
conversion
Motor - load
position error
External
ENC
Parameter
Description
Monitor Signal
Measurement Gain
Remarks
Pn006
Pn007
n.00
Motor speed
1 V/1000 min
-1
Pn007 Factory Setting
n.01
Speed reference
1 V/1000 min
-1
−
n.02
Torque reference
1 V/100% rated torque
Pn006 Factory Setting
n.03
Position error
0.05 V/reference unit
0 V at speed/torque control
n.04
Position amplifier error
0.05 V/encoder pulse unit
Position error after elec-
tronic gear conversion
n.05
Position reference speed
1 V/1000 min
-1
−
n.06
Reserved
−
−
n.07
Motor-load position error
0.01 V/reference unit
−
n.08
Positioning completed
Positioning completed: 5 V
Positioning not completed: 0 V
−
n.09
Speed feedforward
1 V/1000 min
-1
−
n.0A
Torque feedforward
1 V/100% rated torque
−
n.0B
Active gain
1 st gain: 1 V
2 nd gain: 2 V
−
n.0C
Completion of position reference
Completed: 5 V
Not completed: 0 V
−
n.0D
External encoder speed
1 V/1000 min
-1
Value at motor shaft