8 universal pecking (cycle 205), Cycle run, Please note while programming – HEIDENHAIN TNC 128 (77184x-02) User Manual
Page 410: Universal pecking (cycle 205)
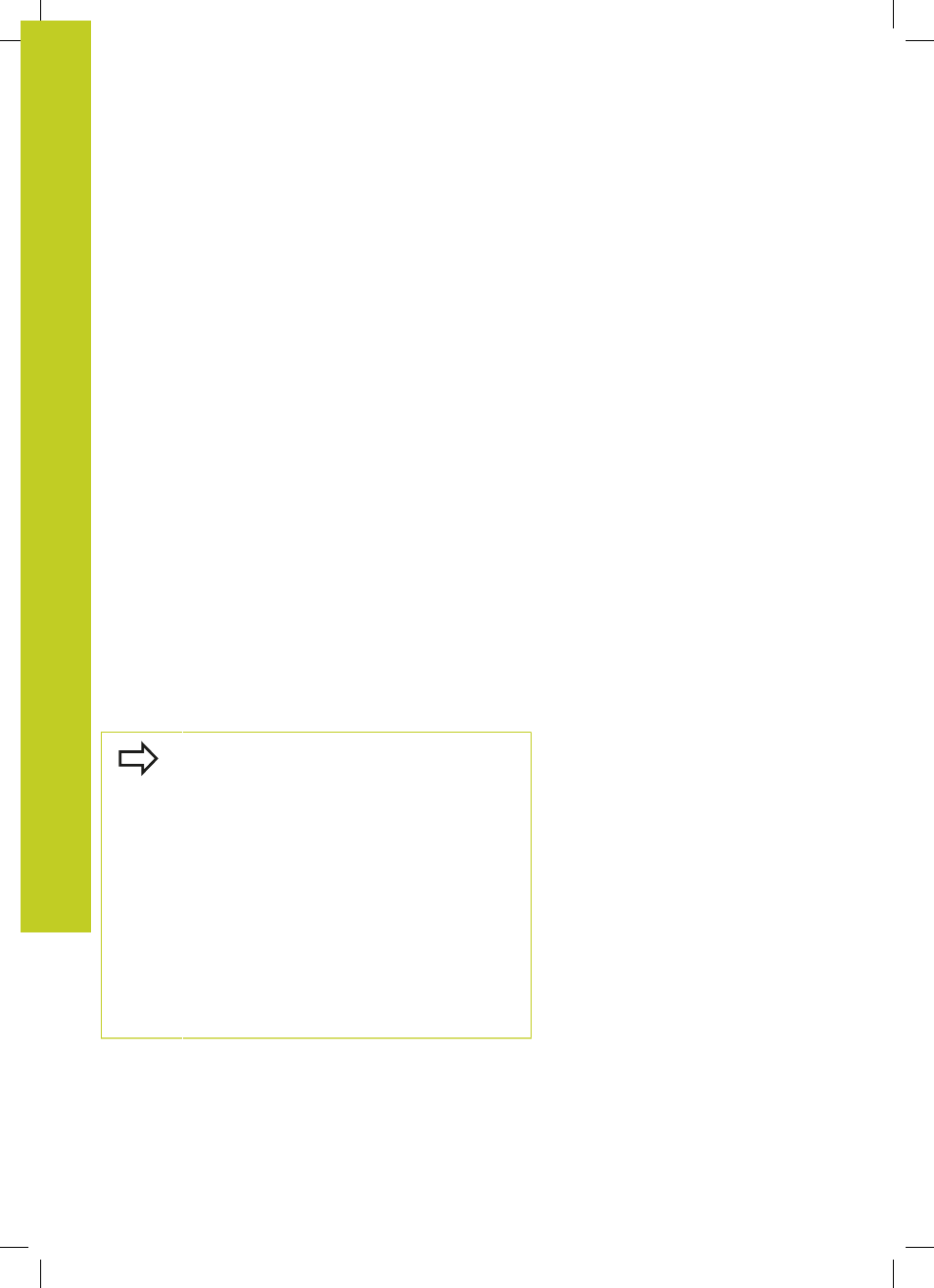
Drilling, boring and thread cycles
16.8 UNIVERSAL PECKING (Cycle 205)
16
410
TNC 128 | User's Manual HEIDENHAIN Conversational Programming | 5/2014
16.8
UNIVERSAL PECKING (Cycle 205)
Cycle run
1 The TNC positions the tool in the tool axis at rapid traverse
FMAX to the entered set-up clearance above the workpiece
surface.
2 If you enter a deepened starting point, the TNC move at the
defined positioning feed rate to the set-up clearance above the
deepened starting point.
3 The tool drills to the first plunging depth at the entered feed rate
F.
4 If you have programmed chip breaking, the tool then retracts
by the entered retraction value. If you are working without
chip breaking, the tool is moved at rapid traverse to the set-up
clearance, and then at
FMAX to the entered starting position
above the first plunging depth.
5 The tool then advances with another infeed at the programmed
feed rate. If programmed, the plunging depth is decreased after
each infeed by the decrement.
6 The TNC repeats this process (2 to 4) until the programmed
total hole depth is reached.
7 The tool remains at the hole bottom—if programmed—for
the entered dwell time to cut free, and then retracts to set-up
clearance at the retraction feed rate. If programmed, the tool
moves to the 2nd set-up clearance at
FMAX.
Please note while programming:
Program a positioning block for the starting point
(hole center) in the working plane with radius
compensation
R0.
The algebraic sign for the cycle parameter DEPTH
determines the working direction. If you program
DEPTH=0, the cycle will not be executed.
If you enter different advance stop distances for
Q258 and Q259, the TNC will change the advance
stop distances between the first and last plunging
depths at the same rate.
If you use
Q379 to enter a deepened starting point,
the TNC merely changes the starting point of the
infeed movement. Retraction movements are not
changed by the TNC, therefore they are calculated
with respect to the coordinate of the workpiece
surface.