Drive plc, Appendix, 6 code table – Lenze Global Drive PLC Developer Studio User Manual
Page 101
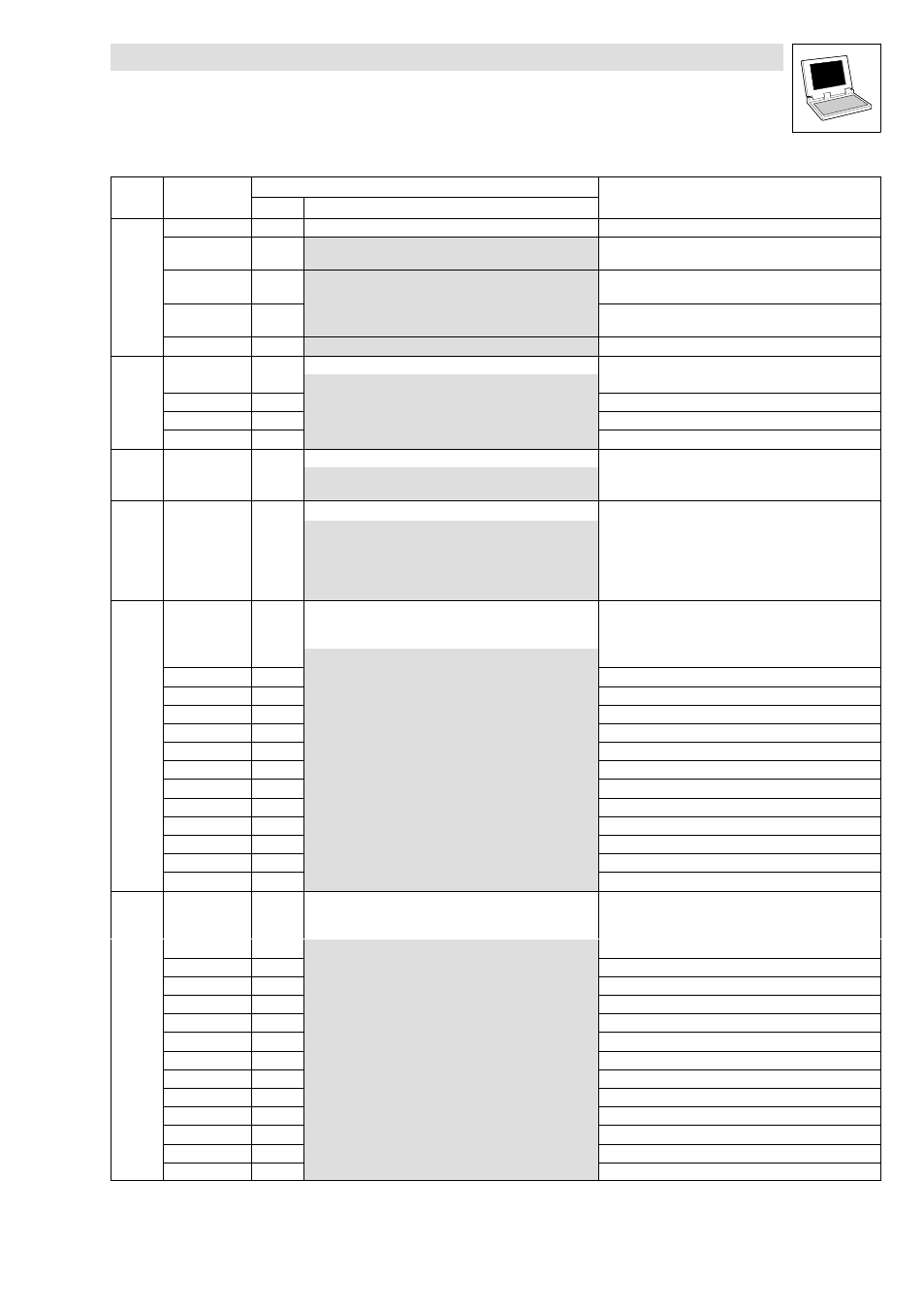
Drive PLC
Appendix
8.6
Code table
8−21
L
DrivePLC DE 6.0
Code
Info
Possible settings
LCD
Code
Info
Selection
Lenze
LCD
C0356 CAN boot up
System bus: Time settings
1
3000
0
{1 ms}
65000 Delay time after power−on for initialisation through the
"quasi" master.
2
0
0
{1}
65000
0 = Event−controlled transmission
Task time factor for sending the CAN2_OUT process data
object.
3
0
Task time factor for sending the CAN3_OUT process data
object.
4
20
0
{1 ms}
65000 Delay time for sending the process data object.
C0357 CE monit time
System bus: Monitoring time for process data input objects
0
{1 ms}
65000
1
3000
CE1monit time
2
3000
CE2monit time
3
3000
CE3monit time
C0358 Reset node
0
System bus: Reset node
0
No function
1
CAN reset node
C0359 CAN state
g
System bus: Status
0
Operational
1
Pre−operational
2
Warning
3
Bus off
4
Stopped
C0360 CAN message
g
System bus: Telegram counter
(number of telegrams)
·
For values > 65535 counting restarts with 0
0
{1 ms}
65535
1
All sent (without free CAN objects)
2
All received (without free CAN objects)
3
Sent to CAN1_OUT
4
Sent to CAN2_OUT
5
Sent to CAN3_OUT
6
Sent to parameter data channel 1
7
Sent to parameter data channel 2
8
Received by CAN1_IN
9
Received by CAN2_IN
10
Received by CAN3_IN
11
Received by parameter data channel 1
12
Received by parameter data channel 2
C0361 Load IN/OUT
g
System bus: Bus load
·
Trouble−free operation demands that the total bus load
(all connected devices) does not exceed 80 %.
0
{1 %}
100
1
All sent (without free CAN objects)
2
All received (without free CAN objects)
3
Sent to CAN1_OUT
4
Sent to CAN2_OUT
5
Sent to CAN3_OUT
6
Sent to parameter data channel 1
7
Sent to parameter data channel 2
8
Received by CAN1_IN
9
Received by CAN2_IN
10
Received by CAN3_IN
11
Received by parameter data channel 1
12
Received by parameter data channel 2