IAI America ERC2 User Manual
Page 81
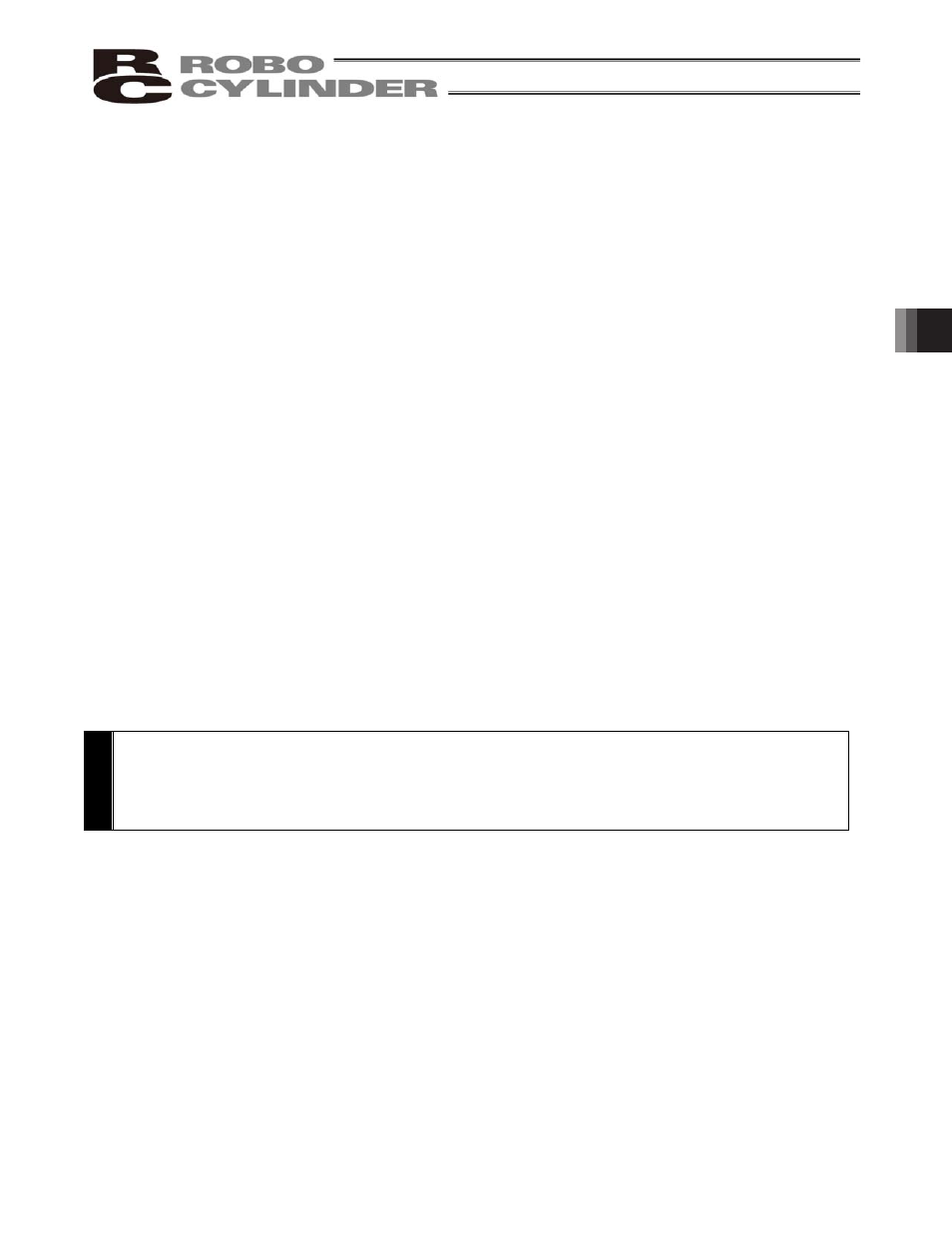
5. Explanation of Operating Functions
62
[1] Specification of push & hold mode
x
Set a value (current-limiting value) “other than 0” in the “Push” field of the position table.
x
To specify the push & hold mode numerically, set bit 0 of the control flag specification register CTLF to “1.”
[2] Push speed
Set a desired push speed in parameter No. 34 (Push speed).
(An appropriate push speed has been set at the factory in accordance with the actuator model.)
[3] Maximum push amount
x
Set a desired amount in the “Positioning band” field of the position table.
x
To specify the maximum push amount numerically, set the applicable value in the positioning band
register (INP).
(Consider a position error that may generate when installing the work part, and if the work part is made of
elastic material, also consider a possible deflection.)
[4] Push direction
x
The push direction is specified by the sign in the “Positioning band” field of the position table.
x
To specify the push direction numerically, set bit 1 of the control flag specification register CTLF to “0” or
“1.”
[5] Push & hold completion judgment
x
Push & hold completion judgment is made based on the generated motor torque (push force) and push
time.
x
Set the push force as a current-limiting value (%) in the “Push” field of the position table. To specify the
push force numerically, set the applicable value in the push-current limiting value during push & hold
operation register (PPOW).
* Determine an appropriate push force based on the characteristics (shape, material, etc.) of the work part,
and then determine the corresponding current-limiting value using the relation diagram of “push force and
current-limiting value” for the applicable actuator.
x
Set the push & hold stop judgment period in parameter No. 6.
(The factory setting is 255 msec.)
[6] Continuous push & hold
x
Although the position complete signal turns “1” once a completion of push & hold operation is recognized,
the actuator will perform the push & hold operation continuously until the next movement command is
issued (command position number and positioning start signals are output).
W
ar
ni
ng
x
If the actuator contacts the work part before reaching the target position, a servo error alarm will
generate. Pay due attention to the position relationship of the target position and the work part.
x
Even when the actuator appears stationary, it actually continues to push the work part at the push force
determined by the current-limiting value. Since the actuator is not physically stopped, exercise due
caution when handling any actuator-related operation during this period.