IAI America ERC2 User Manual
Page 110
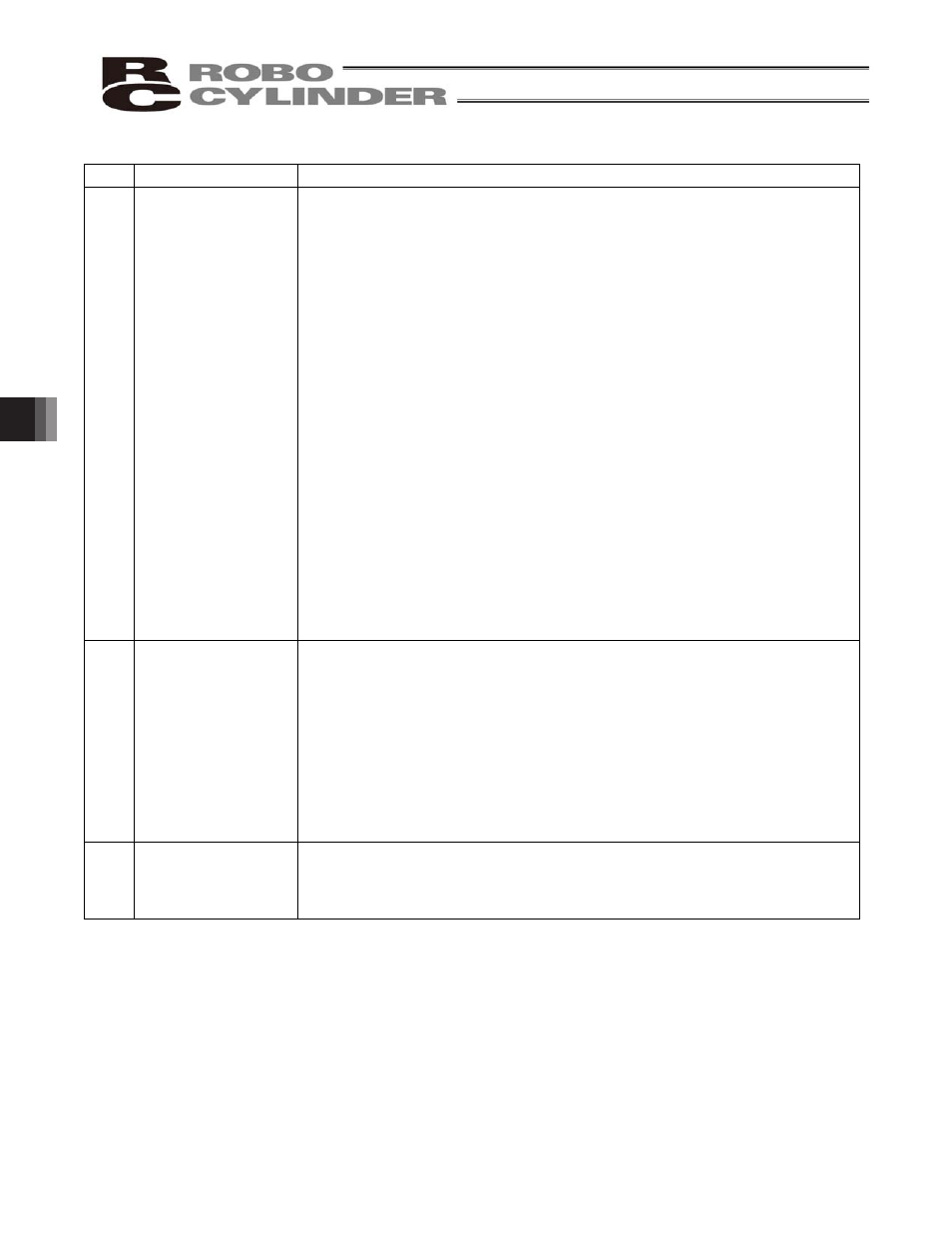
00
7. T
roubleshooting
91
(2) Cold-start level alarms
Code
Error name
Cause/Action
0B8 Excitation detection
error
This controller detects excited phase when the servo is turned on for the first
time after a power on. This alarm indicates that the specified encoder signal
level cannot be detected after the specified period of excitation.
Cause: [1] Loose or disconnected connector of the motor extension cable
[2] The brake cannot be released (if the actuator is equipped with a
brake).
[3] A large load is applied due to an external force.
[4] The power was turned on when the actuator was contacting a
mechanical end.
[5] The slide resistance of the actuator itself is large.
Action: [1] Check the wiring condition of the motor extension cable.
[2] Check the wiring condition of the brake cable, and also turn on/off
the brake release switch to check if a “click” sound is heard.
[3] Check for abnormality in the assembly condition of mechanical
parts.
Increasing the value of parameter No. 29 (Excited-phase signal
detection time) may be effective.
If you wish to change the parameter setting, contact IAI beforehand.
[4] Move the actuator away from the mechanical end, and then turn on
the power again.
Alternatively, change the value of parameter No. 28 (Default
direction of excited-phase signal detection).
[5] If the load weight is normal, turn off the power and move the
actuator by hand to check the slide resistance.
If the actuator is suspected to be faulty, please contact IAI.
0D8 Deviation overflow
The position deviation counter has overflowed.
Cause: [1] The speed dropped due to external force, etc., while the actuator
was moving.
[2] Unstable excitation detection operation after the power has been
turned on
Action: [1] Check the load condition, such as if the work part is contacting any
object around it or the brake is released, and remove the identified
cause.
[2] An overload condition is suspected, so review the load weight.
After appropriate adjustment has been made, reconnect the power
and perform home return.
0DC Out-of-range error in
push & hold operation
This alarm occurs when the actuator was pushed back to the target position
after completion of push & hold operation, due to a strong push-back force of
the work part.
Review the overall settings of the system.