IAI America ERC2 User Manual
Page 108
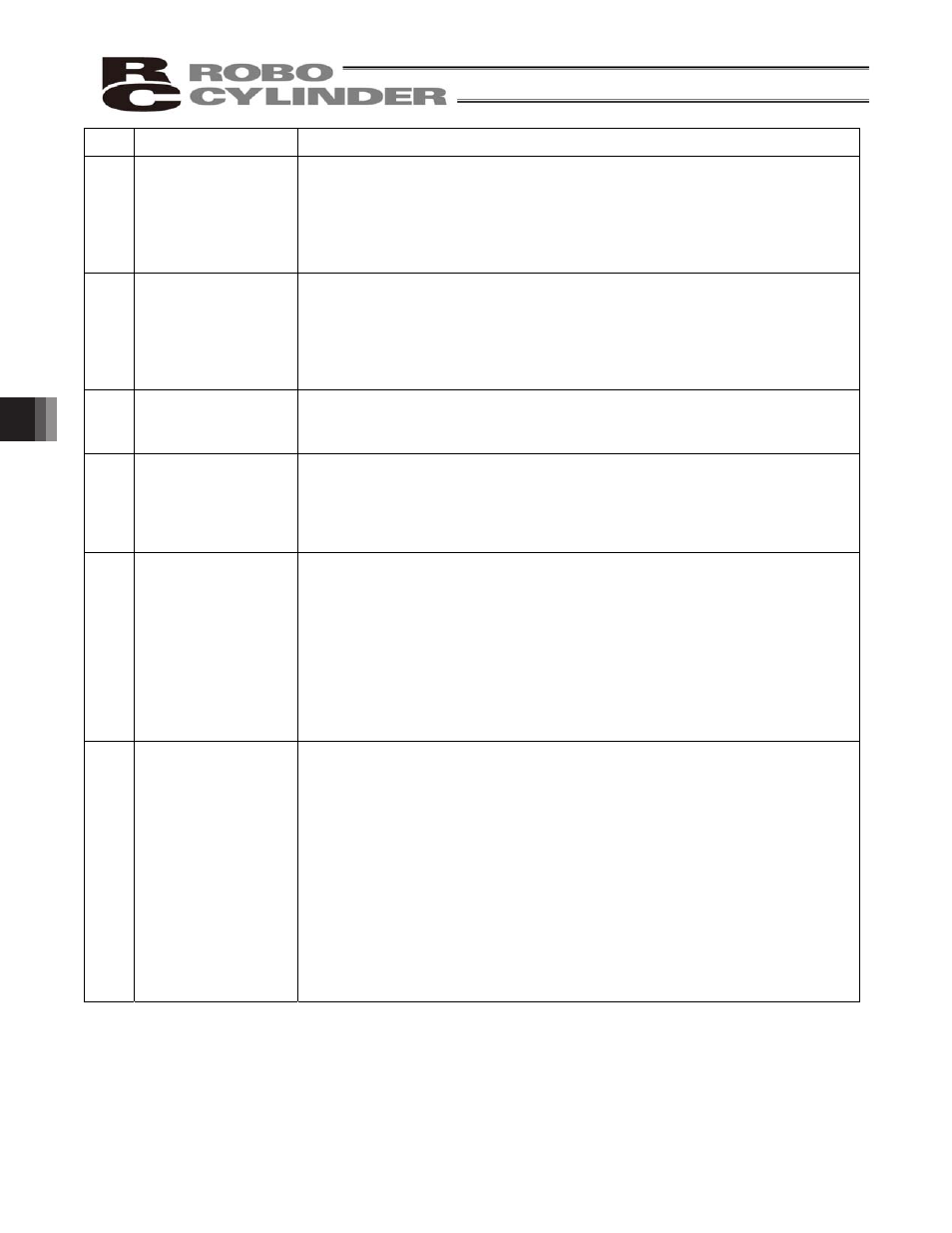
7. T
roubleshooting
89
Code
Error name
Cause/Action
0A1 Parameter data error Cause: The parameter data does not meet the specified input range.
(Example) This alarm generates when a pair of values clearly has an
inappropriate magnitude relationship, such as when the soft
limit + setting is 200.3 mm, while the soft limit – setting is
300 mm.
Action: Change the settings to appropriate values.
0A2 Position data error
Cause: [1] A movement command was input when a target position was not yet
set in the “Position” field.
[2] The target position in the “Position” field is outside the soft limit
range.
Action: [1] Set a target position first.
[2] Change the target position to a value inside the soft limit range.
0A3 Position command
data error
Cause: The speed or acceleration/deceleration specified in the numerical
command exceeds the maximum value that can be set.
Action: Change the applicable setting to an appropriate value.
0BE Home return timeout Cause: Home return does not complete within the period set in the applicable
system parameter after the start of home return operation.
(This alarm should not occur in normal operations.)
Action: Inappropriate controller/actuator combination is a possible cause.
Contact IAI.
0C0 Excessive actual
speed
Cause: This alarm indicates that the motor speed exceeded the maximum
speed set in the applicable system parameter.
This alarm will not generate in normal operation, but may occur in the
following conditions:
[1] Large actuator slide resistance in certain area, or
[2] Instantaneous increase in load due to application of external force,
which may cause the load to decrease and actuator to move rapidly
before a servo error is detected.
Action: Check for abnormality in the assembly condition of mechanical parts.
If the actuator is suspected to be the cause, please contact IAI.
0C1 Servo error
This alarm indicates that after receiving a movement command the motor is
unable to operate for two seconds or more before reaching the target position.
Cause: [1] Loose or disconnected connector of the motor extension cable
[2] Brake cannot be released on a controller equipped with brake.
[3] Large load due to application of external force
[4] Large slide resistance of the actuator itself
Action: [1] Check the wiring condition of the motor extension cable.
[2] Check the wiring condition of the brake cable, and also turn on/off
the brake release switch to check if a “click” sound is heard.
[3] Check for abnormality in the assembly condition of mechanical
parts.
[4] If the load weight is normal, turn off the power and move the
actuator by hand to check the slide resistance.
If the actuator is suspected to be the cause, please contact IAI.