IAI America ERC2 User Manual
Page 103
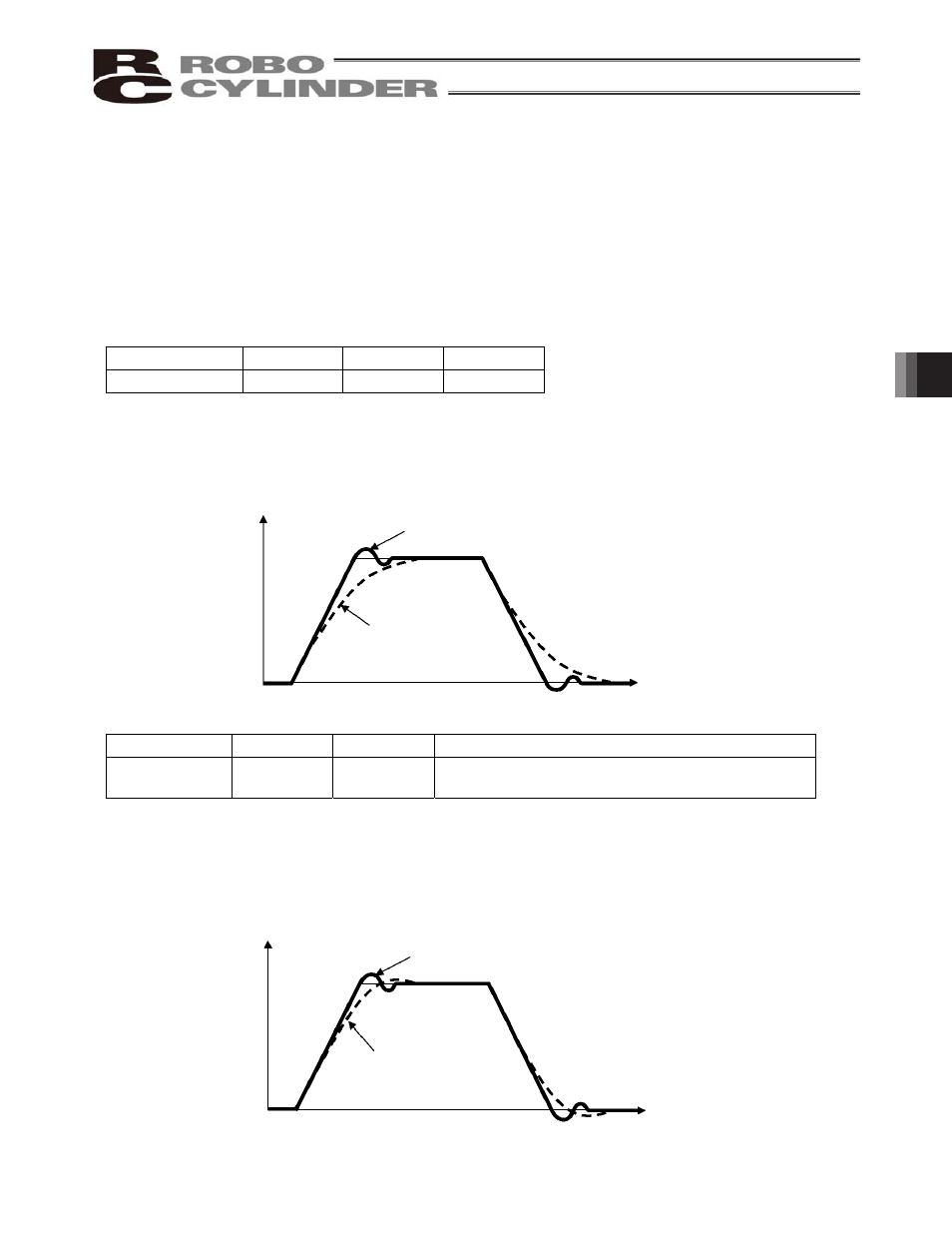
6. Parameter Settings
84
6.2.4 Servo Gain Adjustment
Before the shipment, the servo has been adjusted in accordance with the standard specification of the actuator.
Accordingly, the servo settings need not be changed in normal conditions.
Nonetheless, the parameters relating to servo adjustment are made accessible by the customer so that speedy
actions can be taken in situations where vibration or noise occurs due to the affixing method of the actuator, load
condition, or the like.
In particular, custom types (having a longer ball screw lead or stroke than standard types) are more vulnerable to
vibration and noise due to external conditions.
In such a case, the following parameter settings must be changed. Contact IAI beforehand.
z
Servo gain number (No.7 PLG0)
Parameter No.
Unit
Input range
Default
7
5 rad/sec
0 ~ 31
6
This parameter determines the response when a position control loop is used.
Increasing the set value improves the tracking performance with respect to the position command.
However, increasing the value excessively increases the chances of overshoot.
If the value is small, the tracking performance with respect to the position command drops and positioning takes
a longer time.
z
Speed loop proportional gain (No.31 VLPG)
Parameter No.
Unit
Input range
Default
31
---
1 ~ 27661
Set individually in accordance with the actuator
characteristics.
This parameter determines the response when a speed control loop is used.
Increasing the set value improves the tracking performance with respect to the speed command (i.e., servo
rigidity increases).
The greater the load inertia, the larger this value should be.
However, increasing the value excessively makes the actuator more vulnerable to overshooting or shaking,
leading to mechanical vibration.
Speed
Set value is large (overshoot)
Set value is small
Time
Speed
Set value is large (overshoot)
Set value is small
Time