3 differences from air cylinder control – IAI America ERC2 User Manual
Page 21
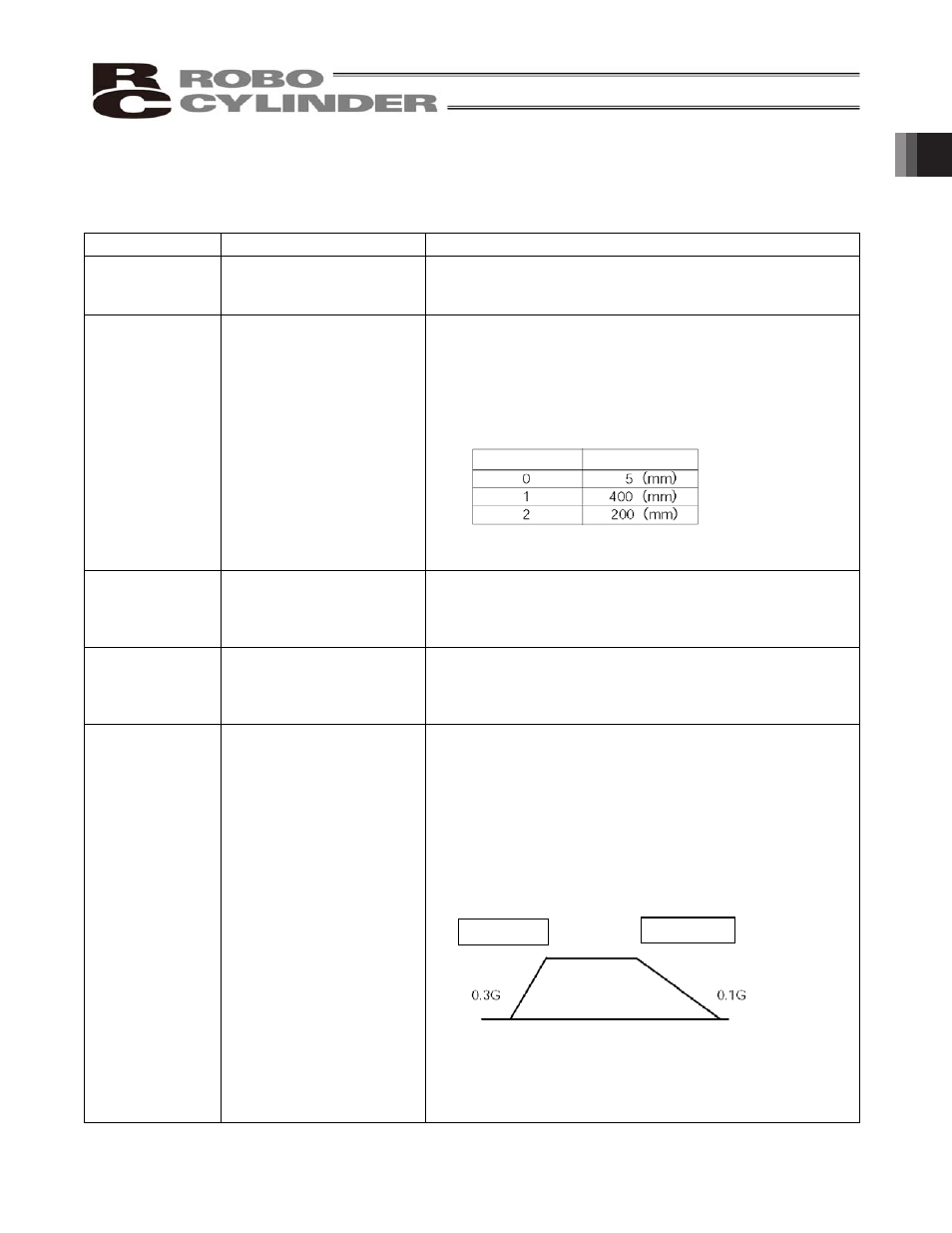
1. Overview
3
1.3 Differences from Air Cylinder Control
This section explains the key differences between an air cylinder and this controller for users who are familiar
with air cylinders but have never used a motorized cylinder before.
Refer to the table below to perform appropriate controls.
Item
Air cylinder
This controller
Drive method
Driven by air pressure
based on electromagnetic
valve control.
Driven by a ball screw or timing belt using a pulse motor.
Target position
setting
Mechanical stopper
(including a shock absorber)
[1] Position number specification mode
Enter a coordinate in the [Position] field of the position table.
You can key in a desired coordinate using the number keys
on a PC (keyboard)/teaching pendant, or move the actuator
to a desired position and then write the coordinate to the
position table directly.
Example) Entries on a 400-mm actuator
[2] Numerical specification mode: Specify a desired value
directly.
Target position
detection
A reed switch or other
external detection sensor is
installed.
Whether or not the target position has been reached is
determined based on the internal coordinate information
received from the position detector (encoder).
Accordingly, no external detection sensor is required.
Speed setting
Adjusted using a speed
controller.
[1] Enter a feed speed in the [Speed] field of the position
table (in mm/sec).
Initially, the default speed has been set automatically.
[2] Specify a desired value directly.
Acceleration/
deceleration
setting
In accordance with the load,
air supply volume, and
speed
controller/electromagnetic
valve performance.
[1] Enter an acceleration or deceleration in the [Acceleration]
or [Deceleration] field of the position table (in units of 0.01
G).
Reference: 1 G = Gravitational acceleration that generates
when the actuator drops freely.
Initially, the default acceleration and deceleration have been
set automatically.
[2] Specify a desired value directly.
Since acceleration and deceleration can be set finely, you
can define a gradual deceleration/acceleration curves.
Larger acceleration/deceleration values set steeper curves,
while smaller acceleration/deceleration values set more
gradual curves.
Position No.
Position
Acceleration
Deceleration
Movement
start position
End position