IAI America ERC2 User Manual
Page 78
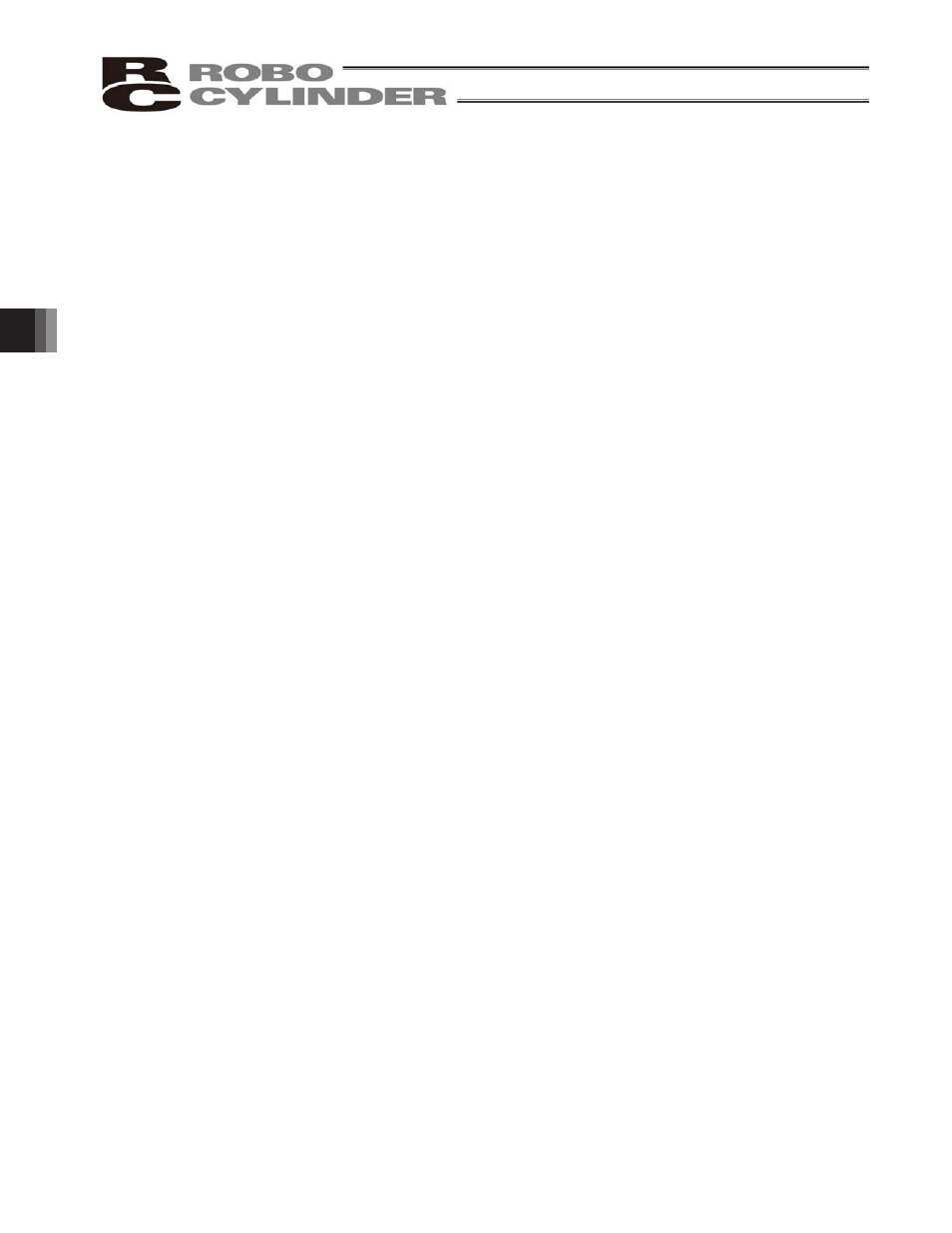
5. Explanation of Operating Functions
59
Positioning start (CSTR)
Upon detecting the “0” o “1” leading edge of this signal bit, the controller will read the target position number
specified by a binary code consisting of six bits from PC1 to PC32 (in the position number specification register)
and cause the actuator to move to the target position of the corresponding position data.
Before positioning is performed, however, the target position, speed and other operation data must be set in the
position table using a PC/teaching pendant.
If this command is issued when home return operation has never been performed (= the HEND output signal bit
is “0”) after the power was turned on, the actuator will perform home return operation automatically and then
move to the target position.
Moving (MOVE)
This signal is output while the actuator is moving (also during home return, push & hold operation and jogging)
with the servo turned on.
Use this signal together with PEND to determine the actuator status from the PLC side.
This signal bit will turn “0” upon completion of positioning, upon completion of home return, after push & hold
completion judgment during push & hold operation, and during pause.
Command position number (PC1 to PC32)
When a moving command is executed at the “0” o “1” edge of the CSTR signal bit, a binary code specified by
six signal bits from PC1 to PC32 will be read as the command position number.
Completed position number (PM1 to PM32)
These signals can be used to check the completed position number effective when the PEND signal bit has
turned “1.”
These signals are output as a binary code in the position number status register.
Immediately after the power has been turned on, all signal bits from PM1 to PM32 are “0.”
All bits remain “0” while the actuator is moving.
As evident from the above explanation, these signals are output only upon completion of positioning.
Although all signal bits will turn “0” when the servo is turned off or an emergency stop is actuated, the bits will
return to “1” when the servo is turned on again, if the actuator is inside the positioning band with respect to the
target position. If the actuator is not inside the positioning band, the signal bits will remain “0.”
These bits will also turn “1” when the push & hold completion judgment signal has turned ON, or the actuator has
missed the work part, during push & hold operation.