5 push & hold operation – IAI America ERC2 User Manual
Page 80
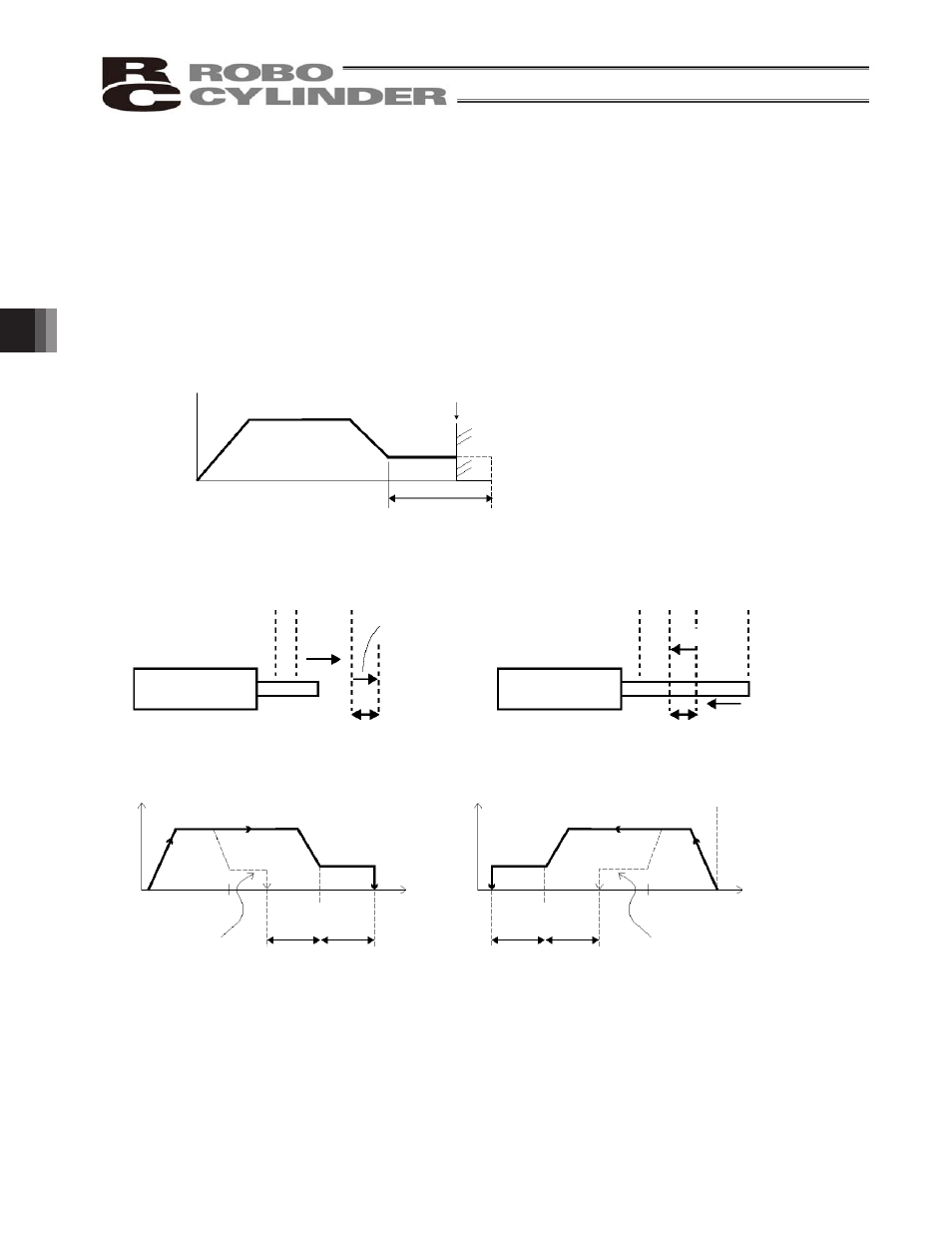
0
5. Explanation of Operating Functions
61
5.3.5 Push & Hold Operation
Just like with an air cylinder, the end of the rod can be pressed against a work part and maintained in this
condition.
The push & hold operation is useful in clamping or press-fitting of work parts.
(1) Basic operation
As shown below, the actuator moves to the specified target position, after which it will move at the specified push
speed to push the work part over a distance up to the specified positioning band.
If the push force reaches a certain level while the actuator is still pushing the work part, the controller will
recognize that push & hold operation has completed and change the position complete signal bit to “1.”
x
Definition of push direction
As shown above, the push direction is positive (+) when the actuator pushes the work part in the direction of
increasing coordinate value from the starting point toward the target position, whereas the push direction is
negative (-) when the actuator pushes the work part in the direction of decreasing coordinate value. Here,
exercise caution because setting a wrong push direction will prevent the actuator from operating correctly;
specifically, the actuator will perform push & hold operation only for twice the positioning band at the starting
point.
Target position
Speed
Travel
Positioning band (Maximum push amount)
The actuator contacts the load and the position
complete signal turns ON here because push &
hold operation is deemed to have completed.
Push speed
Actuator
Actuator
Home
Starting
point
Home
Starting
point
Positioning band
(Sign +)
Push direction
Positioning band
(Sign -)
Speed
Speed
X When the negative
sign (-) is set
Target
Target
Position
Position
X When the positive
sign (+) is set
Positioning
band
Positioning
band
Positioning
band
Positioning
band
Starting
point
Starting
point
Push direction
Target
point
Target
point