HEIDENHAIN iTNC 530 (340 49x-04) Touch Probe Cycles User Manual
Page 167
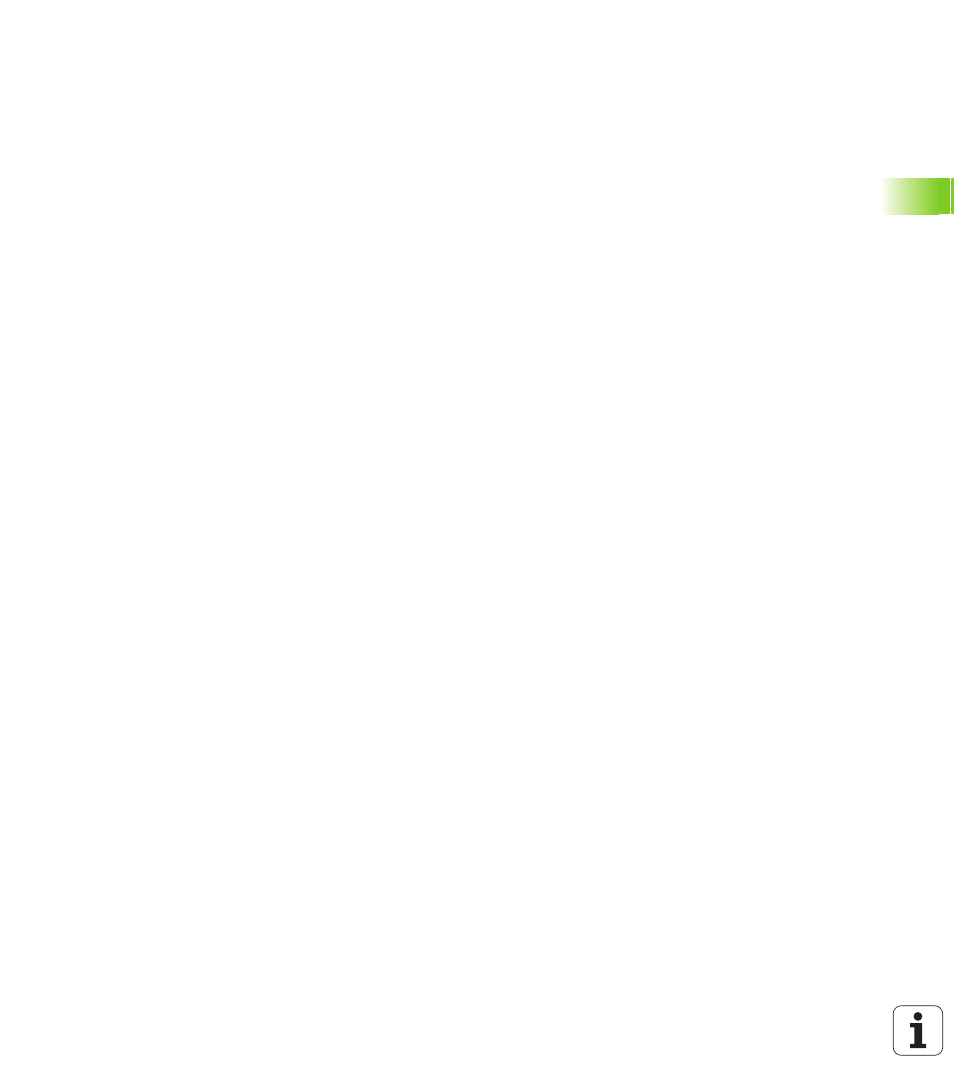
HEIDENHAIN iTNC 530
167
4.1 Kinematic Measur
ement with TS
T
ouc
h Pr
obes (Option KinematicsOpt)
Notes on various calibration methods
Rough optimization during commissioning after entering
approximate dimensions.
Number of measuring points between 1 and 2
Angular step of the rotary axes: Approx. 90°
Fine optimization over the entire range of traverse
Number of measuring points between 3 and 6
The start and end angles should cover the largest possible
traverse range of the rotary axes
Position the calibrating ball on the machine table so that on rotary
table axes there is a large measuring circle, or so that on swivel
head axes the measurement can be made at a representative
position (e.g. in the center of the traverse range).
Optimization of a specific rotary axis position
Number of measuring points between 2 and 3
The measurements are made near the rotary axis angle at which
the workpiece is to be machined
Position the calibration ball on the machine table for calibration at
the position subsequently intended for machining
Inspecting the machine accuracy
Number of measuring points between 4 and 8
The start and end angles should cover the largest possible
traverse range of the rotary axes
Determining the rotary axis backlash during inspection
Number of measuring points between 8 and 12
The start and end angles should cover the largest possible
traverse range of the rotary axes