2 high-pressure pump – Metrohm 792 Basic IC User Manual
Page 149
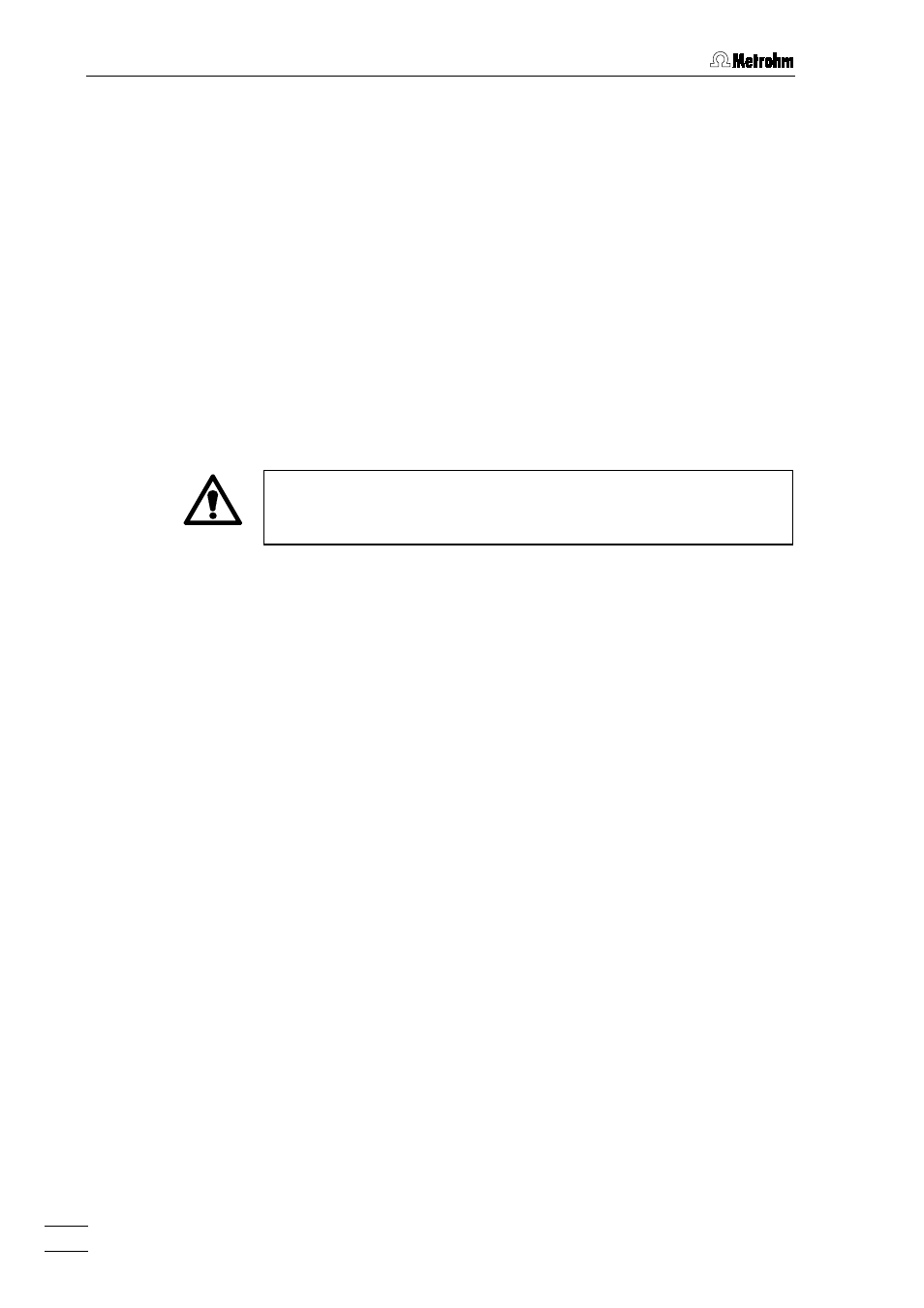
5 Notes – Maintenance – Faults
792 Basic IC
140
Storage
Always store the separating columns closed when not in use and filled
in accordance with the manufacturer’s specifications.
Dead volume
Dead volume at the end of a column can be the cause of extreme peak
broadening or splitting (appearance of double peaks). Filling the col-
umn with glass beads ( d 100 Pm) frequently improves the separation
efficiency.
Regeneration
If the separation properties of the column have deteriorated, it can be
regenerated in accordance with the column manufacturer’s specifica-
tions. With the separating columns available from Metrohm (see sec-
tion 6.3.2), the instructions for regeneration can be found on the leaflet
enclosed with every column.
In the case of separating columns with carrier material based on silica,
only solutions with pH 2}
}
}
}7 may be used for regeneration, other-
wise the columns could be damaged.
5.1.2 High-pressure
pump
Pulsation dampener
The use of the optional
6.2620.150 Pulsation dampener MF is rec-
ommended to protect sensitive separating columns (e.g. methacrylate
based columns). It is used to reduce interfering pulsation in highly sen-
sitive measurements and also protects the column material against
pressure shocks caused by the injection. Its installation is described in
section 2.6.2.
Maintenance
To protect the pump against foreign particles, we advise you to subject
the eluent to
microfiltration (0.45 Pm filter) and siphon the eluent
through the
6.2821.090 Aspirating filter.
In many cases, an unstable baseline (pulsation, flow fluctuations) can
be traced to contaminated valves or faulty, leaky piston seals.
Contaminated valves are cleaned by rinsing with water, RBS solution
or acetone (see section 5.2.6). When the cleaned valves are reinstalled,
you must ensure that the flow direction is correct.
The
replacement of piston seals is described in section 5.2.6.
Salt crystals between the piston and the seal are the cause of abrasive
particles, which can enter the eluent. These lead to contaminated
valves, pressure rise and in extreme cases to scratched pistons. It is
thus essential to ensure that
no precipitates can appear (see also
section 5.1.3).