Terminations, Requirements for smc connectors – Northern Connectors Harting DIN 41 612 Connectors User Manual
Page 28
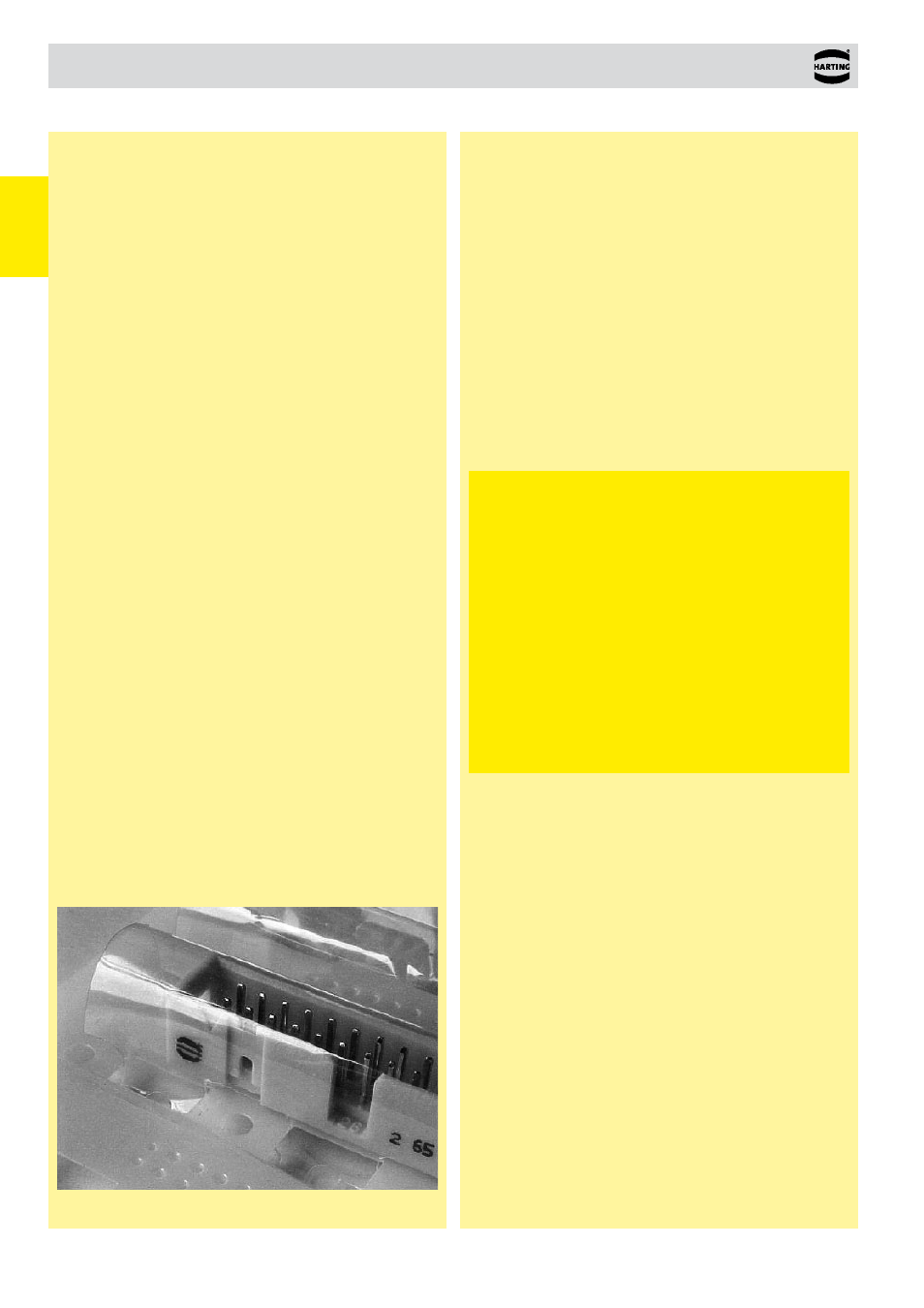
00
.
22
Gen
er
al
in
fo
rma
tio
n
Terminations
Requirements for SMC connectors
SMC (Surface Mount Compatible) connectors have to withstand
temperatures of up to 240 °C in the reflow oven for 10 to 15 se-
conds. Therefore, the moulding must be made from a dimensio-
nally stable plastic which expands at the same rate as the pcb
material when subjected to heat.
The length of the connector contacts should be such that they
protrude by no more than 1.5 millimetres after insertion to the pcb.
Each contact collects solder on its tip as it penetrates the solder
paste in the hole. So if the contact was too long, this solder would
no longer be able to reflow back into the plated through hole by
capillary action during the soldering process, therefore the quality
of the soldered connection would suffer as a result.
Connector design must permit both automatic
assembly with
pick-and-place machines and manual positioning for test and pre-
production batches. It is also important for the packaging of the
connectors to be suitable for automated assembly. Experience
shows that deep-drawn film and reel packaging fed into the pick-
and-place machines with the aid of a conveyor system is particu-
larly suitable.
HARTING SMC technology
HARTING offers its customers a complete system concept for in-
tegrating SMC technology into existing production lines. We ma-
nufacture a wide range of SMC connectors (3 and 5 row) in com-
pliance with IEC 60603-2, D-Sub connectors in compliance with
IEC 60807 and connectors from the har-mik® series with contact
spacing of 1.27 millimetres. In addition, HARTING supports the
market with packaging and processing concepts, which have been
developed in collaboration with renowned manufacturers of SMC
soldering and assembly plants.
Advantages of the “Pin in Hole Intrusive
Reflow” process:
• Partial dip soldering or press fitting is no
longer required
• Complete compatibility with Surface Mount
Technology
• Complete integration into the automated
assembly process
• Reduced floor space in the production plant
• As a rule, no additional investment costs
Fig. 5: HARTING connector mounted in a tape ready
for placement using an odd form assembly station.