Terminations – Northern Connectors Harting DIN 41 612 Connectors User Manual
Page 26
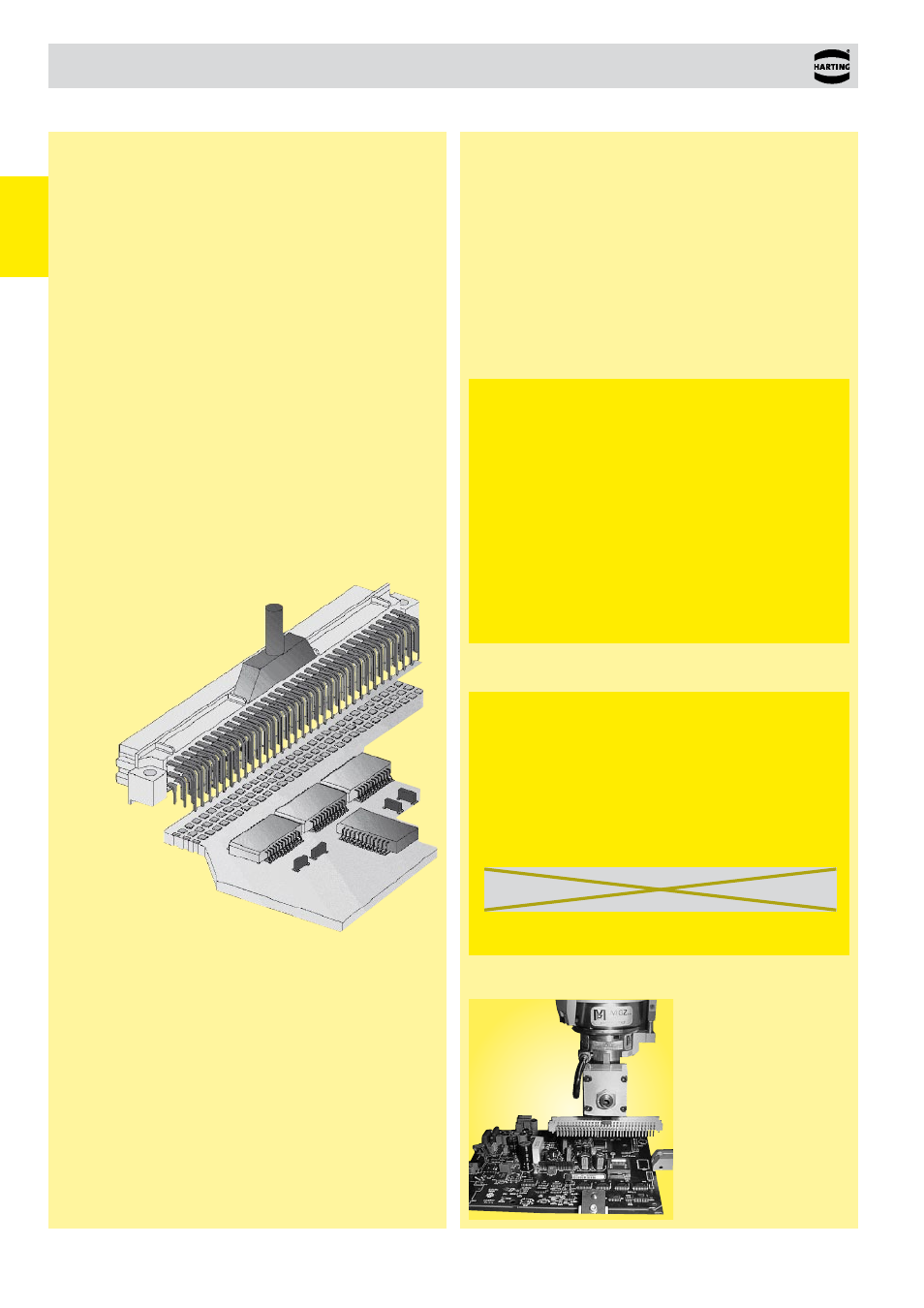
00
.
20
Gen
er
al
in
fo
rma
tio
n
Terminations
THT soldering technology
The term "soldering" is defined in DIN 8505:
"Soldering is a method of connecting metallic materials
using an additional melting metal, if necessary with the as-
sistance of a flux and/or protective gas. The melting tempe-
rature of the solder must lie beneath the minimum melting
temperature of the base metals being connected. These
base metals shall be tinned without melting themselves."
Soft solders commonly used on electronic equipment are to
DIN 1707-100. Todays lead free solders have a melting range
between 217 °C and 227 °C depending on the composition of the
alloy. For soldering metallic materials the flux is defined in DIN
EN 29 454-1. Tests are explained in DIN 8526. For soldering male
connectors into printed circuit boards, see recommendations for
soldering on page 00.06.
SMC soldering technology
The continuing trend towards miniaturisation has
revolutionised the assembly of electronic components. For the
past 15 years, most components have been secured directly
to the pcb surface by means of Surface Mount Technology
(SMT). By dispensing with drilled holes on the pcb, a space
saving of up to 70 percent is achieved.
Today, typical components such as resistors, ICs, capacitors, and
connectors with straight terminal pins are almost exclusively fitted
using SMD (Surface Mount Device) technology in mass production.
In contrast, angled SMD connectors at the edge of the board have
not been successful because of tolerance problems (co-planarity)
and stresses during mating. Modified solder connectors for
assembly with "Pin in Hole Intrusive Reflow" process offer a better
solution. These can be mounted at low cost, utilising existing SMD
production lines.
“Pin in Hole Intrusive Reflow”
In this process, the connector is inserted into plated through holes
in a comparable way to conventional component mounting. All
other components can be assembled on the pcb surface.
Fig. 1:
SMT board with connector for
"Pin in Hole Intrusive Reflow" assembly
Fig. 2:
Pick-and-place machine for
odd form components
(Courtesy of JOT Automation GmbH)
The components are positioned using pick-and-place machines.
These automatic assembly machines differ according to whether
the components are small, lightweight or bulky. Connectors are
considered bulky (odd form) because of their comparatively heavy
weight and large volume which makes them more difficult to grip.
Furthermore, machines for odd form components must have
higher insertion power to fit the components into pcb holes, which
are filled with solder paste. As a rule, modern SMC production
lines are equipped with both types of machine, therefore the
"Pin in Hole Intrusive Reflow" process generally entails no extra
investment costs for the user.
Conventional assembly process:
1. Application of solder paste
2. Positioning the components
3. Positioning odd form components
4. Reflow soldering
5. Pressing in or partially dip soldering the
connector at the board edge
6. Quality inspection
“Pin in Hole Intrusive Reflow” assembly:
1. Application of solder paste
2. Positioning the components
3. Positioning odd form components
4. Reflow soldering
5. Pressing in or partially dip soldering the
connector at the board edge
6. Quality inspection