Device protection, Motor protection, Wiring of the standard device – Lenze EVS9332xS User Manual
Page 78
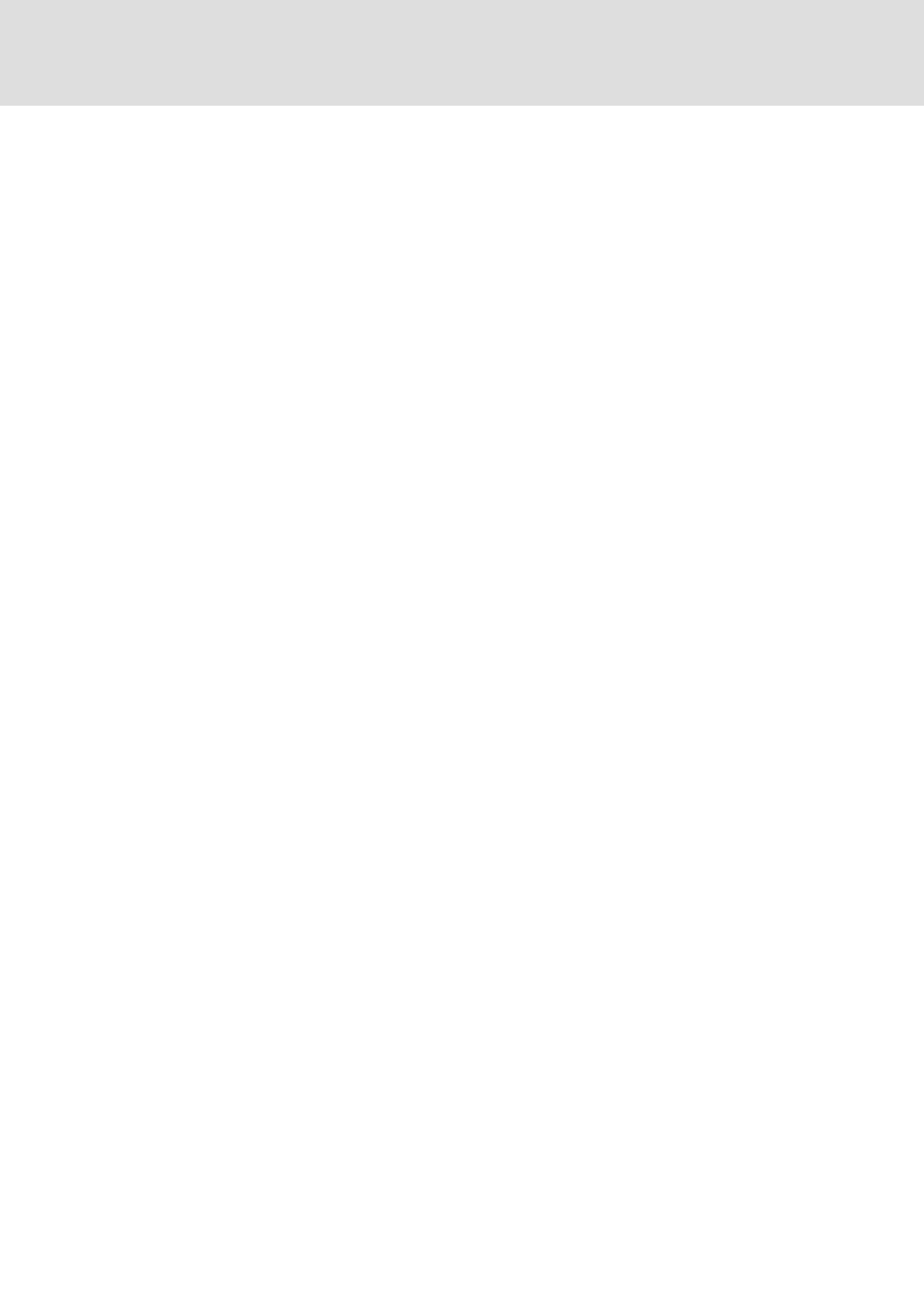
Wiring of the standard device
Important notes
Device protection
5.1
5.1.2
l
5.1−3
EDSVS9332S EN 6.0−07/2013
5.1.2
Device protection
ƒ In the event of condensation, only connect the controller to the mains
voltage after the humidity has evaporated.
ƒ The controller is protected by external fuses.
ƒ Drive controllers EVS9324−xS, EVS9326−xS and
EVS9328−xS ... EVS9332−xS must only be operated with assigned mains
choke / mains filter.
ƒ Length of the screws for connecting the shield sheet for the control
cables: 12 mm.
ƒ Provide unused control inputs and outputs with terminal strips. Cover
unused Sub−D sockets with protective covers included in the scope of
supply.
ƒ Switching on the motor side of the controller is only permissible for
safety shutdown (emergency−off).
ƒ Frequent mains switching (e.g. inching mode via mains contactor) can
overload and destroy the input current limitation of the drive
controller:
– At least 3 minutes must pass between switching off and restarting
the devices EVS9321−xS and EVS9322−xS.
– At least 3 minutes must pass between two starting procedures of the
devices EVS9323−xS ... EVS9332−xS.
– Use the "safe torque off" safety function (STO) if safety−related mains
disconnections occur frequently. The drive variants Vxx4 are
equipped with this function.
5.1.3
Motor protection
ƒ Extensive protection against overload:
– By overcurrent relays or temperature monitoring.
– We recommend the use of PTC thermistors or thermostats to monitor
the motor temperature.
– PTC thermistors or thermostats can be connected to the controller.
– For monitoring the motor, we recommend the use of the I
2
xt
monitoring.
ƒ Only use motors with an insulation suitable for the inverter operation:
– Insulation resistance: min. û = 1.5 kV, min. du/dt = 5 kV/
ms
– When using motors with an unknown insulation resistance, please
contact your motor supplier.